IDEC CORPORATION FC2A-KM1C
Specifications
Manufacturer
IDEC Corporation
Manufacturers Part #
FC2A-KM1C
Sub-Category
Multi-Conductor Cables
Factory Pack Quantity
1
Datasheet
Extracted Text
3 MICRO C PLC User’s Manual SAFETY PRECAUTIONS • Read this user’s manual to make sure of correct operation before starting installation, wiring, operation, maintenance, and 3 inspection of the MICRO C. 3 • All MICRO C’s are manufactured under IDEC’s rigorous quality control system, but users must add a backup or failsafe 3 provision to the control system using the MICRO C in applications where heavy damage or personal injury may be caused in 3 case the MICRO C should fail. • In this user’s manual, safety precautions are categorized in order of importance to Warning and Caution: Warning notices are used to emphasize that improper operation may cause Warning severe personal injury or death. Caution notices are used where inattention might cause personal injury or Caution damage to equipment. Warning 3 3 • Turn power off to the MICRO C before starting installation, removal, wiring, maintenance, and inspection on the MICRO C. Failure to turn power off may cause electrical shocks or Ţre hazard. 3 • Special expertise is required to install, wire, program, and operate the MICRO C. People without such expertise must not use 3 the MICRO C. 3 • Emergency and interlocking circuits must be conŢgured outside the MICRO C. If such a circuit is conŢgured inside the 3 3 MICRO C, failure of the MICRO C may cause disorder of the control system, damage, or accidents. Caution 3 3 • Install the MICRO C according to instructions described in this user’s manual and the MICRO user’s manual. Improper 3 installation will result in falling, failure, or malfunction of the MICRO C. 3 3 • MICRO C is designed for installation in equipment. Do not install the MICRO C outside of equipment. 3 3 3 • Install the MICRO C in environments described in this user’s manual and the MICRO user’s manual. If the MICRO C is used 3 in places where the MICRO C is subjected to high-temperature, high-humidity, condensation, corrosive gases, excessive vibrations, and excessive shocks, then electrical shocks, Ţre hazard, or malfunction will result. 3 3 • MICRO C is designed for use in “Pollution degree 2.” Use the MICRO C in environments of pollution degree 2 (according to IEC664-1). 3 • All DC power type MICRO C units are “PS2” type (according to EN61131). 3 3 • Prevent the MICRO C from falling while moving or transporting the MICRO C, otherwise damage or malfunction of the 3 MICRO C will result. 3 3 • Prevent metal fragments and pieces of wire from dropping inside the MICRO C housing. Put a cover on the MICRO C during installation and wiring. Ingress of such fragments and chips may cause Ţre hazard, damage, or malfunction. • Use a power supply of the rated value. Use of a wrong power supply may cause Ţre hazard. • Use wires of a proper size to meet voltage and current requirements. Tighten M3 terminal screws to a proper tightening torque of 0.3 to 0.5 N-m. 3 • Use an IEC127-approved fuse (2A maximum) on the power line outside the MICRO C. This is required when exporting 3 equipment containing MICRO C to Europe. 3 • Use an IEC127-approved fuse on the output circuit. This is required when exporting equipment containing MICRO C to Europe. 3 • Use an EU-approved circuit breaker. This is required when exporting equipment containing MICRO C to Europe. 3 3 • Make sure of safety before starting and stopping the MICRO C or when operating the MICRO C to force outputs on or off. 3 Incorrect operation on the MICRO C may cause machine damage or accidents. 3 • If relays in the MICRO C output circuit fail, outputs may remain on or off. For output signals which may cause heavy acci- 3 dents, provide a monitor circuit outside of the MICRO C. 3 • Do not connect to the ground directly from the MICRO C. Connect a protective ground to the equipment containing 3 3 MICRO C using an M4 or larger screw. This is required when exporting equipment containing MICRO C to Europe. 3 • Do not disassemble, repair, or modify the MICRO C. 3 • When the battery in the MICRO C is dead, dispose of the battery in accordance with pertaining regulations. When taking back the dead battery to the store or disposing of the dead battery, use a proper container installed for that purpose. This is 3 required when exporting equipment containing MICRO C to Europe. 3 • When disposing of the MICRO C, do so as an industrial waste. • When the battery in the memory card is dead, dispose of the battery in accordance with pertaining regulations. USER’S MANUAL PREFACE-1 3 MICRO C USER’S MANUAL 3 3 This user’s manual primarily describes MICRO C’s additional functions not included in the MICRO programmable control- 3 lers. For installation instructions, general speciŢcations, and common functions shared with the MICRO such as basic and 3 advanced instructions, allocation numbers, and FUN settings, see the MICRO user’s manual. 3 3 MICRO C and MICRO Comparison 3 3 PLC MICRO C MICRO 40 Advanced Instructions 38 (TXD, RXD, CMP2 added; ANR1 deleted) Standard Processing 500 points 100 points Data Registers High-speed Processing 32 points 32 points 1 point (10 I/O type) Analog Potentiometers 1 point 2 points (16/24 I/O types) Loader Port Standards EIA RS232C EIA RS485 Standards EIA RS485 EIA RS485 Communication Expansion/data link communication: Data Link SpeciŢcations 19,200 bps (Ţxed) Expansion/data link communication: Terminal Baud Rate Loader protocol communication: 19,200 bps (Ţxed) 9,600 bps (Ţxed) 290g (10 I/O type) 380g (16 I/O type) 350g (16 I/O type) Weight (approx.) 430g (24 I/O type) 390g (16 I/O AC input type) 400g (24 I/O type) EN55011 Group 1, Class A EN61131-1, EN61131-2, EN60204-1 EN50082-2 IEC801-2, -3, -4 Standards UL508, CSA C22.2, No. 142 PrEN50082-2, EN55011 EN61131-1, EN61131-2, EN60204-1 UL508, CSA C22.2, No. 142 TÜV Product Service E9 95 09 13332 TÜV Product Service B950913332 313 CertiŢcation File No. UL E102542 UL E102542 CSA LR66809 CSA LR66809 3 Program Loader for MICRO C 3 To use the expanded capabilities of the MICRO C such as new advanced instructions for communication and comparison and increased data registers, use an upgraded program loader of version 2.00 or later. To check the program loader version, read FUN31 (program loader version readout/hardware check) using the FUN31 and keys on the program loader. 3 To edit user programs for MICRO C, read FUN11 (program capacity and PLC type selection) on the program loader, and 3 set the fourth line in the FUN11 screen to 1 to select MICRO C as the PLC type, using the FUN11, , , , 1, and keys. 3 3 Since the loader port on the MICRO C uses RS232C communication while the loader port on the MICRO uses RS485, a dif- 3 3 ferent loader cable is needed to connect the program loader to MICRO C or MICRO . Use loader cable 3C (FC2A-KL3C) to 3 connect a program loader to the MICRO C loader port. A program loader can also be connected to the data link terminals on 3 the MICRO C using loader cable 4C (FC2A-KL4C). In either case, loader protocol must be selected for the loader port or data link terminals using the protocol selector switch. For selection of the protocol selector switch, see page 1-2. 3 3 Note: The upgraded program loader of version 2.00 or later can also be connected to the MICRO using MICRO loader cable FC2A-KL1 or FC2A-KL2. IMPORTANT INFORMATION Under no circumstances shall IDEC Corporation be held liable or responsible for indirect or consequential damages resulting from the use of or the application of IDEC PLC components, individually or in combination with other equipment. All persons using these components must be willing to accept responsibility for choosing the correct component to suit their appli- cation and for choosing an application appropriate for the component, individually or in combination with other equipment. All diagrams and examples in this manual are for illustrative purposes only. In no way does including these diagrams and examples in this manual constitute a guarantee as to their suitability for any specific application. To test and approve all pro- grams, prior to installation, is the responsibility of the end user. PREFACE-2 USER’S MANUAL TABLE OF CONTENTS HAPTER 1: GENERAL INFORMATION C Features . . . . . . . . . . . . . . . . . . . . . . . . . . . . . . . . . . . . . . . . . . . . . . . . . . . . . . . 1-1 Parts Description . . . . . . . . . . . . . . . . . . . . . . . . . . . . . . . . . . . . . . . . . . . . . . . . . 1-1 System Setup . . . . . . . . . . . . . . . . . . . . . . . . . . . . . . . . . . . . . . . . . . . . . . . . . . . 1-3 Communication Specifications . . . . . . . . . . . . . . . . . . . . . . . . . . . . . . . . . . . . . . . 1-8 Dimensions . . . . . . . . . . . . . . . . . . . . . . . . . . . . . . . . . . . . . . . . . . . . . . . . . . . 1-10 HAPTER 2: ALLOCATION NUMBERS C Allocation Numbers . . . . . . . . . . . . . . . . . . . . . . . . . . . . . . . . . . . . . . . . . . . . . . . 2-1 I/O Allocation Numbers for Expansion Link System . . . . . . . . . . . . . . . . . . . . . . . . 2-2 Special Internal Relays . . . . . . . . . . . . . . . . . . . . . . . . . . . . . . . . . . . . . . . . . . . . 2-3 Data Register Allocation Numbers . . . . . . . . . . . . . . . . . . . . . . . . . . . . . . . . . . . . 2-4 Expansion Control Data Registers . . . . . . . . . . . . . . . . . . . . . . . . . . . . . . . . . . . . . 2-4 HAPTER 3: COMMUNICATION MONITOR C System Setup . . . . . . . . . . . . . . . . . . . . . . . . . . . . . . . . . . . . . . . . . . . . . . . . . . . 3-1 FUN29: User Communication Status Readout . . . . . . . . . . . . . . . . . . . . . . . . . . . . 3-1 FUN50: User Communication Data Monitor . . . . . . . . . . . . . . . . . . . . . . . . . . . . . . 3-2 HAPTER 4: MODEM MODE C System Setup . . . . . . . . . . . . . . . . . . . . . . . . . . . . . . . . . . . . . . . . . . . . . . . . . . . 4-1 Applicable Modems . . . . . . . . . . . . . . . . . . . . . . . . . . . . . . . . . . . . . . . . . . . . . . . 4-1 Internal Relays for Modem Mode . . . . . . . . . . . . . . . . . . . . . . . . . . . . . . . . . . . . . 4-2 Data Registers for Modem Mode . . . . . . . . . . . . . . . . . . . . . . . . . . . . . . . . . . . . . 4-2 Originate Mode . . . . . . . . . . . . . . . . . . . . . . . . . . . . . . . . . . . . . . . . . . . . . . . . . . 4-3 Disconnect Mode . . . . . . . . . . . . . . . . . . . . . . . . . . . . . . . . . . . . . . . . . . . . . . . . 4-5 AT General Command Mode . . . . . . . . . . . . . . . . . . . . . . . . . . . . . . . . . . . . . . . . . 4-5 Answer Mode . . . . . . . . . . . . . . . . . . . . . . . . . . . . . . . . . . . . . . . . . . . . . . . . . . . 4-6 Initialization String Commands . . . . . . . . . . . . . . . . . . . . . . . . . . . . . . . . . . . . . . . 4-7 Preparation before Using Modem . . . . . . . . . . . . . . . . . . . . . . . . . . . . . . . . . . . . . 4-8 Setting Communication Parameters . . . . . . . . . . . . . . . . . . . . . . . . . . . . . . . . . . . 4-8 Programming Data Registers and Internal Relays . . . . . . . . . . . . . . . . . . . . . . . . . . 4-8 Operating Procedure . . . . . . . . . . . . . . . . . . . . . . . . . . . . . . . . . . . . . . . . . . . . . . 4-9 Sample Program for Modem Originate Mode . . . . . . . . . . . . . . . . . . . . . . . . . . . . . 4-9 Checking Modem Operation . . . . . . . . . . . . . . . . . . . . . . . . . . . . . . . . . . . . . . . . 4-10 HAPTER 5: USER COMMUNICATION INSTRUCTIONS C B1 TXD (Transmit) . . . . . . . . . . . . . . . . . . . . . . . . . . . . . . . . . . . . . . . . . . . . . . 5-1 B2 RXD (Receive) . . . . . . . . . . . . . . . . . . . . . . . . . . . . . . . . . . . . . . . . . . . . . . 5-8 HAPTER 6: COMPARISON INSTRUCTION C B3 CMP2 (Double-word Comparison) . . . . . . . . . . . . . . . . . . . . . . . . . . . . . . . . . 6-1 HAPTER 7: COMPUTER LINK C Computer Link 1:N Communication . . . . . . . . . . . . . . . . . . . . . . . . . . . . . . . . . . . . 7-1 Computer Link 1:N Communication Using Modems . . . . . . . . . . . . . . . . . . . . . . . . 7-2 RS232C/RS485 Converter FC2A-MD1 . . . . . . . . . . . . . . . . . . . . . . . . . . . . . . . . . 7-3 RS232C Cable HD9Z-C52 . . . . . . . . . . . . . . . . . . . . . . . . . . . . . . . . . . . . . . . . . . 7-4 AC Adapter . . . . . . . . . . . . . . . . . . . . . . . . . . . . . . . . . . . . . . . . . . . . . . . . . . . . . 7-4 USER’S MANUAL i TABLE OF CONTENTS HAPTER 8: SAMPLE PROGRAM – USER COMMUNICATION TXD C System Setup . . . . . . . . . . . . . . . . . . . . . . . . . . . . . . . . . . . . . . . . . . . . . . . . . . . 8-1 Description of Operation . . . . . . . . . . . . . . . . . . . . . . . . . . . . . . . . . . . . . . . . . . . . 8-1 Programming Expansion Control Data Registers . . . . . . . . . . . . . . . . . . . . . . . . . . . 8-1 Setting Communication Parameters . . . . . . . . . . . . . . . . . . . . . . . . . . . . . . . . . . . 8-2 Ladder Diagram . . . . . . . . . . . . . . . . . . . . . . . . . . . . . . . . . . . . . . . . . . . . . . . . . . 8-2 HAPTER 9: SAMPLE PROGRAM – USER COMMUNICATION TXD & RXD C System Setup . . . . . . . . . . . . . . . . . . . . . . . . . . . . . . . . . . . . . . . . . . . . . . . . . . . 9-1 Description of Operation . . . . . . . . . . . . . . . . . . . . . . . . . . . . . . . . . . . . . . . . . . . . 9-1 Setting Communication Parameters . . . . . . . . . . . . . . . . . . . . . . . . . . . . . . . . . . . 9-2 BASIC Program Display Example . . . . . . . . . . . . . . . . . . . . . . . . . . . . . . . . . . . . . . 9-2 BASIC Program . . . . . . . . . . . . . . . . . . . . . . . . . . . . . . . . . . . . . . . . . . . . . . . . . . 9-3 Ladder Diagram . . . . . . . . . . . . . . . . . . . . . . . . . . . . . . . . . . . . . . . . . . . . . . . . . . 9-4 HAPTER 10: SAMPLE PROGRAM – MODEM COMMUNICATION C System Setup . . . . . . . . . . . . . . . . . . . . . . . . . . . . . . . . . . . . . . . . . . . . . . . . . . 10-1 Allocation Numbers (Remote Station) . . . . . . . . . . . . . . . . . . . . . . . . . . . . . . . . . 10-2 Allocation Numbers (Local Station) . . . . . . . . . . . . . . . . . . . . . . . . . . . . . . . . . . . 10-3 Description of Operation . . . . . . . . . . . . . . . . . . . . . . . . . . . . . . . . . . . . . . . . . . . 10-3 Ladder Diagram (Remote Station) . . . . . . . . . . . . . . . . . . . . . . . . . . . . . . . . . . . . 10-4 Ladder Diagram (Local Station) . . . . . . . . . . . . . . . . . . . . . . . . . . . . . . . . . . . . . . 10-6 HAPTER 11: TROUBLESHOOTING C Error Causes and Actions . . . . . . . . . . . . . . . . . . . . . . . . . . . . . . . . . . . . . . . . . . 11-1 User Communication Error . . . . . . . . . . . . . . . . . . . . . . . . . . . . . . . . . . . . . . . . . 11-2 Troubleshooting Diagrams . . . . . . . . . . . . . . . . . . . . . . . . . . . . . . . . . . . . . . . . . 11-3 PPENDIX A Type List . . . . . . . . . . . . . . . . . . . . . . . . . . . . . . . . . . . . . . . . . . . . . . . . . . . . . . . A-1 ASCII Character Code Table . . . . . . . . . . . . . . . . . . . . . . . . . . . . . . . . . . . . . . . . . A-2 NDEX I ii USER’S MANUAL 1: GENERAL INFORMATION Introduction 3 This chapter describes general information about additional functions and speciŢcations incorporated in the MICRO C. For 3 3 general information, functions, and speciŢcations inherited from the MICRO , see the MICRO User’s Manual. Features 3 MICRO C has upgraded functions for communications. The new functions are particularly useful for modem communica- tion, user communication, and monitoring data communication. User Communication Function 3 3 MICRO C has an RS232C loader port in place of the RS485 loader port on the MICRO . The more widely applicable RS232C loader port can be directly connected to any equipment with an RS232C communication port. New advanced instructions for transmitting and receiving data make it possible to set up a communication system using various communication formats. The user communication function can be used only in the standard processing mode, not in the high-speed processing mode. Increased Data Registers 3 Since data communication requires more data registers, MICRO C has 500 data registers (D0 through D499) expanded 3 from 100 data registers in the MICRO . All expanded data registers except D499 can be used to program instructions. 3 In the high-speed processing mode, available data registers are limited to 32 (D0 through D31) as with the MICRO . Double-word Comparison of Data Registers Double-word comparison instruction is added to compare data in data registers. Two consecutive data registers designated by a source operand are compared with two consecutive data registers designated by another source operand. When used with a repeat designation, one double-word comparison instruction can execute a maximum of 31 double-word compari- son operations. With a repeat designation, the results of all double-word comparisons can not only be available individu- ally but also be ANDed; so the comparison results can be easily determined even when comparing a large quantity of data. Parts Description Function Selector Switch Selects the station function in the expansion or data link system. Analog Potentiometer Sets the analog value for the analog timer, frequency, or pulse width of pulse outputs. 567 10 3 MICRO C has only one potentiometer while 16- and 24-I/O type 3 MICRO base units have two potentiometers. 0 7 1 6 2 5 3 4 Protocol Selector Switch 01 0 7 1 Selects the communication protocol for the loader port (loader proto- 6 2 5 3 4 col or user protocol) and the data link terminals (data link/expansion link or loader protocol). Loader Port For connecting the program loader or computer. The loader port can also be used as a user communication port when user protocol is selected with the protocol selector switch. DATA LINK Communication Enable Button AS B G Enables the communication mode selected with the protocol selector switch. When the protocol selector switch setting is changed while 3 the MICRO C is powered up, press this button to enable the new com- munication mode for the loader port and data link terminals. Data Link Terminals For connecting the data link line in the expansion link or data link system. The data link terminals can also be used for connecting the program loader or computer when loader protocol is selected with the The Ţgure above illustrates the 16-I/O 3 protocol selector switch. type MICRO C base unit. USER’S MANUAL 1-1 1: GENERAL INFORMATION Protocol Selector Switch The protocol selector switch is used to select communication modes for the RS232C loader port and the RS485 data link 3 terminals. When the MICRO C is powered up, the selected communication modes are enabled automatically. If the protocol 3 selector switch setting is changed after the MICRO C is powered up, the new setting does not take effect until the commu- nication enable button is depressed. Communication Protocols for Loader Port and Data Link Terminals Protocol Selector Switch Position Loader Port Protocol Data Link Terminal Protocol Remarks 0 Loader protocol Data link protocol 1 User protocol Data link protocol 2 Loader protocol Loader protocol 3 User protocol Loader protocol 4 Loader protocol Loader protocol For maintenance (Note 1) 5 through 7 Reserved Reserved (Note 2) 3 Loader protocol: The protocol used for communication between MICRO C and program loader or CUBIQ on computer. User protocol: The protocol used for user communication instructions (RS232C) Data link protocol: The protocol used for communication in the expansion link or data link (RS485). Note 1: When the protocol selector switch is set to 4, the communication parameters for the loader port are arbitrarily set to the default values of FUN8 (loader port communication mode setting); baud rate 9,600 bps, terminator code 0D, 7 data bits, even parity, 1 stop bit, and receive timeout 500 msec. Any change in FUN8 values does not take effect. The communi- cation parameters for the data link terminals using the loader protocol are Ţxed and the same as the FUN8 default values. 3 Note 2: When the protocol selector switch is set to 5 through 7, the ERR1 indicator on the MICRO C blinks and the 3 MICRO C does not start to run. Communication Enable Button 3 While the MICRO C is powered up, pressing the communication enable button for more than 4 seconds until the ERR1 3 indicator blinks once makes the MICRO C read the settings on the protocol selector switch and function selector switch. 3 Then the MICRO C updates the communication modes for the loader port and data link terminals. This button is useful when you want to change the communication mode without turning power off. 3 If the communication enable button is pressed while the MICRO C is in operation, the user program Warning execution is stopped and all outputs are forced off. Function Selector Switch When the protocol selector switch is set to 0 or 1, the data link terminals can be used for expansion link or data link com- 3 munication. Then the function selector switch selects the station function for each MICRO C in the expansion link or data 3 3 link system. The function of the function selector switch on the MICRO C is the same as that on the MICRO . When the pro- tocol selector switch is set to 2 through 4 to select loader protocol for the data link terminals, the function selector switch setting has no effect. 3 MICRO C Station Function by Function Selector Switch Position 3 Function Selector Switch Position MICRO C Station Function 0 Base or master station 1 Slave station 1 2 Slave station 2 3 Slave station 3 4 Slave station 4 5 Slave station 5 6 Slave station 6 7 Expansion station 1-2 USER’S MANUAL 1: GENERAL INFORMATION System Setup 3 This section describes various system conŢgurations using the MICRO C and required settings. Selecting Communication Mode Set the function selector switch and the protocol selector switch to select a desired communication mode for the loader port and data link terminals. After changing the settings of the function selector switch and protocol selector switch while 3 the MICRO C is powered up, press the communication enable button for more than 4 seconds until the ERR1 indicator 3 3 blinks once; then the new communication mode takes effect. When the MICRO C is powered up, the MICRO C checks the settings of the function selector switch and protocol selector switch and enables the selected communication mode auto- matically. You have to press the communication enable button only when you change the communication mode while the 3 MICRO C is powered up. 3 If the communication enable button is pressed while the MICRO C is in operation, the user program Warning execution is stopped and all outputs are forced off. Connecting Program Loader to the Loader Port 3 When connecting a program loader to the loader port on the MICRO C, set the protocol selector switch to 0, 2, or 4 to select 3 loader protocol for the loader port. Use the loader cable 3C to connect the program loader to the MICRO C loader port. 3 Special cables are needed to connect to the loader port on the MICRO C. Loader cables for the Caution 3 MICRO such as FC2A-KL1 (2m/6.56 ft. long) and FC2A-KL2 (5m/16.4 ft. long) cannot be used for 3 3 the MICRO C. Cables used for connecting to the loader port on the MICRO C cannot be used for the 3 MICRO . If a wrong cable is used, machine damage may result. Loader Cable 3C FC2A-KL3C (2m/6.56 ft. long) The loader cable 3C has an RS232C/RS485 converter in the middle. When connecting and disconnecting the loader cable, be sure to hold the connec- tor. Since the connector has a latch, the cable cannot be removed holding the cable. Make sure of correct direction of the cable as indicated on the direction labels attached near the connectors on the cable. Connecting the Cable Slide the cover to the right The program loader has a cover on the top to select the loader cable connection port or AC adapter jack. Slide the cover to the right to open the loader cable connection port. Connect the connector of the loader cable to the loader cable connec- tion port on the program loader and the other connector of the cable to 3 the loader port on the MICRO C as indicated on the direction labels. Loader Cable Connection Port USER’S MANUAL 1-3 1: GENERAL INFORMATION Connecting Program Loader to the Data Link Terminals 3 A program loader can also be connected to the data link terminals on the MICRO C when the protocol selector switch is set to 2, 3, or 4 to select loader protocol for the data link terminals. This capability is particularly useful to monitor the com- munication data transmitted through the loader port while user communication or modem communication is performed with the protocol selector switch set to 3. Loader Cable 4C FC2A-KL4C (2m/6.56 ft. long) The loader cable 4C has a power supply box in the middle. (RS485) (RS485) AC Adapter (Output: 5V DC) The loader cable 4C is not supplied with an AC adapter, which must be prepared by the user. Note: AC adapters for IDEC’s FA series PLCs cannot be used. Connecting the Cable Slide the cover to the right The program loader has a cover on the top to select the loader cable connection port or AC adapter jack. Slide the cover to the right to open the loader cable connection port. Connect the connector of the loader cable to the loader cable con- nection port on the program loader and the three spade terminals on 3 the other end of the cable to the data link terminals on the MICRO C Loader Cable Connection Port as indicated on the marker tubes. Connecting an AC Adapter Connect an AC adapter to the power supply box in the middle of the Polarity 9.5 ş2.1 loader cable 4C to supply power to the program loader. Applicable output plug of the AC adapter is shown on the right. + – Dimensions in mm. When a program loader or computer running CUBIQ is connected to the data link terminals and a Caution communication device is connected to the loader port at the same time to perform communications shown below, multi-stage comparison instruction HSC1 cannot be used. Data link terminals: Used for loader protocol communication Loader port: Used for loader protocol communication at 19,200 bps 1-4 USER’S MANUAL ş5.5 SG B A 1: GENERAL INFORMATION Computer Link through Loader Port 3 To set up a 1:1 computer link system, connect an IBM PC or compatible to the MICRO C using the computer link cable 4C (FC2A-KC4C). Set the protocol selector switch to 0, 2, or 4 to select loader protocol for the loader port. Computer Link Cable 4C To RS232C Port FC2A-KC4C 3m (9.84 ft.) long To Loader Port (RS232C) D-sub 9-pin Female Connector Cable Connector Pinouts Pin Description 1 DCD Data Carrier Detect 2 RXD Receive Data 3 TXD Transmit Data 4 DTR Data Terminal Ready 5 GND Signal Ground 6 DSR Data Set Ready 7 —— 8 CTS Clear to Send 9 —— Computer Link through Data Link Terminals 3 A 1:1 computer link system can also be set up through the data link terminals on the MICRO C using the computer link cable 6C (FC2A-KC6C). Set the protocol selector switch to 2, 3, or 4 to select loader protocol for the data link terminals. Computer Link Cable 6C FC2A-KC6C To RS232C Port 2m (6.56 ft.) long RS232C/RS485 Converter D-sub 9-pin ABSG Female Connector Cable Connector Pinouts Connect the three spade ter- (RS485) minals on the computer link Pin Description cable 6C to data link termi- 1 —— nals A, B, and SG as indi- 2 RXD Receive Data cated on the maker tubes. 3 TXD Transmit Data 4 —— 5 GND Signal Ground 6 —— 7 RTS Request to Send AC Adapter 8 CTS Clear to Send Output: 5V DC Connect an AC adapter to the RS232C/RS485 converter in the 9 —— middle of the computer link cable 6C. The computer link cable 6C is not supplied with an AC adapter, which must be prepared by the user. For applicable output plug of the AC adapter, see page 1-4. Note: AC adapters for IDEC’s FA series PLCs cannot be used. USER’S MANUAL 1-5 1: GENERAL INFORMATION Connecting Modem through Loader Port 3 To connect a modem to the loader port on the MICRO C, use the modem cable 1C (FC2A-KM1C). Set the protocol selector switch to 1 or 3 to select user protocol for the loader port. Modem Cable 1C To RS232C Port FC2A-KM1C Modem 3m (9.84 ft.) long To Loader Port (RS232C) D-sub 25-pin Male Connector Cable Connector Pinouts Pin Description 1 FG Frame Ground 2 TXD Transmit Data 3 RXD Receive Data 4 RTS Request to Send 5 —— 6 —— 7 SG Signal Ground 8 DCD Data Carrier Detect 20 DTR Data Terminal Ready Connecting RS232C Equipment through Loader Port 3 To connect equipment with an RS232C communication port to the loader port on the MICRO C, use the user communica- tion cable 1C (FC2A-KP1C). One end of the user communication cable 1C is not provided with a connector, and it can be terminated with a proper connector to plug in to communicate with the RS232C port. 3 When the protocol selector switch is set to 1 or 3, MICRO C can communicate with RS232C equipment through the loader 3 port using the user protocol. When the protocol selector switch is set to 0, 2, or 4, MICRO C can communicate through the loader port using the loader protocol. User Communication Cable 1C RS232C Equipment FC2A-KP1C 2.4m (7.87 ft.) long To RS232C Port To Loader Port Attach a proper connector to the (RS232C) open end referring to the cable connector pinouts shown below. Cable Connector Pinouts Signal Direction Pin Description AWG# Color 1 RTS Request to Send 28 Black Twisted 2 DTR Data Terminal Ready 28 Yellow 3 TXD Transmit Data 28 Blue 4 RXD Receive Data 28 Green 5 DSR Data Set Ready 28 Brown 6 SG Signal Ground 28 Gray 7 SG Signal Ground 26 Red Twisted 8 NC No Connection 26 White Cover — Shield — — 1-6 USER’S MANUAL 1: GENERAL INFORMATION Link Systems 3 MICRO C has three link functions; expansion link, data link, and computer link. When using a link function, the function selector switch and protocol selector switch have to be set and the FUN settings may be required. For details of these set- 3 tings, see Expansion Link Function and Data Link Function in the MICRO User’s Manual and Computer Link 1:N Com- munication on page 7-1 in this manual. The expansion link cannot be used in the data link system. Expansion Link System 3 3 The expansion link system consists of two MICRO C or MICRO base units connected through the data link terminals using the optional expansion cable FC2A-KE1 (250 mm/9.84" long) or a shielded twisted pair cable as shown below. The cable 3 3 for the expansion link system can be extended up to 200 meters (656 feet). Every MICRO C or MICRO base unit can be used as an expansion station. Base Station Expansion Station Function selector switch: 0 Function selector switch: 7 Protocol selector switch: 0 or 1 Protocol selector switch: 0 or 1 The RUN indicator on the expan- sion station remains off whether the base station is running or stopped. Data Link System The data link system consists of one master station connected to a maximum of six slave stations to communicate control 3 3 data for distributed control. Every MICRO C or MICRO base unit can be used as a master or slave station. When a slave sta- tion performs communication at 19,200 bps through the loader port, multi-stage comparison instruction HSC1 cannot be used at the slave station. Master Station Slave Station 1 Slave Station 2 Slave Station 6 Function selector switch: 0 Function selector switch: 1 Function selector switch: 2 Function selector switch: 6 Protocol selector switch: 0 or 1 Protocol selector switch: 0 or 1 Protocol selector switch: 0 or 1 Protocol selector switch: 0 or 1 Computer Link System 3 In the computer link system, a personal computer is connected to one or a maximum of 32 MICRO C base units to control 3 the operation of all MICRO C base units. The 1:1 computer link system requires the computer link cable 4C (FC2A-KC4C) 3 or computer link cable 6C (FC2A-KC6C). The 1:N computer link system using MICRO C base units requires RS232C/ RS485 converter FC2A-MD1 and cables; computer link interface unit FC2A-LC1 is not required. 1st Unit 2nd Unit Nth Unit (N ≤ 32) Function selector switch: 0 Function selector switch: 0 Function selector switch: 0 Protocol selector switch: 2, 3, or4 Protocol selector switch: 2, 3, or 4 Protocol selector switch: 2, 3, or 4 FUN9: 0 FUN9: 1 FUN9: N–1 RS232C/RS485 Converter FC2A-MD1 3 The figure above illustrates a 1:N computer link system for MICRO C. USER’S MANUAL 1-7 1: GENERAL INFORMATION Communication SpeciŢcations 3 This section describes the MICRO C communication speciŢcations. For general speciŢcations, function speciŢcations, I/O 3 speciŢcations, and program loader speciŢcations, see the MICRO User’s Manual. Loader Port Communication SpeciŢcations Standards EIA RS232C Maximum Cable Length 15m (49.2 ft.) Baud Rate 1200, 2400, 4800, 9600, 19200 bps Data Bits 7 or 8 bits Parity Odd, Even, None Communication Stop Bits 1 or 2 bits Parameters 10 to 2550 msec Receive Timeout (In the user communication, receive timeout is disabled when 2550 msec is selected.) Connection to Program Loader Using optional loader cable 3C (FC2A-KL3C) Connection to RS232C Equipment Using optional user communication cable 1C (FC2A-KP1C) or other cables User Communication Mode SpeciŢcations 3 When the protocol selector switch is set to 1 or 3 to select user protocol for the loader port, the MICRO C can communicate through the loader port with external equipment which has an RS232C port, such as a computer, modem, printer, or bar- code reader. Using transmit and receive instructions for user communication, user programs can be created to match the communica- tion protocol of the equipment to communicate with. Determine the possibility of communication referring to the user communication mode speciŢcations described below: Standards EIA RS232C Control Signal TXD, RXD, DTR, RTS, DSR Baud Rate 1200, 2400, 4800, 9600, 19200 bps Data Bits 7 or 8 bits Parity Odd, Even, None Stop Bits 1 or 2 bits 10 to 2550 msec (10-msec increments) or none Receive Timeout (Receive timeout is disabled when 2550 msec is selected.) Communication Method Start-stop synchronization system half-duplex Maximum Transmit Data 200 bytes Maximum Receive Data 200 bytes 1-8 USER’S MANUAL 1: GENERAL INFORMATION Data Link Terminal Communication SpeciŢcations Standards EIA RS485 (termination resistor is not required) Recommended Cable ş0.9 mm shielded twisted cable Conductor Resistance 85 Ω/km maximum Shield Resistance 12 Ω/km maximum Maximum Cable Length 200m (656 ft.) 3 Isolation Between data link terminals of multiple MICRO C units: Not isolated Expansion or data link communication: 19200 bps (Ţxed) Baud Rate Loader protocol communication: 9600 bps (Ţxed) Expansion link: Master station normal scan time + approx. 9 to 10 msec Communication Delay Data link: Master station normal scan time + approx. 12.5 to 13 msec + Slave station scan time Connection to Program Loader Using optional loader cable 4C (FC2A-KL4C) Data Link Terminal Communication with Program Loader 3 When the protocol selector switch is set to 2, 3, or 4 to select loader protocol for the data link terminals, the MICRO C can 3 communicate through the data link terminals with the program loader or computer to monitor the MICRO C operation, transfer user programs, and perform other communications. The communication parameters using the loader protocol for the data link terminals are Ţxed to the same values as the FUN8 (loader port communication mode setting) default shown below and cannot be selected unlike the communication through the loader port. Data Link Terminal Communication Parameters (Loader Protocol) Baud Rate 9600 bps Terminator Code 0D (CR) Data Bits 7 bits Parity Even Stop Bit 1 bit Receive Timeout 500 msec 3 When the protocol selector switch is set to 2 or 4, the MICRO C can perform loader communication through both the loader port and data link terminals at the same time. If data write operation (write N bytes or write 1 bit) is attempted to the same operand through both the loader port and data link terminals at the same time, the command through the data link termi- nals has priority although communication error does not occur at both ports. Some of the program transfer operation cannot be performed as described below: Caution 1. While a user program is written through either the loader port or data link terminals, a user program cannot be written through the other port. The prior write user program operation is executed normally, but the subsequent write user program operation results in a protect error. 2. While a user program is written through either the loader port or data link terminals, a user program cannot be read through the other port. The prior write user program operation is executed normally, but the subsequent read user program operation results in a protect error. 3. A user program cannot be read through either the loader port or data link terminals if a user program is written through the other port before the read user program operation is completed. The subsequent write user program operation is executed normally, but the prior read user program operation may fail to read the complete user program and result in a CRC error. USER’S MANUAL 1-9 1: GENERAL INFORMATION Dimensions 3 MICRO C Base Unit Program Loader 30 mm (1.181") 95 mm (3.740") 16-I/O Type: 135 mm (5.315") 60 mm (2.362") 24-I/O Type: 165 mm (6.496") 80 mm (3.150") 25 mm (0.984") Mounting Hole Layout Minimum M4 tapped holes or center to center ş4.5 (0.177" dia.) drilled holes 58 mm (2.283") 77 mm (3.031") 16-I/O Type: 116 mm (4.567") 24-I/O Type: 146 mm (5.748") Minimum center to center 29 mm (1.142") 1-10 USER’S MANUAL 85 mm (3.346") 185 mm (7.283") 2: ALLOCATION NUMBERS Introduction 3 This chapter describes allocation numbers available only for the MICRO C. For details about allocation numbers shared 3 3 with the MICRO , see the MICRO User’s Manual. 3 Expanded functions in the MICRO C include: 3 3 MICRO C has 500 data registers D0 through D499 while MICRO has 100 data registers D0 through D99. D499 is used to enable or disable expansion control data registers D484 through D498 and cannot be used as an ordinary data register to store data. Special internal relay M307 has different functions when used as a base or expansion station in the expansion link system or when used as a master station or slave station in the data link system. Allocation Numbers 3 Available I/O numbers depend on the type and combination of the MICRO C base units used in the expansion link system. For details of available I/O numbers in the expansion link system, see the next page. Operand Processing Mode Allocation Number Maximum Points Standard and 14 points (Base) I0 - I7 I10 - I15 High-speed Input + 14 points (Expansion) Standard only I20 - I27 I30 - I35 Standard and 10 points (Base) Q0 - Q7 Q10 - Q11 High-speed Output + 10 points (Expansion) Standard only Q20 - Q27 Q30 - Q31 Standard and M0 - M7 M10 - M17 M20 - M27 High-speed M30 - M37 M40 - M47 M50 - M57 M60 - M67 M70 - M77 M80 - M87 M90 - M97 M100 - M107 232 points M110 - M117 M120 - M127 M130 - M137 Internal Relay (40 points) M140 - M147 M150 - M157 M160 - M167 Standard only M170 - M177 M180 - M187 M190 - M197 M200 - M207 M210 - M217 M220 - M227 M230 - M237 M240 - M247 M250 - M257 M260 - M267 M270 - M277 M280 - M287 Standard and 8 points Catch Input Relay M290 - M297 High-speed (8 points) Special Internal Standard and 16 points M300 - M307 M310 - M317 Relay High-speed (16 points) Standard and T0 - T15 High-speed Timer Standard only T16 - T31 32 points total (16 points total) Standard and C0 - C15 High-speed Counter Standard only C16 - C31 Standard and R0 - R31 64 points High-speed Shift Register (32 points) Standard only R32 - R63 Standard and D0 - D31 500 points High-speed Data Register (32 points) Standard only D32 - D499 Notes: Input and output allocation numbers for the expansion station start with I20 and Q20. For the I/O allocation num- bers in the expansion link system, see the next page. The maximum points shown in ( ) are values for the high-speed processing mode. The same number cannot be used for a counter and a timer in a user program. Internal relays M260 through M287 have special functions in the modem mode. See page 4-2. Data register D499 is reserved to enable or disable expansion control data registers D484 through D498 and cannot be used as an ordinary data register to store data. For details, see page 2-4. USER’S MANUAL 2-1 2: ALLOCATION NUMBERS I/O Allocation Numbers for Expansion Link System Input and output allocation numbers do not continue from the base station to the expansion station. At the expansion sta- 3 tion, inputs start at I20 and outputs start at Q20. Inputs and outputs are allocated depending on the MICRO C base units used in the expansion link system as shown below: 3 3 I/O Points MICRO C Base Station MICRO C Expansion Station Total IN/OUT I/O Allocation Numbers I/O Allocation Numbers 16-I/O Type 16 9/7 ——— I0 - I7 Q0 - Q6 I10 24-I/O Type 24 14/10 ——— I0 - I7 Q0 - Q7 I10 - I15 Q10 - Q11 16-I/O Type 16-I/O Type 32 18/14 I0 - I7 I20 - I27 Q0 - Q6 Q20 - Q26 I10 I30 16-I/O Type 24-I/O Type I0 - I7 I20 - I27 Q20 - Q27 Q0 - Q6 I10 I30 - I35 Q30 - Q31 40 23/17 24-I/O Type 16-I/O Type I0 - I7 Q0 - Q7 I20 - I27 Q20 - Q26 I10 - I15 Q10 - Q11 I30 24-I/O Type 24-I/O Type 48 28/20 I0 - I7 Q0 - Q7 I20 - I27 Q20 - Q27 I10 - I15 Q10 - Q11 I30 - I35 Q30 - Q31 2-2 USER’S MANUAL 2: ALLOCATION NUMBERS Special Internal Relays Internal relays M290 through M317 are special internal relays with the following functions: Allocation Number Description CPU Stopped Power OFF M290 Input I0 Operating Cleared M291 Input I1 Operating Cleared M292 Input I2 Operating Cleared M293 Input I3 Operating Cleared Catch Input Status Set (See Note below) M294 Input I4 Operating Cleared M295 Input I5 Operating Cleared M296 Input I6 Operating Cleared M297 Input I7 Operating Cleared M300 Start Control Maintained Maintained M301 Initialize Pulse (See Note below) Cleared Cleared M302 All Outputs OFF Cleared Cleared M303 Carry (Cy) or Borrow (Bw) Cleared Cleared M304 User Program Execution Error Cleared Cleared Link Communication Error M305 Maintained Cleared (Expansion mode and data link mode) Link Communication Prohibit Flag M306 Maintained Maintained (Expansion mode and data link mode) Link Communication Initialize Flag (Master Station) (Expansion mode and data link mode) M307 Cleared Cleared Link Communication Stop Flag (Slave Station) (Data link mode) M310 1-sec Clock Reset Cleared Cleared M311 1-sec Clock Operating Cleared M312 100-msec Clock Operating Cleared M313 10-msec Clock Operating Cleared M314 Timer/Counter Preset Value Changed Maintained Maintained M315 High-speed Counter Soft Reset Maintained Cleared M316 High-speed Counter (HSC3) Overţow Cleared Cleared M317 In-operation Output Cleared Cleared Note: M290 through M297 and M301 are used only for reading in the user program, but can be directly set or reset using the program loader or optional software CUBIQ on a computer. M307 Link Communication Initialize Flag (Master Station)/Link Communication Stop Flag (Slave Station) Special internal relay M307 has different functions when used as a base or expansion station in the expansion link system or when used as a master station or slave station in the data link system. Base or master station: Link communication initialize ţag When M307 at the base or master station is turned on during operation, the link conŢguration is checked to initialize the expansion or data link system. When an expansion station or slave station is powered up after the base or master station, turn M307 on to initialize the link system. After an expansion link or data link setup is changed, M307 must also be turned on to ensure correct communication. Slave station: Link communication stop ţag When a slave station does not receive communication data from the master station for 800 msec or more in the data link system, M307 turns on. When the slave station receives correct communication data, M307 turns off. In the expansion station, M307 has no effect and cannot be monitored using the program loader. USER’S MANUAL 2-3 2: ALLOCATION NUMBERS Data Register Allocation Numbers Available data registers are limited in the high-speed processing mode or in the data link system conŢguration. Some data registers are allocated to special functions in the data link system as shown below. For the data link function, see the 3 MICRO User’s Manual. D100 through D209, D492, and D493 have special functions in the modem mode. See page 4-2. Standard Processing Mode Data Register High-speed Data Link Data Link Number Processing Mode Other than Data Link (Master Station) (Slave Station) D0 to D31 Available Available D32 to D59 Available Available D60 to D84 For data link D85 to D89 For data link D90 to D99 Can be designated as control data registers using FUN10. (Note) D100 to D483 Available Not available D484 to D485 When expansion control data register service is enabled for each group of these data registers using D499, the selected data registers work as expansion con- D486 to D491 trol data registers; others can be used as ordinary data registers. D492 to D495 When expansion control data register service is disabled using D499, these D496 to D498 data registers can be used as ordinary data registers. D499 Reserved to enable or disable expansion control data register service. Note: When FUN10 is set to enable control data registers, selected data registers D90 through D99 work as control data 3 registers; others can be used as ordinary data registers. For details of the data link function, see the MICRO User’s Manual. Expansion Control Data Registers Data registers D484 through D499 are allocated as expansion control data registers. D499 is used to enable or disable expansion control data register service for D484 through D498 divided into group 0 through 3. Data registers in the group disabled for expansion control data registers can be used as ordinary data registers. D499 cannot be used as an ordinary data register and must not be programmed to store data of operation results. Group Expansion Control DR Description — D499 Expansion control data register service selection D498 Day (Calendar) 0 D497 Month (Calendar) D496 Year (Calendar) D495 Modem mode selection D494 Reserved 1 D493 Modem mode status D492 Protocol selection in modem mode D491 Control signal status D490 DSR control signal option D489 DTR control signal option Available only for communication through 2 the loader port using user protocol D488 RTS control signal option (protocol selector switch set to 1 or 3) D487 Reserved D486 RTS control signal ON/OFF timer D485 (Lower byte) Protocol selector switch value D485 (Upper byte) For maintenance 3 D484 (Lower byte) Function selector switch value D484 (Upper byte) For maintenance 2-4 USER’S MANUAL 2: ALLOCATION NUMBERS D499 Expansion Control Data Register Service Selection D499 is used to enable or disable expansion control data register service for D484 through D498 divided into group 0 through 3. D499 cannot be used as an ordinary data register and must not be programmed to store data of oper- Warning ation results. If an unexpected value is set to D499, the modem mode may be enabled or disabled during operation. Store a value in D499 to enable or disable expansion control data service for group 0 through 3 as described below: D499 Value Group 0123456789 10 11 12 13 14 15 0 (D496-D498) 1 (D492-D495) 2 (D486-D491) 3 (D484-D485) The D499 value marked with indicates that the data registers in the corresponding group are enabled for expansion con- trol data register service. The enable/disable of expansion control data register service is determined by the lower 4 bits in D499. Although a value over 15 can be entered to D499, upper 12 bits do not take effect. Group 0 D498 Day (Calendar) D497 Month (Calendar) D496 Year (Calendar) When group 0 is enabled as expansion control data registers, the calendar data are stored to D496 through D498. The year is indicated with the lower 2 digits. Group 1 D495 Modem mode selection When group 1 is enabled as expansion control data registers and “1” is set to D495, the modem mode is enabled. When “0” is set to D495, the modem mode is disabled. For the modem mode, see page 4-1. D494 Reserved D493 Modem mode status When the modem mode is enabled (see above), D493 stores a modem mode status. D493 Value Description Remarks 30h AT command completed normally AT command (start IR) is completed normally. 31h Issuing AT command See the result code stored in data registers D104 through D119. 32h AT command execution error Check the modem power, modem cable, and the remote modem. 33h Two or more start IRs are on Correct the program so that only one start IR goes on at a time. 34h Modem mode enabled Correct the program so that only the disconnect command is issued 35h Start IR program error while the line is connected. 36h (Reserved) 37h (Reserved) 38h Retrying AT command 39h AT command program error Correct the program to include 0Dh in the AT command. D492 Protocol selection in modem mode When the modem mode is enabled (see above), the protocol at the loader port is switched from the user protocol depend- ing on the value in D492 after the telephone line is connected. D492 = 1: User protocol is continued at the loader port D492 = 0: Loader protocol is enabled at the loader port USER’S MANUAL 2-5 2: ALLOCATION NUMBERS Group 2 D491 Control signal status When group 2 is enabled as expansion control data registers, D491 stores a value to show that RTS, DSR, and DTR are on or off. The data of D491 is updated at every END processing. D491 Value RTS DSR DTR Description 0 OFF OFF OFF All RTS, DSR, and DTR are off. 1 ON OFF OFF RTS is on. 2 OFF ON OFF DSR is on. 3 ON ON OFF RTS and DSR are on. 4 OFF OFF ON DTR is on. 5 ON OFF ON RTS and DTR are on. 6 OFF ON ON DSR and DTR are on. 7 ON ON ON All RTS, DSR, and DTR are on. D490 DSR control signal option 3 When group 2 is enabled as expansion control data registers, D490 is used to control data ţow between the MICRO C and the remote terminal depending on the DSR (Data Set Ready) signal of the remote terminal. The DSR signal is an input to 3 3 the MICRO C to determine the status of the remote terminal. The remote terminal informs the MICRO C using DSR whether the remote terminal is ready for receiving data or is sending valid data. The DSR control signal option can be used only in the user protocol to communicate through the loader port. D490 = 0 (system default): DSR is not used for data ţow control. When DSR control is not needed, set 0 to D490. 3 D490 = 1: When DSR is on, MICRO C can transmit and receive data. ON DSR signal OFF Transmit/receive Impossible Possible Impossible Transmit/receive data Data 3 D490 = 2: When DSR is off, MICRO C can transmit and receive data. ON DSR signal OFF Transmit/receive Impossible Possible Impossible Transmit/receive data Data 3 D490 = 3: When DSR is on, MICRO C can transmit data. This function is usually called “Busy Control” and is used for controlling transmission to a remote terminal with a slow processing speed, such as a printer. When the remote terminal is busy, data input to the remote terminal is restricted. ON DSR signal OFF Transmit Impossible Possible Impossible Transmit data Data 2-6 USER’S MANUAL 2: ALLOCATION NUMBERS 3 D490 = 4: When DSR is off, MICRO C can transmit data. This function is contrary to “D490 = 3.” ON DSR signal OFF Transmit Impossible Possible Impossible Transmit data Data 3 D490 = 5: When DSR is on, MICRO C can receive data. ON DSR signal OFF Receive data Data 3 MICRO C receives data arriving while DSR is on. Data out of this range are not received. 3 D490 = 6: When DSR is off, MICRO C can receive data. This function is contrary to “D490 = 5.” ON DSR signal OFF Receive data Data 3 MICRO C receives data arriving while DSR is off. Data out of this range are not received. D490 = 7 or more: Same as D490 = 0. DSR is not used for data ţow control. D489 DTR control signal option When group 2 is enabled as expansion control data registers, D489 is used to control the DTR (Data Terminal Ready) sig- 3 nal to indicate the MICRO C operating status or transmitting/receiving status. The DTR control signal option can be used only in the user protocol to communicate through the loader port. D489 = 0 (system default): 3 3 3 While MICRO C is running, DTR is on whether MICRO is transmitting or receiving data. While MICRO C is 3 stopped, DTR remains off. Use this option to indicate the MICRO C operating status. 3 Stopped Running Stopped MICRO C ON DTR signal OFF 3 3 D489 = 1: While MICRO C is transmitting data, DTR is turned on. While MICRO C is not transmitting data, DTR remains off. Use this option when a remote terminal operates in the half-duplex mode since DTR goes on or off 3 according to the transmit data from MICRO C. Transmit data Transmit data ON DTR signal OFF USER’S MANUAL 2-7 2: ALLOCATION NUMBERS 3 3 D489 = 2: While MICRO C is transmitting data, DTR remains off. While MICRO C is not transmitting data, DTR is turned on. The DTR operation at this option is contrary to the operation at D489 = 1. Transmit data Transmit data ON DTR signal OFF D489 = 3: DTR remains off. 3 D489 = 4: While MICRO C can receive data, DTR is turned on. Use this option when ţow control of receive data is required. D489 = 5: DTR is turned on or off according to DSR. When DSR is on, DTR is turned on. When DSR is off, DTR remains off. Use this option for returning control signal and acknowledgment when data ţow control with the remote terminal is required. ON DSR signal OFF ON DTR signal OFF D489 = 6 or more: Same as D489 = 0. D488 RTS control signal option When group 2 is enabled as expansion control data registers, D488 is used to control the RTS (Request to Send) signal to 3 indicate the MICRO C transmitting/receiving status or operating status. The RTS control signal option can be used only in the user protocol to communicate through the loader port. D488 = 0 (system default): 3 3 While MICRO C is transmitting data, RTS remains off. While MICRO C is not transmitting data, RTS is turned on. Use this option when a remote terminal operates in the half-duplex mode since RTS goes on or off accord- 3 ing to the transmit data from MICRO C. Transmit data Transmit data ON RTS signal OFF 3 3 D488 = 1: While MICRO C is transmitting data, RTS is turned on. While MICRO C is not transmitting data, RTS remains off. Use this option when a remote terminal operates in the half-duplex mode since RTS goes on or off accord- 3 ing to the transmit data from MICRO C. Transmit data Transmit data ON RTS signal OFF 3 3 3 D488 = 2: While MICRO C is running, RTS is on whether MICRO C is transmitting or receiving data. While MICRO C is 3 stopped, RTS remains off. Use this option to indicate the MICRO C operating status. 3 Stopped Running Stopped MICRO C ON RTS signal OFF D488 = 3: RTS remains off. 2-8 USER’S MANUAL 2: ALLOCATION NUMBERS 3 D488 = 4: While MICRO C can receive data, RTS is turned on. Use this option when ţow control of receive data is required. D488 = 5: RTS is turned on or off according to DSR. When DSR is on, RTS is turned on. When DSR is off, RTS remains off. Use this option for returning control signal and acknowledgment when data ţow control with the remote terminal is required. ON DSR signal OFF ON RTS signal OFF D488 = 6 or more: Same as D488 = 0. D487 Reserved D486 RTS control signal ON/OFF timer When group 2 is enabled as expansion control data registers and D488 is set to 0 or 1 to synchronize the transmit data with the RTS signal, D486 is used to set the amount of time to turn on and off the RTS signal before and after transmitting data. The RTS control signal ON/OFF timer can be used only in the user protocol to communicate through the loader port. D486 = 0 through 249 (Increments 10 msec): Any value over 249 is regarded as 249. The maximum timer error is 20 msec + 2 scan time. Example: D488 = 0 (RTS control signal option) and D486 = 5 ON RTS signal OFF Transmit data Transmit data 50 msec 50 msec 3 MICRO C transmits data 50 msec after RTS is turned off and RTS is turned on 50 msec after data transmission is completed. 3 Since a sufŢcient amount of time is allowed for the remote terminal after MICRO C has issued RTS, this option is useful when the remote terminal has a slow communication (receiving) speed. •Operating Status and Control Signals 3 3 Communication Mode MICRO C Stopped MICRO C Running DTR and RTS are on, except Control signal statuses depend on D488 User Protocol DTR is off when D489 = 0 through D490 options. RTS is off when D488 = 2 Initial settings are: Modem Mode DTR and RTS are on as standard. D488 = 2, D489 = 0, D490 = 0 Control signal options have no effect. Loader Protocol Communication is executed with D488 = 0, D489 = 0, D490 = 0. When DSR control is used with D490 set to 1 through 4, transmit condition must be satisŢed within 5 seconds after the DSR signal has turned to allow transmission. If transmit condition is not met within 5 seconds, the transmit data is invali- dated. Then, RTS and DTR take the same statuses as if the data were transmitted. When group 2 is disabled and user communication is used without control signal options, the communication is performed under the same conditions as expansion control data registers are set D488 = 0, D489 = 0, and D490 = 0. USER’S MANUAL 2-9 2: ALLOCATION NUMBERS Group 3 D485 Protocol selector switch value When group 3 is enabled as expansion control data registers, the lower byte of D485 stores the value set on the protocol selector switch. The upper byte of D485 is reserved for maintenance. To view the protocol selector switch value, monitor D485 in hexadecimal notation on the program loader. E 4 8 5 OUT MON OR MON MCS/R CC= D 16 D485 $**03 Protocol selector switch value For maintenance D484 Function selector switch value When group 3 is enabled as expansion control data registers, the lower byte of D484 stores the value set on the function selector switch. The upper byte of D484 is reserved for maintenance. To view the function selector switch value, monitor D484 in hexadecimal notation on the program loader. E 4 8 4 OUT MON OR MON MCS/R D 16 D484 $**01 Function selector switch value For maintenance 2-10 USER’S MANUAL SG B A 3: COMMUNICATION MONITOR Introduction This chapter describes FUN29 user communication status readout and FUN50 user communication data monitor. The FUN29 and FUN50 communication monitor functions can be used when the protocol selector switch is set to 3 to select user protocol for the loader port and loader protocol for the data link terminals. 3 While the MICRO C is communicating through the loader port using the user protocol, the communication status or com- munication data can be monitored on a program loader or computer connected to the data link terminals. The communica- tion monitor functions are useful for debugging user communication programs. System Setup 0 Protocol Selector Switch 7 1 6 2 Set to 3 to select user protocol for the loader port 5 3 RS232C Equipment 4 and loader protocol for the data link terminals (modem, printer, computer) To Loader Port To RS232C Port ABSG To Data Link Terminals Loader Cable 4C (RS485) Computer Link Cable 6C FC2A-KL4C 2m (6.56 ft.) long FC2A-KC6C 2m (6.56 ft.) long Power Supply Box AC Adapter Output: 5V DC For communication monitor functions using a computer, see the CUBIQ User’s Manual. FUN29: User Communication Status Readout User communication error data, execution of transmit/receive instructions, and communication parameters can be read using FUN29 on the program loader. Error code 2 9 FUN 29 COM-ERR 0 FUN 0: No error BRD JMP/E (TXD ) 1: Error occurred in received data (RXD ) (parity, framing, overrun error, etc.) 9600 EVEN 7 (1) Transmit instruction Baud rate : Not transmitting data 1200 bps : Transmitting data 2400 bps Parity Receive instruction 4800 bps Even 9600 bps Data bits Stop bits : Not receiving data Odd 19200 bps : Receiving data None 7 or 8 bits 1 or 2 bits To return to the editor mode, press the CLR key. USER’S MANUAL 3-1 3: COMMUNICATION MONITOR FUN50: User Communication Data Monitor 3 Transmit and receive data of user communication between the MICRO C and RS232C equipment can be monitored using FUN50 on the program loader connected to the data link terminals. Before using the FUN50 user communication data monitor, make sure of the correct system setup shown on the preceding page. If the protocol selector switch setting has been changed to 3 after power up, press the communication enable button 3 on the MICRO C until the ERR1 indicator blinks once; then the new communication setting is enabled. First bring the FUN50 screen up pressing the keys: 5 FUN 50 LINE-MON FUN 0 CC= *STOP Monitoring ON/OFF STOP: Monitoring is off :(DATA)--- 0 RUN: Monitoring is on Communication Data Blocks Indicates the quantity of transmit and receive data blocks communicated during monitoring. To start monitoring, move down the cursor to the asterisk on the second line and set the monitoring ON/OFF to RUN: B FUN 50 LINE-MON REP RUN RUN indicates monitoring is on. :(DATA)--- 2 3 Increments as MICRO C transmits and receives data during monitoring. To move the cursor up or down, press the or key. Pressing the REP key toggles RUN and STOP to start or stop monitoring. When monitoring is started by switching to RUN, monitor data stored in the previous monitoring is cleared from memory. Monitor data can be stored up to 30 screens. When the monitor buffer reaches full capacity, “FULL” is displayed in place of the communication data blocks, stopping communication data monitor. Before displaying the monitored data, Ţrst stop monitoring, then move the cursor down to the colon (:) and start to display the monitored data. B marks the start of a communication data block ** REP **05303132333435 Hex code 0 1 2 3 4 5 3637383941424344 ASCII character display 6 7 8 9 A B C D To view the next or preceding screen of monitor data, press the or key. A maximum of 30 screens can be displayed. A communication data block consists of transmit and/or receive data. When the interval between communication charac- ters exceeds 20 msec, the communication data block ends at this point and are displayed on a new line to mark the ** beginning of the next communication data block. To return to the FUN50 screen, press the CLR key. To return to the editor screen, press the CLR key again. 3 After the FUN50 user communication data monitor is completed, press the communication enable button on the MICRO C for 4 seconds until the ERR1 indicator blinks once; then normal communication using the program loader is enabled. If the communication enable button is pressed while a user transmit or receive instruction is executed, the execution is aborted and all outputs are forced off. 3-2 USER’S MANUAL 4: MODEM MODE Introduction 3 3 This chapter describes the modem mode designed for communication between the MICRO C and another MICRO C or any 3 data terminal equipment through telephone lines. Using the modem mode, the MICRO C can initialize a modem, dial a tele- phone number, send an AT command, enable the answer mode to wait for an incoming call, and disconnect the telephone line. All of these operations can be performed simply by turning on a start internal relay dedicated to each operation. 3 The modem mode provides for a simple modem control function so that the MICRO C can initialize Caution a modem, dial a destination telephone number, or answer an incoming call. The performance of the modem communication using the modem mode depends on the modem functions and telephone line situations. The modem mode does not prevent intrusion or malfunctions of other systems. For practical applications, conŢrm the communication function using the actual system setup and include safety provisions. System Setup 3 To connect a modem to the loader port on the MICRO C, use the modem cable 1C (FC2A-KM1C). To enable the modem mode, make the three settings described below: 1. Set the protocol selector switch to 1 or 3 to select user protocol for the loader port. (See page 1-2.) 2. Enter 6 (7, 14, or 15) to data register D499 to enable expansion control data register service for D486 through D495. (See page 2-5.) 3. Enter 1 to data register D495 to enable the modem mode. (See page 2-5.) 0 7 1 Protocol Selector Switch 6 2 5 3 Set to 1 or 3 to select user protocol 4 for the loader port To RS232C Port Modem Modem Cable 1C To Loader Port FC2A-KM1C (RS232C) D-sub 25-pin 3m (9.84 ft.) long Male Connector Mini DIN Connector Pinouts D-sub 25-pin Connector Pinouts Description Color Pin Pin Description Shield — Cover 1 FG Frame Ground RTS Request to Send Black 1 2 TXD Transmit Data DTR Data Terminal Ready Yellow 2 3 RXD Receive Data TXD Transmit Data Blue 3 4 RTS Request to Send RXD Receive Data Green 4 5 —— DSR Data Set Ready Brown 5 6 —— SG Signal Ground Gray 6 7 SG Signal Ground SG Signal Ground Red 7 8 DCD Data Carrier Detect NC No Connection White 8 20 DTR Data Terminal Ready 3 Do not connect the NC (No Connection) pin to any line; otherwise, the MICRO C may be damaged. Caution 3 Modem cables for Apple Macintosh computers cannot be used for the MICRO C. Applicable Modems Any Hayes compatible modem can be used. Modems with a communications rate of 9600 bps or more between modems are recommended. Use modems of the same make and model at both ends of the communication line. In making this user’s manual, the correct operation has been conŢrmed on four modems: AIWA’s PV-AF144V5, AIWA’s PV-BF144, AIWA’s PV-BF288M2, and OMRON’s ME1414BII. When using other modems, set a proper initialization string by referring to page 4-3 and conŢrm operation. USER’S MANUAL 4-1 4: MODEM MODE Internal Relays for Modem Mode When the modem mode is enabled, internal relays M260 through M287 are allocated to special functions. M260 through M266 are used to send an AT command or disconnect the telephone line. M270 through M276 and M280 through M286 turn on to indicate the results of the command. M267, M277, and M287 are used to indicate the status of the loader port. All of internal relays M260 through M287 are turned off at the Ţrst scan in the modem mode. Start and Result Internal Relays Mode Command Start IR Completion IR Failure IR Data Registers Initialization String M260 M270 M280 D135-D159 Originate Mode ATZ (M261) M271 M281 — Dialing (M262) M272 M282 D160-D209 Disconnect Mode Disconnect Line M263 M273 M283 — AT General Command Mode AT Command M264 M274 M284 D120-D134 Initialization String M265 M275 M285 D135-D159 Answer Mode ATZ (M266) M276 M286 — When one of start internal relays M260 through M266 is turned on, a corresponding command is executed once. To repeat the command, reset the start internal relay and turn the internal relay on again. Completion or failure of a command is determined as described below: Completion: The command is transmitted repeatedly as many as the retry cycles speciŢed in data register D100. When the command is completed successfully, the completion IR is turned on and the command is not executed for the remaining cycles. Failure: The command is transmitted repeatedly but failed in all trials as many as the retry cycles speciŢed in data register D100. Loader Port Status Internal Relays Status IR Status Description ON: Loader port protocol is in transition between loader protocol and user protocol M267 Protocol Transition OFF: Loader port protocol is settled to loader protocol or user protocol (Note) ON: Command mode M277 Operational State OFF: On-line mode ON: Telephone line connected M287 Line Connection OFF: Telephone line disconnected 3 Note: While M267 (protocol transition) is on, the MICRO C cannot send and receive communication. Data Registers for Modem Mode When the modem mode is enabled, data registers D100 through D209, D492, and D493 are allocated to special functions. At the Ţrst scan in the modem mode, D100 and D135 through D159 store the default values. DR Stored Data Description 0: No retry Retry Cycles D100 1-99: Executes a speciŢed number of retries (Default = 3) 100 or more executes 99 retries Modify Initialization String 0: \Q3 (used for AIWA’s modems) D101 (Change \Q3 in the default) 1 or more: \Q2 (used for OMRON’s modems and others) D102-D103 Reserved — D104-D119 AT Command Result Code AT command result codes returned from modem are stored D120-D134 AT Command String AT command string for the AT general command mode is stored D135-D159 Initialization String Initialization string for the originate and answer modes is stored D160-D209 Telephone Number Telephone number for dialing in the originate mode is stored Protocol for the loader port after telephone line is connected is selected D492 On-line Mode Protocol 0: Loader protocol 1: User protocol D493 Modem Mode Status Modem mode status is stored (see page 4-6) 4-2 USER’S MANUAL 4: MODEM MODE Originate Mode The originate mode is used to send an initialization string to the modem, issue the ATZ command to reset the modem, and dial the telephone number. To execute a command, turn on one of start internal relays M260 through M262. If two or more start internal relays are turned on simultaneously, an error will result and error code 33h is stored in modem mode status data register D493 (see page 4-6). When a start internal relay is turned on, a corresponding sequence of commands is exe- cuted once as described below. M260: Send initialization string, send the ATZ command, and dial the telephone number M261: Send the ATZ command and dial the telephone number M262: Dial the telephone number Initialization String 3 When the modem mode is enabled as described on page 4-1 and the MICRO C is started to run, the default initialization string is stored to data registers D135 through D154 at the END processing of the Ţrst scan. To send the initialization 3 string from the MICRO C to the modem, turn M260 on; then the ATZ command is issued and the telephone number is dialed successively. Default Initialization String: ATE0Q0V1X4\Q3&D2&C1\J0\V0\A0&M5\N2S0=2&W CR LF When D101 (modify initialization string) is set to 0, the default initialization string shown above is stored to data registers D135 through D154. AT and LF are appended at the beginning and end of the initialization string automatically by the sys- tem program and are not stored in data registers. DR 135 136 137 138 139 140 141 142 143 144 145 146 147 148 149 150 151 152 153 154 AT E0 Q0 V1 X4 \Q 3& D2 &C 1\ J0 \V 0\ A0 &M 5\ N2 S0 =2 &W 0D00 LF This initialization string is used for AIWA’s modems. Depending on your modem and telephone line, the initialization string may have to be modiŢed. To replace \Q3 with \Q2 to be used for OMRON’s modems and others, set 1 to data regis- ter D101 (modify initialization string). More changes can also be made by entering required values to data registers D135 through D159. Store two characters in one data register; the Ţrst character at the upper byte and the second character at the lower byte in the data register. AT and LF need not be stored in data registers. Use the MOV (move) instructions to set ASCII values of the initialization string characters and CR at the end. Program the MOV instructions to replace the default values in D135 through D154 stored in the Ţrst scan and execute the MOV in a subsequent scan. For essential commands which must be included in the initializa- tion string, see page 4-7. After the new values are stored, turn M260 on to send the new initialization string to the modem. When the initialization string has been sent successfully, internal relay M270 is turned on. If the initialization string fails, internal relay M280 is turned on. When the subsequent commands of ATZ and dialing are also completed successfully, M271 and M272 will also be turned on. The default initialization string or the modiŢed initialization string stored in D135 through D159 is also used for the ini- tialization in the answer mode. ATZ (Resetting the Modem) The default initialization string speciŢes to be stored in the non-volatile memory of the modem, using the &W command. 3 The initialization string is restored when the modem is powered up or when the ATZ command is issued. MICRO C sends the ATZ command to the modem, following the initialization string when M260 is turned on. The ATZ command can also be issued separately by turning M261 on, followed by the dial command to be executed automatically. ATZ Command: ATZ CR LF When the ATZ command has been completed successfully, internal relay M271 is turned on. If the ATZ command fails, internal relay M281 is turned on. When the subsequent dialing is also completed successfully, M272 will also be turned on. If the initialization string has been stored in the non-volatile memory of the modem, M260 may be skipped. Start with M261 to send the ATZ command. USER’S MANUAL 4-3 4: MODEM MODE Dialing the Telephone Number When the modem mode is enabled, data registers D160 through D209 are allocated to the telephone number. Before turn- ing on one of the start internal relays M260 through M262 for the originate mode, store the telephone number in data reg- isters starting with D160. One data register stores two characters: the Ţrst character at the upper byte and the second character at the lower byte in the data register. Since 50 data registers are allocated to the telephone number, up to 100 characters can be stored, as many as the modem capacity allows. Use the MOV (move) instructions to set ASCII values of the telephone number and execute the MOV instructions before turning on start internal relays M260 through M262. Example of Dial Command: ATDT123 CR LF ATD and LF are appended at the beginning and end of the dial command automatically by the system program and need not be stored in data registers. To program the telephone number of the example above, store ASCII values of T for touch- tone phone or P for pulse or rotary phone, followed by the telephone number and CR to data registers starting with D160. 5431h D160 54h = “T” 31h = “1” 32h = “2” 33h = “3” D161 3233h 0Dh = CR All characters subsequent to CR are ignored. D162 0D00h As described above, when start internal relay M260 is turned on, the initialization string is sent, followed by the ATZ com- mand and the dial command. When start internal relay M261 is turned on, the ATZ command is sent, followed by the dial command. The dial command can also be sent separately by turning on start internal relay M262. If retry cycles are set to data register D100, the dial command is repeated at intervals of approximately 1 minute as many as the speciŢed retry cycles until the telephone line is connected. When the dial command has been completed successfully, internal relay M272 is turned on. If the dial command fails, internal relay M282 is turned on. The dial command is determined successful when the DCD signal is turned on and when result code CR LF CONNECT CR LF or CR LF CARRIER OK CR LF returned from the modem is received. 3 Note: When the MICRO C is powered down while the telephone line is connected, the telephone line is disconnected because the DTR signal is turned off. This method should not be used for disconnecting the telephone line. Always use M263 to disconnect the telephone line as described on page 4-5. Loader Port Communication Protocol Before the telephone line is connected in the modem mode after power up, the loader port can only send out an AT com- mand by turning on a start internal relay M260 through M266. The communication protocol for the loader port after the telephone line is connected is selected by the value stored in data register D492. D492 Loader Port Communication Protocol in the On-Line Mode 0 Loader protocol 1 User protocol When the telephone line is disconnected, the loader port restores the state as before the telephone line is connected, whether D492 is set to 0 or 1. When using a TXD or RXD instruction in the user communication mode while the telephone line is connected, insert internal relay M287 (line connection) as an input condition for the TXD or RXD instruction. After the telephone line is connected, make sure of an approximately 5-second interval before executing the TXD or RXD instruction until the tele- phone line connection stabilizes. 3 Note: When the MICRO C is stopped while the telephone line is connected, the loader port protocol changes to the loader protocol even if D492 is set to 1 (user protocol in the on-line mode); then the telephone line remains connected. When the 3 3 MICRO C is started again, the MICRO C restores the on-line mode. 4-4 USER’S MANUAL 4: MODEM MODE Disconnect Mode The disconnect mode includes only one command to disconnect the telephone line. To disconnect the telephone line, turn internal relay M263 on. The telephone line is disconnected by turning the DTR signal off since the initialization string includes the &D2 command. While a modem command is executed, another command cannot be executed. If two or more start internal relays are turned on simultaneously, an error will result and error code 33h is stored in modem mode status data register D493 (see page 4-6). When the disconnect command has been completed successfully, internal relay M273 is turned on. If the disconnect com- mand fails, internal relay M283 is turned on. The disconnect command is determined successful when the DCD signal is turned off. After the telephone line is disconnected, the loader port restores the state as before the telephone line is connected whether D492 is set to 0 or 1 so that the loader port can be controlled by turning on a start internal relay M260 through M266. Note: The disconnect mode does not use the escape sequence +++ and the ATH command. AT General Command Mode When the modem mode is enabled, data registers D120 through D134 are allocated to the AT general command string. Before turning on start internal relay M264 for the AT general command mode, store an AT command string in data regis- ters starting with D120. One data register stores two characters: the Ţrst character at the upper byte and the second charac- ter at the lower byte in the data register. Use the MOV (move) instructions to set the ASCII values of the AT command string and execute the MOV instructions before turning M264 on. Example of AT Command: ATE0Q0V1 CR LF AT and LF are appended at the beginning and end of the AT general command string automatically by the system program and need not be stored in data registers. To program the AT command string of the example above, store ASCII values of the command characters and CR to data registers starting with D120. D120 4530h 45h = “E” 30h = “0” 51h = “Q” 30h = “0” D121 5130h 56h = “V” 31h = “1” D122 5631h D123 0D00h 0Dh = CR All characters subsequent to CR are ignored. When the AT general command has been completed successfully, internal relay M274 is turned on. If the AT general com- mand fails, internal relay M284 is turned on. The AT general command is determined successful when result code CR LF OK CR LF returned from the modem is received. USER’S MANUAL 4-5 4: MODEM MODE Answer Mode The answer mode is used to send an initialization string to the modem and to issue the ATZ command to reset the modem. To execute a command, turn on one of start internal relays M265 or M266. If two or more start internal relays are turned on simultaneously, an error will result and error code 33h is stored in modem mode status data register D493 (see below). When a start internal relay is turned on, a corresponding sequence of commands is executed once as described below. M265: Send initialization string and send the ATZ command M266: Send the ATZ command Initialization String 3 When the modem mode is enabled as described on page 4-1 and the MICRO C is started to run, the default initialization string is stored to data registers D135 through D154 at the END processing of the Ţrst scan. To send the initialization string from the data registers to the modem, turn M265 on; then the ATZ command is issued subsequently. CR LF Default Initialization String: ATE0Q0V1X4\Q3&D2&C1\J0\V0\A0&M5\N2S0=2&W As described in the Originate Mode, the initialization string can be modiŢed to match your modem. For details of modify- ing the initialization string, see page 4-3. When the initialization string has been sent successfully, internal relay M275 is turned on. If the initialization string fails, internal relay M285 is turned on. When the subsequent ATZ command is also completed successfully, M276 will also be turned on. ATZ (Resetting the Modem) The default initialization string speciŢes to be stored in the non-volatile memory of the modem, using the &W command. 3 The initialization string is restored when the modem is powered up or the ATZ command is issued. MICRO C sends the ATZ command to the modem following the initialization string when M265 is turned on. The ATZ command can also be issued separately by turning M266 on. CR LF ATZ Command: ATZ When the ATZ command has been completed successfully, internal relay M276 is turned on. If the ATZ command fails, internal relay M286 is turned on. If the initialization string has been stored in the non-volatile memory of the modem, M265 may be skipped. Start with M266 to send the ATZ command. Modem Mode Status Data Register When the modem mode is enabled, data register D493 stores a modem mode status. D493 Value Description Remarks 30h AT command completed normally AT command (start IR) is completed normally. 31h Issuing AT command See the result code stored in data registers D104 through D119. 32h AT command execution error Check the modem power, modem cable, and the remote modem. 33h Two or more start IRs are on Correct the program so that only one start IR goes on at a time. 34h Modem mode enabled Correct the program so that only the disconnect command is issued 35h Start IR program error while the line is connected. 36h (Reserved) 37h (Reserved) 38h Retrying AT command 39h AT command program error Correct the program to include 0Dh in the AT command. 4-6 USER’S MANUAL 4: MODEM MODE Initialization String Commands The default initialization string includes the commands shown below. The commands are described in three categories of importance. For details of modem commands, see the user’s manual for your modem. When modifying the initialization string, include the commands in the Ţrst category to make sure of correct modem communication. Commands which must be included in the initialization string Commands in this category are essential to use the modem mode. Some modems have the same function by a different command name. Modify the initialization string to match your modem. E0 Characters NOT echoed Q0 Result codes displayed &D2 Hang up and disable auto-answer on DTR detection 3 When the DTR signal turns off, the telephone line is disconnected. MICRO C uses this function to disconnect the telephone line. \J0 Set bps rate adjust off 3 The bps rate between the modem and the MICRO C or data terminal equipment is constant and independent of the telephone line bps rate. \Q3 When 0 is set to D101 for AIWA’s modems, \Q3 is enabled so that CTS and RTS are used for bidirectional hard- ware ţow control. When 1 is set to D101 for OMRON’s modems, \Q2 is substituted to set unidirectional hardware 3 ţow control. The XON/XOFF ţow control cannot be used for the MICRO C modem mode. V1 Word result code &C1 DCD ON with carrier from remote modem DCD tracks the state of the data carrier from the remote modem. An ON condition of DCD indicates the presence of a carrier. \V0 MNP result codes disabled Result codes returned to those controlled by the ATV1 command are set. Reliable link result codes are not used. &W Write active proŢle The current conŢguration proŢle is saved to a non-volatile memory. Command which requires a proper preset value S0 Ring to answer ON SpeciŢes the ring on which the modem will pick up the telephone line. S0=2 speciŢes that the modem answers an incoming call when detecting 2 ring calls. S0=0 disables the auto-answer function. Most modems have a default of S0=0. Commands which are optional X4 Enables dial tone and busy detection &M5 Enables error correction \N2 Sets the MNP operating mode to the reliable mode – buffered – error detection. V.42 can also be used. Error correction function is used to improve the communication reliability. \A0 Set MNP maximum block size to 64 bytes Modems are generally conŢgured so that the incoming data from DTE is compressed to a small amount as much as possible before the modem sends out the data to the telephone line; this is in consideration of higher data transmis- sion efŢciency and reduced cost. Consequently, modems require processing time after receiving data but before 3 sending out the data to the telephone line. In most applications of the MICRO C, it is desirable that the modem sends out data immediately after the modem has received the data. In addition, the amount of incoming and outgoing data for each communication is considered to be small; so the effect of data compression is small. Note: After setting the initialization string in the primary test phase of modem application, it is recommended that you use the AT\S (display on-line status) and AT%R (display conŢguration registers) commands on a computer to conŢrm the modem conŢguration and parameters. USER’S MANUAL 4-7 4: MODEM MODE Preparation before Using Modem Before using a modem, read the user’s manual for your modem. Determine commands for the initialization string To check if a particular AT command can be used for your modem, use the following method: 1. Store the ASCII values of the command to data registers starting with D120 and turn on internal relay M264 (start IR for AT general command) to send the AT command to the modem. 2. Send the AT command from the terminal mode of communication software on a computer to the modem. Determine the type of the telephone line Consult your local telephone company whether your telephone line is for touch tone phones or pulse dial phones. Deter- mine the dial command according to the type of the telephone line. ATDT Touch tone phones ATDP Pulse dial phones Test the modem operation After the initialization string has been sent to the modem, use the AT\S and AT%R commands on a computer to check the modem conŢguration and parameters. Setting Communication Parameters Set the FUN8 loader port communication parameters to match those of the modem and DTE connected on the communi- cation line. Since the total of modem communication parameters is 10 bits, set the FUN8 value to a total of 10 bits. Example (FUN8 Default): Data bits 7 Stop bit 1 Parity Even Start bit 1 Total 10 bits When the loader protocol is used for communication, the communication parameters shown above are recommended. Set 3 the baud rate of the MICRO C to a value between 2400 bps and 9600 bps using FUN8. When the program transfer function is used with the loader protocol, set the communications rate between modems to the 3 same value as the baud rate of the MICRO C or a higher speed. Programming Data Registers and Internal Relays To enable the modem mode and communicate through the telephone line, the following settings are needed. 1. Program to move 6 (7, 14, or 15) to data register D499 to enable expansion control register service for D486 through D495. 2. Program to move 1 to data register D495 to enable the modem mode. 3. Program the destination telephone number if dialing is required. Enter the ASCII values of the telephone number to data registers starting with D160. Store two characters each in one data register. Enter 0Dh at the end of the telephone num- ber. See page 4-4. 4. Program to move 0 or 1 to data register D101 depending on your modem. When you use AIWA’s modem, enter 0 to use the default initialization string. When you use OMRON’s modem, enter 1 to substitute \Q2 for \Q3 in the default initial- ization string. 5. If the default initialization string does not match your modem, program a proper initialization string and enter the ASCII values to data registers starting with D135. Make sure that internal relay M260 (initialization string start IR) is turned on after the new values have been stored to the data registers. See page 4-3. 6. If you want to change the default value of 3 retry cycles, program to move a required value to data register D100. 7. Include internal relays M260 through M287 in the user program to control the modem communication as required. Since the modem mode uses control data registers D488 through D490 to control the RTS, DTR, Caution and DSR signals, do not enter any value to these data registers while the modem mode is enabled. 4-8 USER’S MANUAL 4: MODEM MODE Operating Procedure 3 1. After completing the user program including FUN8 settings, transfer the user program to the MICRO C from the pro- gram loader or a computer running CUBIQ through the loader port or the data link terminals. To transfer the user pro- gram, the loader port or the data link terminals must be set to loader protocol using the protocol selector switch. For example, when transferring the user program from the program loader through the data link terminals, set the protocol selector switch to 2, 3, or 4. 2. After transferring the user program, set the protocol selector switch to 1 or 3 to select user protocol for the loader port. Press the communication enable button for 4 seconds until the ERR1 indicator blinks once, if necessary. 3 3. Start the MICRO C to run the user program. 4. Turn start internal relay M260 or M265 on to initialize the modem. When originating the modem communication, turn M260 on to send the initialization string, the ATZ command, and the dial command. If the initialization string has been stored in the non-volatile memory of the modem, turn M261 on to start with the ATZ command followed by the dial command. When answering an incoming call, turn M265 on send the initialization string and the ATZ command. If the initializa- tion string has been stored in the non-volatile memory of the modem, turn M266 on to send the ATZ command only. 5. Transmit or receive communication through the modem. 6. Turn start internal relay M263 to disconnect the telephone line. Sample Program for Modem Originate Mode This program demonstrates a user program for the modem originate mode to move values to data registers, initialize the modem, dial the telephone number, and disconnect the telephone line. M301 is the initialize pulse special internal relay. MOV S1 D1 REP 6 D499 ** M301 Six MOV instructions are used to store values to data registers for the modem mode. MOV S1 D1 REP 1 D495 ** 6 → D499 to enable control data register service for D486 through D495. MOV S1 D1 REP 1 → D495 to enable the modem mode. 21554 D160 ** 21554 (5432h) → D160 to designate touch tone and telephone number. MOV S1 D1 REP CR LF 54h = “T”, 32h = “2” (Dial command ATDT2 ) 3328 D161 ** 3328 (0D00h) → D161 to enter CR at the end of the telephone number. MOV S1 D1 REP 0 D492 0 → D492 to enable loader protocol for the loader port after connecting the ** telephone line. MOV S1 D1 REP 0 D101 0 → D101 to use \Q3 in the default initialization string. ** M317 is the in-operation output special internal relay. T0 100 M317 3 Timer T0 starts to time down when the MICRO C is started to run. SOTU When timer T0 times out 10 seconds, M260 is turned on to send the initial- T0 M260 ization string, ATZ, and dial command to the modem. SOTU When input I0 is turned on, M263 is turned on to disconnect the telephone I0 M263 line. END 3 Note: If the MICRO C status transition occurs while a user communication TXD or RXD instruction is executed, the user communication is invalidated. Such status transitions include: • Modem mode is enabled (6 is set to D499 and 1 is set to D495) • Telephone line is connected • Loader port communication protocol is changed to loader protocol (0 is set to D492) USER’S MANUAL 4-9 4: MODEM MODE Checking Modem Operation ConŢrm the modem operation referring to the user’s manual for your modem. Indicator names may differ depending on the brand and model of modems but have the same functions. 1. Make sure the modem is powered up. The POWER indicator must be on. 3 2. Check that the modem’s DTR indicator is on while the MICRO C is in operation. Problem: The DTR indicator is not on. Solution 1: Check the modem cable connection using a VOM. Solution 2: Check that control signal options (D488 through D490) have not been changed. Check that control signal status data register D491 holds a value 4 through 7, indicating that the DTR is on. Above 1 and 2 are conŢrmed, but modem operation still has a problem. 3. It is not clear if an AT command is issued successfully. Problem: Modem mode status data register D493 does not hold a value 30h or 34h. Solution: Enable the modem mode; set the protocol selector switch to 1 or 3, enter 6 to data register D499, and enter 1 to data register D495. Problem: Modem mode status data register D493 holds a value 32h (AT command execution error). Solution: Use the communication monitor function on the program loader or a computer running CUBIQ. Connect the program loader to the data link terminals, and set the protocol selector switch to 3 as shown on page 3 3-1. Use FUN50 user communication data monitor. Start the MICRO C to run, and issue an AT command. Check to see if the AT command and result code are displayed on the program loader. Problem: The AT command is displayed, but the result code is not displayed on the program loader. Solution: Check the modem’s TXD and RXD signal lines are connected correctly. Problem: Modem mode status D493 holds a value 33h. Solution: Check if two or more start internal relays are on simultaneously. If so, correct the user program to make sure that only one start internal relay is on at a time. 4. An AT command is issued successfully and a result code is received, but the following problem occurs. Problem: When a dial command is issued, “NO DIALTONE” is returned and stored in the AT command result code data registers starting with D104. Solution 1: Check that the modular cable is plugged into the LINE jack on the modem. If the modular cable is plugged into the TEL jack on the modem, plug the cable to the LINE jack. Solution 2: When dialing an outside number in a PBX environment, insert the digit used to obtain an outside line after ATDT or ATDP, followed by the W modiŢer (wait for dial tone) or the , modiŢer (delay a dial sequence). Problem: When a dial command is issued repeatedly, “NO CARRIER” is returned and stored in the AT command result code data registers starting with D104. Solution: Make sure that the same communication parameters and initialization string are set on both the local and remote modems. 4-10 USER’S MANUAL 5: USER COMMUNICATION INSTRUCTIONS Introduction This chapter describes the programming of the TXD (transmit) instruction and RXD (receive) instruction for user commu- nication. 3 With the protocol selector switch set to 1 or 3 to select user protocol for the loader port, MICRO C can transmit data using the TXD instruction through the loader port to an RS232C remote terminal, such as a computer, printer, or modem. 3 MICRO C can also receive data through the loader port from a remote terminal with an RS232C port. The received data is converted and stored in data registers as designated by the RXD instruction. B1 TXD (Transmit) When input is on, data designated by S1 is converted into a speciŢed format TXD S1 D1 D2 and transmitted through the loader port to a remote terminal with an ***** **** **** RS232C port. Key Operation B Enter operands S1, D1, and D2. 1 1 S1 (Data) ADV REP Detailed key operation is described on page 5-6. BPS TXD To exit, press the key. D1: M 0 D2: D 0 Valid Operands (Standard Processing) Operand Function I Q M T C R D Constant Repeat S1 (Source 1) Transmit data — — — — — — 0-498 00h-FFh 1-99 D1 (Destination 1) Transmit completion output — 0-31 0-287 — — — — — — D2 (Destination 2) Transmit status — — — — — — 0-497 — — Transmit data designated by operand S1 can be a maximum of 200 bytes. When transmission is complete, an output or internal relay, designated by operand D1, is turned on. Destination 2 occupies two consecutive data registers starting with the operand designated by D2. The transmit status data register, designated by D2, stores the status of transmission and error code. The next data register stores the byte count of transmitted data. The same data registers cannot be used as transmit status data registers for TXD instructions and receive status data registers for RXD instructions. If the same data register numbers are programmed as status data registers for TXD and RXD instructions, syntax error 80 will result. Precautions for Programming TXD Instruction 3 1. MICRO C has 5 formatting areas for executing TXD instructions, so more than 5 TXD instructions cannot be executed at the same time. An error code is set to the transmit status data register, designated by operand D2, in the excessive TXD instructions that cannot be executed. 2. If the input for a TXD instruction is turned on while another TXD instruction is executed, the subsequent TXD instruc- tion is executed 2 scan time after the preceding TXD instruction is completed. 3. Since TXD instructions are executed in each scan while input is on, a pulse input from a SOTU or SOTD instruction should be used as required. 4. In the high-speed processing mode, user communication instructions TXD and RXD cannot be used. USER’S MANUAL 5-1 5: USER COMMUNICATION INSTRUCTIONS Transmit Data Transmit data is designated by source operand S1 using constant values or data registers. BCC code can also be calculated automatically and appended to the transmit data. One TXD instruction can transmit 200 bytes of data at the maximum. S1 (Source 1) Transmit Digits Calculation Transmit Data Operand Conversion Type Repeat Calculation (Bytes) Start Position Constant 00h-FFh (7Fh) No conversion 1 — — — A: Binary→ASCII 1-4 Data Register D0-D498 B: Binary→BCD→ASCII 1-5 1-99 — — –: No conversion 1-2 A: Binary→ASCII X: XOR BCC — 1-2 — 1-15 –: No conversion A: ADD Designating Constant as S1 When a constant value is designated as source operand S1, one-byte data is transmitted without conversion. The valid transmit data value depends on the data bits selected in FUN8 loader port communication mode setting. When 8 data bits are selected, 00h through FFh is transmitted. When 7 data bits are selected as default, 00h through 7Fh is transmitted. Con- stant values are entered in hexadecimal notation into the source data. Designating Data Register as S1 When a data register is designated as source operand S1, conversion type and transmit digits must also be designated. The data stored in the designated data register is converted and a designated quantity of digits of the resultant data is transmit- ted. Conversion types are available in Binary→ASCII, Binary→BCD→ASCII, and no conversion. When repeat is designated, data of data registers as many as the repeat cycles are transmitted, starting with the designated data register. Repeat cycles can be up to 99. Conversion Type The transmit data is converted according to the designated conversion type as described below: Example: D10 stores 000Ch (12) (1) Binary→ASCII conversion “0” “0” “0” “C” 000Ch D10 (30h) (30h) (30h) (43h) Binary→ASCII conversion When transmitting 4 digits (2) Binary→BCD→ASCII conversion “0” “0” “0” “1” “2” 000Ch 00012 D10 (30h) (30h) (30h) (31h) (32h) Binary→BCD conversion BCD→ASCII conversion When transmitting 5 digits (3) No conversion FF D10 000Ch (00h) (0Ch) No conversion When transmitting 2 digits 5-2 USER’S MANUAL 5: USER COMMUNICATION INSTRUCTIONS Transmit Digits (Bytes) After conversion, the transmit data is taken out in speciŢed digits. Possible digits depend on the selected conversion type. Example: D10 stores 000Ch (12) and is converted in Binary→BCD→ASCII (1) Transmit Digits = 2 “0” “0” “0” “1” “2” “1” “2” D10 000Ch (30h) (30h) (30h) (31h) (32h) (31h) (32h) Binary→BCD→ASCII conversion Intermediate result of conversion Lowest 2 digits (2) Transmit Digits = 1 “0” “0” “0” “1” “2” “2” 000Ch D10 (30h) (30h) (30h) (31h) (32h) (32h) Binary→BCD→ASCII conversion Intermediate result of conversion Lowest 1 digit Repeat Cycles When a data register is designated to repeat, consecutive data registers, as many as the repeat cycles, are used for transmit data in the same conversion type and transmit digits. Example: Data register D10 is converted in Binary→BCD→ASCII and is designated with transmit digits 2. (1) Repeat Cycles = 2 “1” “2” “3” “4” (31h) (32h) (33h) (34h) Repeat 1 D10 000Ch 00012 Repeat 2 D11 0022h 00034 Binary→BCD conversion BCD→ASCII conversion (2) Repeat Cycles = 3 “1” “2” “3” “4” “5” “6” (31h) (32h) (33h) (34h) (35h) (36h) Repeat 1 D10 000Ch 00012 Repeat 2 0022h 00034 D11 Repeat 3 D12 0038h 00056 Binary→BCD conversion BCD→ASCII conversion BCC (Block Check Character) Block check characters can be appended to the transmit data. The start position for the BCC calculation can be speciŢed from the Ţrst byte through the 15th byte. The BCC, calculated in either XOR or ADD, can be 1 or 2 digits. 1st 2nd 3rd 4th 5th 6th 15th 16th 17th 18th 19th STX “A” “B” “C” “D” “E” “0” CR LF BCC BCC BCC calculation start position can be selected from this range. BCC (2 digits) BCC calculation range when starting with the 1st byte of the data. USER’S MANUAL 5-3 5: USER COMMUNICATION INSTRUCTIONS BCC Calculation Start Position The start position for the BCC calculation can be speciŢed from the Ţrst byte through the 15th byte. The BCC is calculated for the range starting from the designated position up to the byte immediately before the BCC of the transmit data. Example: Transmit data consists of 17 bytes plus 2 BCC digits. (1) Calculation Start Position = 1 1st 2nd 3rd 4th 5th 6th 15th 16th 17th 18th 19th STX “A” “B” “C” “D” “E” “0” CR LF BCC BCC BCC calculation range BCC (2 digits) (2) Calculation Start Position = 2 1st 2nd 3rd 4th 5th 6th 15th 16th 17th 18th 19th STX “A” “B” “C” “D” “E” “0” CR LF BCC BCC BCC calculation range BCC (2 digits) BCC Calculation Formula BCC calculation formula can be selected from XOR (exclusive OR) or ADD (addition) operation. Example: Conversion results of transmit data consist of 41h, 42h, 43h, 44h, and 45h. (1) BCC Calculation Formula = XOR 41h ⊕ 42h ⊕ 43h ⊕ 44h ⊕ 45h = 41h (2) BCC Calculation Formula = ADD 41h + 42h + 43h + 44h + 45h = 14Fh → 4Fh (Only the last 1 or 2 digits are used as BCC.) Conversion Type The BCC calculation result can be converted or not according to the designated conversion type as described below: Example: BCC calculation result is 0041h. (1) Binary→ASCII conversion “4” “1” 0041h (34h) (31h) Binary→ASCII conversion 2 digits (2) No conversion “A” 0041h (00h) (41h) No conversion 2 digits BCC Digits (Bytes) The quantity of digits (bytes) of the BCC code can be selected from 1 or 2. Example: “4” “1” “4” “1” (1) BCC Digits = 2 (34h) (31h) (34h) (31h) “4” “1” “1” (2) BCC Digits = 1 (34h) (31h) (31h) 5-4 USER’S MANUAL 5: USER COMMUNICATION INSTRUCTIONS Transmit Completion Output Designate an output, Q0 through Q31, or an internal relay, M0 through M287, as an operand for the transmit completion output. When the start input for a TXD instruction is turned on, preparation for transmission is initiated, followed by data trans- mission. When a sequence of all transmission operation is complete, the designated output or internal relay is turned on. Transmit Status Designate a data register, D0 through D497, as an operand to store the transmit status information including a transmission status code and a user communication error code. When the data register designated for the transmit status is monitored in hexadecimal notation on the program loader, the second lowest digit indicates a transmission status code and the lowest digit indicates a user communication error code. If no error exists, the lowest digit indicates 0. To view the transmit status, monitor the designated data register in hexadecimal notation on the program loader. Example: Data register D0 is designated as an operand for the transmit status. E OUT MON OR MON 0 D 16 D 0 $ 40 User communication error code (see page 11-2) Transmit status code (see below) Transmit Status Code Transmit Status Description Status Code From turning on the start input for a TXD instruction, until the transmit 1 Preparing transmission data is stored in the internal transmit buffer From enabling data transmission by an END processing, until all data 2 Transmitting data transmission is completed From completing all data transmission, until the END processing is 3 Data transmission complete completed for the TXD instruction All transmission operation is completed and the next transmission is 4 Transmit instruction complete made possible Data transmission may be aborted depending on an error. If data transmission is aborted by an error, remove the cause of the error and turn the start input for the TXD instruction on again. For error codes and causes, see User Communication Error Code on page 11-2. Transmit Data Byte Count The data register next to the operand designated for transmit status stores the byte count of data transmitted by the TXD instruction. When BCC is included in the transmit data, the byte count of the BCC is also included in the transmit data byte count. Example: Data register D100 is designated as an operand for transmit status. Transmit status D100 Transmit data byte count D101 USER’S MANUAL 5-5 5: USER COMMUNICATION INSTRUCTIONS Key Operation for Programming TXD Instruction on Program Loader The following example demonstrates how to program a TXD instruction using the program loader. Data register contents: D010 04D2h = 1234 D011 162Eh = 5678 Transmit data example: BCC calculation range BCC BCC STX “1” “2” “3” “4” “5” “6” “7” “8” ETX (H) (L) (02h) (31h) (32h) (33h) (34h) (35h) (36h) (37h) (38h) (03h) (3Ah) (36h) Constant D10 D11 BCC Constant Start to program a TXD instruction. B 1 1 S1 (Data) Source 1 (transmit data) ADV REP BPS TXD Destination 1 (transmit completion output) D1: M 0 Destination 2 (transmit status) D2: D 0 Enter hexadecimal constant value 02 for STX as transmit data. OUT 2 1 STX (02) BRD 16 2 --- Constant 3 --- 4 --- Designate data register D10, binary→BCD→ASCII conversion, 4 transmit digits, and 2 repeat cycles for the next transmit data. E B 1 4 2 OR 0 REP BPS BRD D When repeat cycle is 1, these keys may be omitted. 1 STX (02) 2 D 10 B4 2 10 --- Repeat cycles 11 --- Transmit digits Conversion type (selected using the REP key) A: Binary→ASCII conversion B: Binary→BCD→ASCII conversion –: No conversion Data register as transmit data source Data position (Nth byte) 1 23456789 10 11 12 BCC BCC STX “1” “2” “3” “4” “5” “6” “7” “8” ETX (H) (L) (02h) (31h) (32h) (33h) (34h) (35h) (36h) (37h) (38h) (03h) (3Ah) (36h) Constant D10 D11 BCC Constant 5-6 USER’S MANUAL 5: USER COMMUNICATION INSTRUCTIONS Enter a BCC code of 2 digits calculated using the ADD format, binary→ASCII conversion; calculation is started at the Ţrst byte of the transmit data. B B B 2 1 REP REP REP BRD BPS When BCC calculation starts at the Ţrst byte, these keys may be omitted. 1 STX (02) 2 D 10 B4 2 10 BCC AA2 1 12 --- Calculation start position Quantity of digits Conversion type (selected using the REP key) A: Binary→ASCII conversion –: No conversion Calculation format (selected using the REP key) X: XOR (exclusive OR) A: ADD (addition) Enter hexadecimal constant value 03 for ETX at the end of transmit data. OUT 3 2 D 10 B4 2 BPP 16 10 BCC AA2 1 12 ETX (03) 13 --- Constant Designate internal relay M10 as an operand for transmit completion output. C 1 1 S1:(Data) SOT 0 BPS M TXD To edit the source 1 data, move D1: M 10 the cursor to the colon, and D2 D 0 press the key. Designate data register D100 as an operand for transmit status. E 1 1 S1:(Data) OR 0 0 BPS D TXD D100: Transmit status D1: M 10 D101: Transmit data byte count D2 D100 Complete the programming of the TXD instruction. Pressing the key writes the TXD instruction into the program 0 LOD I 0 loader memory. To discard the edited data before pressing the 1 (TXD ) key, press the CLR key. 10 END 11 END Editing the TXD Instruction To edit an existing TXD instruction, move the cursor to the left of the (TXD), and press the key; then the TXD editor screen appears. To edit the source 1 data, press the key again with the cursor at the left of the (Data), and follow the same procedure described above. USER’S MANUAL 5-7 5: USER COMMUNICATION INSTRUCTIONS B2 RXD (Receive) When input is on, data received through the loader port from a remote ter- RXD S1 D1 D2 minal with an RS232C port is converted and stored in data registers accord- ***** **** **** ing to the receive format designated by S1. Key Operation B Enter operands S1, D1, and D2. 2 1 S1 (Data) ADV REP Detailed key operation is described on page 5-17. BRD RXD To exit, press the key. D1: M 0 D2: D 0 Valid Operands (Standard Processing) Operand Function I Q M T C R D Constant Repeat S1 (Source 1) Receive format — — — — — — 0-498 00h-FFh 1-99 D1 (Destination 1) Receive completion output — 0-31 0-287 — — — — — — D2 (Destination 2) Receive status — — — — — — 0-497 — — Receive format designated by operand S1 can be a maximum of 200 bytes. When data receive is complete, an output or internal relay, designated by operand D1, is turned on. Destination 2 occupies two consecutive data registers starting with the operand designated by D2. The receive status data register, designated by D2, stores the status of data receive and error code. The next data register stores the byte count of received data. The same data registers cannot be used as transmit status data registers for TXD instructions and receive sta- tus data registers for RXD instructions. If the same data register numbers are programmed as status data registers for TXD and RXD instructions, syntax error 80 will result. Precautions for Programming RXD Instruction 3 1. MICRO C can execute a maximum of 5 RXD instructions that have a start delimiter at the same time. If a start delimiter 3 is not programmed in RXD instructions, MICRO C can execute only one receive instruction at a time. If the start input for an RXD instruction is turned on while another RXD instruction without a start delimiter is executed, a user commu- nication error occurs. 2. Since RXD instructions are executed in each scan while input is on, a pulse input from a SOTU or SOTD instruction should be used as required. 3. In the high-speed processing mode, user communication instructions RXD and TXD cannot be used. 5-8 USER’S MANUAL 5: USER COMMUNICATION INSTRUCTIONS Receive Format Receive format, designated by source operand S1, speciŢes data registers to store received data, data digits for storing data, data conversion type, and repeat cycles. A start delimiter and an end delimiter can be included in the receive format to discriminate valid incoming communication. When some characters in the received data are not needed, “skip” can be used to ignore a speciŢed number of characters. BCC code can also be appended to the receive format to verify the received data. One RXD instruction can receive 200 bytes of data at the maximum. S1 (Source 1) Receive Calculation Receive Skip Operand Digits Conversion Type Repeat Calculation Start Format Bytes (Bytes) Position 1-4 A: ASCII→Binary Data Register D0-D498 1-5 B: ASCII→BCD→Binary 1-99 — — — 1-2 –: No conversion Start Delimiter 00h-FFh (7Fh) 1 No conversion — — — — End Delimiter 00h-FFh (7Fh) 1 No conversion — — — — A: Binary→ASCII X: XOR BCC — 1-2 — 1-15 — –: No conversion A: ADD Skip — — — — — — 1-99 Designating Data Register as S1 When a data register is designated as source operand S1, receive digits and conversion type must also be designated. The received data is divided into a block of speciŢed receive digits, converted in a speciŢed conversion type, and stored in the designated data register. Conversion types are available in ASCII→Binary, ASCII→BCD→Binary, and no conversion. When repeat is designated, received data is divided, converted, and stored in data registers as many as the repeat cycles, starting with the designated data register. Repeat cycles can be up to 99. Receive Digits The received data is divided into a block of speciŢed receive digits before conversion as described below: Example: Received data of 6 bytes are divided in different receive digits. (Repeat is also designated.) (1) Receive Digits = 2 “1” “2” “3” “4” “5” “6” (31h) (32h) (33h) (34h) (35h) (36h) 2 digits 2 digits 2 digits 1st block 2nd block 3rd block (2) Receive Digits = 3 “1” “2” “3” “4” “5” “6” (31h) (32h) (33h) (34h) (35h) (36h) 3 digits 3 digits 1st block 2nd block USER’S MANUAL 5-9 5: USER COMMUNICATION INSTRUCTIONS Conversion Type The data block of the speciŢed receive digits is then converted according to the designated conversion type as described below: Example: Received data has been divided into a 2-digit block. (1) ASCII→Binary conversion “1” “2” 0012h (31h) (32h) ASCII→Binary conversion (2) ASCII→BCD→Binary conversion “1” “2” 00012 000Ch (31h) (32h) ASCII→BCD conversion BCD→Binary conversion (3) No conversion “1” “2” 3132h (31h) (32h) No conversion Repeat Cycles When a data register is designated to repeat, the received data is divided and converted in the same way as speciŢed, and the converted data is stored in consecutive data registers as many as the repeat cycles. Example: Received data of 6 bytes is divided into 2-digit blocks, converted in ASCII→Binary, and stored to data registers starting at D20. (1) Repeat Cycles = 2 “1” “2” “3” “4” (31h) (32h) (33h) (34h) 2 digits 2 digits 1st block 2nd block ASCII→Binary conversion D20 0012h Repeat 1 0034h D21 Repeat 2 (1) Repeat Cycles = 3 “1” “2” “3” “4” “5” “6” (31h) (32h) (33h) (34h) (35h) (36h) 2 digits 2 digits 2 digits 1st block 2nd block 3rd block ASCII→Binary conversion D20 0012h Repeat 1 0034h D21 Repeat 2 D22 0056h Repeat 3 5-10 USER’S MANUAL 5: USER COMMUNICATION INSTRUCTIONS Designating Constant as Start Delimiter 3 A start delimiter can be programmed at the Ţrst byte in the receive format of an RXD instruction; the MICRO C will recog- nize the beginning of valid communication, although an RXD instruction without a start delimiter can also be executed. When a constant value is designated at the Ţrst byte of source operand S1, the one-byte data serves as a start delimiter to start the processing of the received data. The valid start delimiter value depends on the data bits selected in FUN8 loader port communication mode setting. When 8 data bits are selected, start delimiters can be 00h through FFh. When 7 data bits are selected as default, start delimiters can be 00h through 7Fh. Constant values are entered in hexadecimal notation into the source data. A maximum of 5 RXD instructions with different start delimiters can be executed at the same time. When the Ţrst byte of the incoming data matches the start delimiter of an RXD instruction, the received data is processed and stored according to the receive format speciŢed in the RXD instruction. If the Ţrst byte of the incoming data does not match the start delimiter 3 of any RXD instruction that is executed, MICRO C discards the incoming data and waits for the next communication. While an RXD instruction without a start delimiter is executed, any incoming data is processed continuously according to the receive format. Only one RXD instruction without a start delimiter can be executed at a time. If start inputs to two or more RXD instructions without a start delimiter are turned on simultaneously, one at the smallest address is executed and the corresponding completion output is turned on. Example: (1) When an RXD instruction without a start delimiter is executed Incoming Data When D100 is designated as the first data register “0” “1” “2” “3” h D100 **** (30h) (31h) (32h) (33h) D101 h **** 1st character h D100+n **** The incoming data is divided, converted, and stored to data registers according to the receive format. (2) When RXD instructions with start delimiters STX (02h) and ENQ (05h) are executed Incoming Data STX “1” “2” “3” (02h) (31h) (32h) (33h) ENQ “A” “B” “C” (05h) (41h) (42h) (43h) D100 h **** RXD Instruction 1 D101 h **** STX (02h) When D100 is designated as the first data register D100+n h **** Compare D200 h **** RXD Instruction 2 D201 h **** ENQ (05h) When D200 is designated as the first data register D200+n h **** The incoming data is divided, converted, and stored to data registers according to the receive format. Start delimiters are not stored to data registers. USER’S MANUAL 5-11 5: USER COMMUNICATION INSTRUCTIONS Designating Constant as End Delimiter 3 An end delimiter can be programmed at other than the Ţrst byte in the receive format of an RXD instruction; the MICRO C will recognize the end of valid communication, although RXD instructions without an end delimiter can also be executed. When a constant value is designated at other than the Ţrst byte of source operand S1, the one-byte data serves as an end delimiter to end the processing of the received data. The valid end delimiter value depends on the data bits selected in FUN8 loader port communication mode setting. When 8 data bits are selected, end delimiters can be 00h through FFh. When 7 data bits are selected as default, end delimiters can be 00h through 7Fh. Constant values are entered in hexadeci- mal notation into the source data. If a character in incoming data matches the end delimiter, the RXD instruction ends receiving data at this point and starts subsequent receive processing as speciŢed. Even if a character matches the end delimiter at a position earlier than expected, the RXD instruction ends receiving data there. If a BCC code is included in the receive format of an RXD instruction, an end delimiter can be positioned immediately before or after the BCC code. If a data register or skip is designated between the BCC and end delimiter, correct receiving is not ensured. When an RXD instruction without an end delimiter is executed, data receiving ends when the speciŢed bytes of data in the receive format, such as data registers and skips, have been received. In addition, data receiving also ends when the interval between incoming data characters exceeds the receive timeout value speciŢed in FUN8 loader port communication mode setting whether the RXD has an end delimiter or not. The character interval timer is started when the Ţrst character of incoming communication is received and restarted each time the next character is received. When a character is not received after a predetermined time, timeout occurs and the RXD ends data receive operation. Example: (1) When an RXD instruction without an end delimiter is executed D100 h Incoming Data When D100 is designated **** as the first data register “0” “1” “2” “3” h D101 **** (30h) (31h) (32h) (33h) Total of received characters D100+n h **** The incoming data is divided, converted, and stored to data registers according to the receive format. Receive operation is completed when the total characters programmed in RXD are received. (2) When an RXD instruction with end delimiter ETX (03h) and without BCC is executed h Incoming Data When D100 is designated D100 **** as the first data register “1” “2” “3” ETX D101 h **** (31h) (32h) (33h) (03h) End Delimiter h End of Receiving Data D100+n **** The incoming data is divided, converted, and stored to data registers according to the receive format. The end delimiter is not stored to a data register. Any data arriving after the end delimiter is discarded. (3) When an RXD instruction with end delimiter ETX (03h) and one-byte BCC is executed D100 h Incoming Data When D100 is designated **** as the first data register “1” “2” ETX BCC D101 h **** (31h) (32h) (03h) Code End Delimiter End of Receiving Data D100+n h **** The incoming data is divided, converted, and stored to data registers according to the receive format. The end delimiter and BCC code are not stored into data registers. 3 After receiving the end delimiter, MICRO C receives only the one-byte BCC code. 5-12 USER’S MANUAL 5: USER COMMUNICATION INSTRUCTIONS Skip When “skip” is designated in the receive format, a speciŢed quantity of digits in the incoming data are skipped and not stored to data registers. A maximum of 99 digits (bytes) of characters can be skipped continuously. Example: When an RXD instruction with skip for 2 digits starting at the third byte is executed Incoming Data “1” “2” “3” “4” “5” “6” “7” “8” (31h) (32h) (33h) (34h) (35h) (36h) (37h) (38h) D102 h **** Skipped h D103 **** D104 h **** D105 h **** When D100 is designated as the first data register h D100 **** D101 h **** BCC (Block Check Character) 3 MICRO C has an automatic BCC calculation function to detect a communication error in incoming data. If a BCC code is 3 designated in the receive format of an RXD instruction, MICRO C calculates a BCC value for a speciŢed starting position through the position immediately preceding BCC and compares the calculation result with the BCC code in the received incoming data. The start position for the BCC calculation can be speciŢed from the Ţrst byte through the 15th byte. The BCC, calculated in either XOR or ADD, can be 1 or 2 digits. When an end delimiter is not used in the RXD instruction, the BCC code must be positioned at the end of the receive for- mat designated in Source 1 operand. When an end delimiter is used, the BCC code must be immediately before or after the 3 end delimiter. MICRO C reads a speciŢed number of BCC digits in the incoming data according to the receive format to calculate and compare the received BCC code with the BCC calculation results. BCC Calculation Start Position The start position for the BCC calculation can be speciŢed from the Ţrst byte through the 15th byte. The BCC is calculated for the range starting from the designated position up to the byte immediately before the BCC of the receive data. Example: Received data consists of 17 bytes plus 2 BCC digits. (1) Calculation Start Position = 1 1st 2nd 3rd 4th 5th 6th 15th 16th 17th 18th 19th STX “A” “B” “C” “D” “E” “0” CR LF BCC BCC BCC calculation range BCC (2 digits) (2) Calculation Start Position = 2 1st 2nd 3rd 4th 5th 6th 15th 16th 17th 18th 19th STX “A” “B” “C” “D” “E” “0” CR LF BCC BCC BCC calculation range BCC (2 digits) USER’S MANUAL 5-13 5: USER COMMUNICATION INSTRUCTIONS BCC Calculation Formula BCC calculation formula can be selected from XOR (exclusive OR) or ADD (addition) operation. Example: Incoming data consist of 41h, 42h, 43h, 44h, and 45h. (1) BCC Calculation Formula = XOR 41h ⊕ 42h ⊕ 43h ⊕ 44h ⊕ 45h = 41h (2) BCC Calculation Formula = ADD 41h + 42h + 43h + 44h + 45h = 14Fh → 4Fh (Only the last 1 or 2 digits are used as BCC.) Conversion Type The BCC calculation result can be converted or not according to the designated conversion type as described below: Example: BCC calculation result is 0041h. (1) Binary→ASCII conversion “4” “1” 0041h (34h) (31h) Binary→ASCII conversion 2 digits (2) No conversion “A” 0041h (00h) (41h) No conversion 2 digits BCC Digits (Bytes) The quantity of digits (bytes) of the BCC code can be selected from 1 or 2. Example: “4” “1” “4” “1” (1) BCC Digits = 2 (34h) (31h) (34h) (31h) “4” “1” “1” (2) BCC Digits = 1 (34h) (31h) (31h) 5-14 USER’S MANUAL 5: USER COMMUNICATION INSTRUCTIONS Comparing BCC Codes 3 MICRO C compares the BCC calculation result with the BCC code in the received incoming data to check for any error in the incoming communication due to external noises or other causes. If a disparity is found in the comparison, an error code is stored in the data register designated as receive status in the RXD instruction. For user communication error code, see page 11-2. Example 1: BCC is calculated for the Ţrst byte through the sixth byte using the XOR format, converted in binary→ASCII, and compared with the BCC code appended to the seventh and eighth bytes of the incoming data. Incoming Data “1” “2” “3” “4” “5” “6” “0” “7” (31h) (32h) (33h) (34h) (35h) (36h) (30h) (37h) BCC Calculation Range BCC Comparison result is true to indicate BCC Calculation Result that data is received correctly. 31h ⊕ 32h ⊕ 33h ⊕ 34h ⊕ 35h ⊕ 36h = 07h Binary→ASCII Conversion “0” “7” (30h) (37h) Example 2: BCC is calculated for the Ţrst byte through the sixth byte using the ADD format, converted in binary→ASCII, and compared with the BCC code appended to the seventh and eighth bytes of the incoming data. Incoming Data “1” “2” “3” “4” “5” “6” “0” “7” (31h) (32h) (33h) (34h) (35h) (36h) (30h) (37h) BCC Calculation Range BCC Comparison result is false. BCC Calculation Result Error code 9 is stored in the receive 31h + 32h + 33h + 34h + 35h + 36h = 135h status data register. Binary→ASCII Conversion “3” “5” (33h) (35h) Receive Completion Output Designate an output, Q0 through Q31, or internal relay, M0 through M287, as an operand for the receive completion out- put. When the start input for an RXD instruction is turned on, preparation for receiving data is initiated, followed by data con- version and storage. When a sequence of all data receive operation is complete, the designated output or internal relay is turned on. USER’S MANUAL 5-15 5: USER COMMUNICATION INSTRUCTIONS Receive Status Designate a data register, D0 through D497, as an operand to store the receive status information including a receive status code and a user communication error code. When the data register designated for the receive status is monitored in hexadecimal notation on the program loader, the second lowest digit indicates a receive status code and the lowest digit indicates a user communication error code. If no error exists, the lowest digit indicates 0. To view the receive status, monitor the designated data register in hexadecimal notation on the program loader. Example: Data register D0 is designated as an operand for the receive status. E OUT MON OR MON 0 D 16 D 0 $ 40 User communication error code (see page 11-2) Receive status code (see below) Receive Status Code Receive Status Description Status Code From turning on the start input for an RXD instruction to read the 1 Preparing data receive receive format, until the RXD instruction is enabled by an END pro- cessing From enabling the RXD instruction by an END processing, until incom- 2 Receiving data ing data is received From receiving incoming data, until the received data is converted and 3 Data receive complete stored in data registers according to the receive format All data receive operation is completed and the next data receive is 4 Receive instruction complete made possible Data receive may be aborted depending on an error. If data receive is aborted by an error, remove the cause of the error and turn the start input for the RXD instruction on again. For error codes and causes, see User Communication Error Code on page 11-2. Receive Data Byte Count The data register next to the operand designated for receive status stores the byte count of data received by the RXD instruction. When a start delimiter, end delimiter, and BCC are included in the received data, the byte counts for these codes are also included in the receive data byte count. Example: Data register D200 is designated as an operand for receive status. Receive status D200 Receive data byte count D201 5-16 USER’S MANUAL 5: USER COMMUNICATION INSTRUCTIONS Key Operation for Programming RXD Instruction on Program Loader The following example demonstrates how to program an RXD instruction including a start delimiter, skip, BCC, and end delimiter using the program loader. Converted data is stored to data registers D20 and D21. Internal relay M20 is used as destination D1 for the receive completion output. Data register D200 is used as destination D2 for the receive status, and data register D201 is used to store the receive data byte count. Receive data example: BCC calculation range BCC BCC STX “1” “2” “3” “4” “5” “6” “7” “8” “9” “0” “A” “B” ETX (H) (L) (02h) (31h) (32h) (33h) (34h) (35h) (36h) (37h) (38h) (39h) (30h) (41h) (42h) (39h) (32h) (03h) Start Skip Stored to D20 Stored to D21 BCC End Delimiter Delimiter Start to program an RXD instruction. B 2 1 S1 (Data) Source 1 (receive format) ADV REP BRD RXD Destination 1 (receive completion output) D1: M 0 Destination 2 (receive status) D2: D 0 Enter hexadecimal constant value 02 for STX as a start delimiter in the receive format. OUT 2 1 STX (02) BRD 16 2 --- A constant entered at the Ţrst 3 --- byte speciŢes the start delimiter. 4 --- Designate 4 bytes to skip. B B 4 1 STX (02) REP REP 2 SKIP 4 6 --- Skip byte count 7 --- Designate data register D20, ASCII→binary conversion, 4 digits, and 2 repeat cycles. E B 2 4 2 OR 0 REP BRD BRD D When repeat cycle is 1, 1 STX (02) these keys may be omitted. 2 SKIP 4 6 D 20 A4 2 14 --- Repeat cycles Receive digits Conversion type (selected using the REP key) A: ASCII→Binary conversion B: ASCII→BCD→Binary conversion –: No conversion Data register to store received data Data position (Nth byte) 1 23456789 10 11 12 13 14 15 16 BCC BCC STX “1” “2” “3” “4” “5” “6” “7” “8” “9” “0” “A” “B” ETX (H) (L) (02h) (31h) (32h) (33h) (34h) (35h) (36h) (37h) (38h) (39h) (30h) (41h) (42h) (03h) (39h) (32h) USER’S MANUAL 5-17 5: USER COMMUNICATION INSTRUCTIONS Enter a BCC code of 2 digits calculated using the ADD format, binary→ASCII conversion; calculation is started at the Ţrst byte of the received data. B B B 2 1 REP REP REP BRD BPS When BCC calculation starts at the Ţrst byte, these keys may be omitted. 2 SKIP 4 6 D 20 A4 2 14 BCC AA2 1 16 --- Calculation start position Quantity of digits Conversion type (selected using the REP key) A: Binary→ASCII conversion –: No conversion Calculation format (selected using the REP key) X: XOR (exclusive OR) A: ADD (addition) Enter hexadecimal constant value 03 for ETX as an end delimiter in the receive format. OUT 3 6 D 20 A4 2 BPP 16 14 BCC AA2 1 A constant entered at other than 16 ETX (03) the Ţrst byte speciŢes the end 17 --- delimiter. Designate internal relay M20 as an operand for receive completion output. C 2 1 S1:(Data) SOT 0 BRD M RXD To edit the source 1 data, move D1: M 20 the cursor to the colon, and D2 D 0 press the key. Designate data register D200 as an operand for receive status. E 2 1 S1:(Data) OR 0 0 BRD D TXD D200: Receive status D1: M 20 D201: Receive data byte count D2 D200 Complete the programming of the RXD instruction. Pressing the key writes the RXD instruction into the program 0 LOD I 1 loader memory. To discard the edited data before pressing the 1 (RXD ) key, press the CLR key. 11 END 12 END Editing the RXD Instruction To edit an existing RXD instruction, move the cursor to the left of the (RXD), and press the key; then the RXD editor screen appears. To edit the source 1 data, press the key again with the cursor at the left of the (Data), and follow the same procedure described above. 5-18 USER’S MANUAL 6: COMPARISON INSTRUCTION Introduction This chapter describes the programming of the CMP2 (double-word comparison) instruction. This instruction is useful to compare data received using the user communication. The CMP2 instruction compares data in data registers. Two consecutive data registers designated by a source operand are compared with two consecutive data registers designated by another source operand. When used with a repeat designation, one CMP2 instruction can execute a maximum of 31 double-word comparison operations. With a repeat designation, the results of all double-word comparisons can be ANDed; so, the comparison results are easily determined, even when com- paring a large amount of data. B3 CMP2 (Double-word Comparison) (S1)(S1+1) = (S2)(S2+1) → D1 on TXD S1(R) S2(R) D1(R) REP When input is on, 32-bit data designated by source operands S1 and **** **** **** ** S1+1 is compared with 32-bit data designated by source operands S2 and S2+1. When (S1)(S1+1) data is equal to (S2)(S2+1) data, destination operand D1 is turned on. When the condition is not met, D1 is turned off. Key Operation B Enter operands S1, S2, and D1. 3 1 S1 ADV REP When repeat is required, press the REP key for the operand BPP CMP2 S2: to repeat, and enter the number of repeat cycles. D1: To exit, press the key. Valid Operands (Standard Processing) Operand Function I Q M T C R D Constant Repeat S1 (Source 1) Data to compare — — — — — — 0-497 — 1-31 S2 (Source 2) Data to compare — — — — — — 0-497 — 1-31 D1 (Destination 1) Comparison output — 0-31 0-287 — — — — — 1-31 In the high-speed processing mode, operands for advanced instructions are limited. See page 2-1. Examples: CMP2 The comparison output is usually maintained while the input to the comparison instruction is off. If the comparison output is on, the on status is maintained when the input is turned off as demonstrated by this program. ON Input I0 CMP2 S1 S2 D1 REP OFF D10 D20 Q0 ** I0 Comparison D10·D11 = D20·D21 D10·D11 ≠ D20·D21 Result ON Comparison Output Q0 OFF This program turns the output off when the input is off. ON Input I0 CMP2 S1 S2 D1 REP OFF D10 D20 M0 I0 ** Comparison D10·D11 = D20·D21 Result D10·D11 ≠ D20·D21 ON M0 Q0 Output Q0 OFF USER’S MANUAL 6-1 6: COMPARISON INSTRUCTION Repeat Operation in the Double-word Comparison Instruction Unlike other advanced instructions, when S1 and/or S2 (source) is designated to repeat and D1 (destination) is not desig- nated to repeat, the comparison results are ANDed and set to one destination. When only S1 (source) is designated to repeat, double-word operands (as many as the repeat cycles, starting with the oper- and designated by S1) are compared with the double-word operand designated by S2. The comparison results are ANDed and set to the operand designated by D1. S1 (Repeat = 3) S2 (Repeat = 0) D1 (Repeat = 0) CMP2 S1 R S2 D1 REP D20·D21 D30·D31 D20 D30 M50 3 I1 D22·D23 D30·D31 AND M50 D24·D25 D30·D31 When only S2 (source) is designated to repeat, the double-word operand designated by S1 is compared with double-word operands (as many as the repeat cycles, starting with the operand designated by S2). The comparison results are ANDed and set to the operand designated by D1. S1 (Repeat = 0) S2 (Repeat = 3) D1 (Repeat = 0) CMP2 S1 S2 R D1 REP D20·D21 D30·D31 D20 D30 M50 3 I2 D20·D21 D32·D33 AND M50 D20·D21 D34·D35 When S1 (source) and S2 (source) are designated to repeat, double-word operands (as many as the repeat cycles, starting with the operands designated by S1 and S2) are compared with each other. The comparison results are ANDed and set to the operand designated by D1. S1 (Repeat = 3) S2 (Repeat = 3) D1 (Repeat = 0) CMP2 S1 R S2 R D1 REP D20·D21 D30·D31 D20 D30 M50 3 I3 D22·D23 D32·D33 AND M50 D24·D25 D34·D35 When S1 (source) and D1 (destination) are designated to repeat, double-word operands (as many as the repeat cycles, starting with the operand designated by S1) are compared with the double-word operand designated by S2. The compari- son results are set to operands (as many as the repeat cycles, starting with the operand designated by D1). S1 (Repeat = 3) S2 (Repeat = 0) D1 (Repeat = 3) CMP2 S1 R S2 D1 R REP D20·D21 D30·D31 M50 D20 D30 M50 3 I4 D22·D23 D30·D31 M51 D24·D25 D30·D31 M52 When S2 (source) and D1 (destination) are designated to repeat, the double-word operand designated by S1 is compared with double-word operands (as many as the repeat cycles, starting with the operand designated by S2). The comparison results are set to operands (as many as the repeat cycles, starting with the operand designated by D1). S1 (Repeat = 0) S2 (Repeat = 3) D1 (Repeat = 3) CMP2 S1 S2 R D1 R REP D20·D21 D30·D31 M50 D20 D30 M50 3 I5 D20·D21 D32·D33 M51 D20·D21 D34·D35 M52 When S1, S2 (source), and D1 (destination) are designated to repeat, double-word operands (as many as the repeat cycles, starting with the operands designated by S1 and S2) are compared with each other. The comparison results are set to oper- ands (as many as the repeat cycles, starting with the operand designated by D1). S1 (Repeat = 3) S2 (Repeat = 3) D1 (Repeat = 3) CMP2 S1 R S2 R D1 R REP D20·D21 D30·D31 M50 D20 D30 M50 3 I6 D22·D23 D32·D33 M51 D24·D25 D34·D35 M52 6-2 USER’S MANUAL 7: COMPUTER LINK Introduction 3 This chapter describes the computer link 1:N communication system for controlling multiple MICRO C units from a com- 3 puter. Unlike the computer link 1:N communication system for the MICRO , shielded twisted pair cables from the RS232C/ 3 RS485 converter can be connected to data link terminals on the MICRO C directly, without the need for the computer link 3 interface units and computer link interface cables. A computer can also communicate with a MICRO C network through 3 modems. For the MICRO C computer link 1:1 communication, see page 1-5. Computer Link 1:N Communication To set up a 1:N computer link system, connect a computer to RS232C/RS485 converter using RS232C cable HD9Z-C52. 3 Connect the RS232C/RS485 converter to MICRO C units using shielded twisted pair cables. Supply power to the RS232C/RS485 converter by connecting a 24V DC source to terminals 6 and 7 or by plugging an AC adapter to the DC IN jack. For speciŢcations of the AC adapter, see page 7-4. RS232C/RS485 Converter FC2A-MD1 132H × 110W × 34D mm POWER (5.917"H × 4.331"W × 1.339"D) SD RS485 RS232C/RS485 RD SERIAL PORT CONVERTER 1 Type FC2A-MD1 T 2 A 3 To RS232C Port B To RS232C Port 4 SG 5 FG 6 RS232C Cable + POWER SUPPLY D-sub 9-pin HD9Z-C52 7 24V DC D-sub 25-pin – Female 1.5m (4.92 ft.) long Male Connector DC IN Connector + – 24V DC or AC Adapter (9V DC, 350 mA) 1st Unit 2nd Unit Function selector switch: 0 Function selector switch: 0 Protocol selector switch: 2, 3, or 4 Protocol selector switch: 2, 3, or 4 FUN9: 0 FUN9: 1 ABSG ABSG Shielded twisted pair cable 200m (656 ft.) maximum Nth Unit (N≤32) 3rd Unit Function selector switch: 0 Function selector switch: 0 Protocol selector switch: 2, 3, or 4 Protocol selector switch: 2, 3, or 4 FUN9: N–1 FUN9: 2 ABSG ABSG 3 Select a unique device number, from 0 through 31, for each MICRO C using FUN9 PLC address for network communica- 3 tion on the program loader, and transfer the user program to the MICRO C. USER’S MANUAL 7-1 RS232C SERIAL PORT 7: COMPUTER LINK Computer Link 1:N Communication Using Modems A 1:N computer link system can also be controlled through modems using RS232C/RS485 converter FC2A-MD1. Connect a computer and the RS232C/RS485 converter to modems using RS232C straight cables. 3 Connect the RS232C/RS485 converter to MICRO C units using shielded twisted pair cables. Supply power to the RS232C/RS485 converter by connecting a 24V DC source to terminals 6 and 7 or by plugging an AC adapter to the DC IN jack. For speciŢcations of the AC adapter, see page 7-4. RS232C/RS485 Converter FC2A-MD1 132H × 110W × 34D mm POWER (5.917"H × 4.331"W × 1.339"D) SD RS485 RS232C/RS485 RD SERIAL PORT CONVERTER 1 Type FC2A-MD1 T 2 A 3 B Telephone Line 4 SG 5 Modem Modem FG RS232C RS232C 6 + POWER SUPPLY Straight Cable Straight Cable 7 24V DC – Note: When connecting a computer to RS232C/RS485 converter DC IN FC2A-MD1 directly, use RS232C cable HD9Z-C52. + – 24V DC or AC Adapter (9V DC, 350 mA) 1st Unit 2nd Unit Function selector switch: 0 Function selector switch: 0 Protocol selector switch: 2, 3, or 4 Protocol selector switch: 2, 3, or 4 FUN9: 0 FUN9: 1 3 3 MICRO C MICRO C ABSG ABSG Shielded twisted pair cable 200m (656 ft.) maximum 3 Nth Unit (N≤32) MICRO can also be connected to Function selector switch: 0 the computer link 1:N communica- FUN9: N–1 tion using RS232C/RS485 con- Computer Link Interface Unit A B SG FG verter FC2A-MD1 for modems. FC2A-LC1 3 For connecting the MICRO to the 69.5H × 55W × 35.5D mm network, use the computer link (2.736"H × 2.165"W × 1.398"D) interface unit and computer link interface cable. Computer Link Interface Cable 3 MICRO FC2A-KC3 100 mm (3.937") long 3 In the 1:N communication network, MICRO C cannot send the initialization string to the modem. The modem must be ini- tialized in advance using the following initialization string. This string is different from the default initialization string in 3 the MICRO C modem mode. Initialization String: ATE0V0X0\J1\N0\Q0&D0S0=2&W E0 Character NOT echoed V0 Digit result code X0 Disables dial tone and busy detection \J1 Set bps rate adjust on \N0 Normal mode – buffered – no error detection \Q0 Disables ţow control &D0 Ignore DTR signal S0=2 Answer on the second ring &W Write active proŢle into non-volatile memory 7-2 USER’S MANUAL RS232C SERIAL PORT 7: COMPUTER LINK RS232C/RS485 Converter FC2A-MD1 3 3 The RS232C/RS485 converter FC2A-MD1 is used with the MICRO C and the MICRO to convert data signals between EIA RS232C and EIA RS485. This converter makes it possible to connect a host device with RS232C interface to multiple 3 3 MICRO C and MICRO programmable controllers using one cable. RS485 RS232C Converter Signal Level Signal Level Parts Description Power Indicator Goes on when power is supplied POWER SD Transmit Data Indicator RS485 I/O RS485 RS232C/RS485 RD Goes on when RS232C transmit data (pin #2) is on SERIAL PORT CONVERTER 1 Termination Resistor Type FC2A-MD1 T Receive Data Indicator 2 Transmit/Receive Data A A Goes on when RS232C receive data (pin #3) is on 3 Transmit/Receive Data B B 4 Signal Ground SG RS232C I/O 5 Frame Ground FG Connect to the RS232C port on the computer 6 Vcc (+24V) + POWER SUPPLY 7 24V DC GND – DC IN AC Adapter Jack Connect AC adapter to supply 9V DC, 350mA Note: The FC2A-MD1 contains a 220Ω termination resistor on the RS485 line, eliminating the need for an external termi- nation resistor. To use the internal termination resistor, connect terminal T to terminal B. When the termination resistor is not needed, disconnect terminal T from terminal B. SpeciŢcations General SpeciŢcations Power terminals 24V DC ±20% (Ripple 10% maximum) Rated Power Voltage DC IN adapter jack 9V DC, 350mA supplied from AC adapter Current Draw Power terminals: Approx. 40 mA at the rated voltage Operating Temperature 0 to 60°C Storage Temperature –20 to +70°C Operating Humidity 45 to 85% RH (no condensation) 2 Vibration Resistance 5 to 55 Hz, 60 m/sec , 2 hours each in 3 axes 2 Shock Resistance 300 m/sec , 3 shocks each in 3 axes Dielectric Strength 1500V AC, 1 minute between live parts and dead parts Insulation Resistance 10 MΩ minimum between live parts and dead parts (500V DC megger) Noise Resistance Power terminals: ±1 kV, 1 µsec (using noise simulator) Weight Approx. 550g Serial Interface SpeciŢcations EIA standard RS232C (D-sub 25-pin female connector) Standards in Compliance EIA standard RS485 (screw terminals) Communication Method Half-duplex Communication ConŢguration 1:N (N ≤ 32) Communication Cable Shielded twisted-pair cable Communication Baud Rate 9600 bps (Ţxed) Slave Stations 32 slave stations maximum (RS485 line) RS232C: 15m (49.2 ft.) Maximum Cable Length RS485: Total 200m (656 ft.) USER’S MANUAL 7-3 RS232C SERIAL PORT 7: COMPUTER LINK RS232C Connector Pinouts Pin No. Description D-sub 25-pin Female Connector 13 1 1 GND Frame Ground 2 TXD Transmit Data 3 RXD Receive Data 4 (RTS) Unused 5 (CTS) Unused 25 14 6 (NC) Unused Note: Terminals 4 and 5 are connected together internally. 7 GND Signal Ground 8-25 (NC) Unused Dimensions Mounting Bracket Mounting Hole Layout 3.6 mm 10 mm (0.394") (0.142") 142 mm 132 mm (5.197") (5.591") Rubber Feet ş4.5 mm hole × 2 (0.177" dia.) 3.6 mm 10 mm (0.394") (0.142") 3.6 mm 3.6 mm 5 mm 110 mm (4.331") (0.142") (0.142") (0.197") D-sub 25-pin Connector AC Adapter Jack Note: When mounting the RS232C/RS485 converter on a panel surface, remove the rubber feet; then attach the supplied mounting brackets on the bottom of the 34 mm (1.339") 24.4 mm (0.961") converter using screws. 7 mm (0.276") RS232C Cable HD9Z-C52 Connector for RS232C/RS485 Converter Connector for Computer 1.5m (4.92 ft.) long Description Pin No. Pin No. Symbol GND Frame Ground 1 1 DCD TXD Transmit Data 2 2 RXD RXD Receive Data 3 3 TXD RTS Request to Send 4 4 DTR CTS Clear to Send 5 5 GND DSR Data Set Ready 6 6 DSR DCD Data Carrier Detect 8 7 RTS DTR Data Terminal Ready 20 8 CTS GND Signal Ground 7 9 RI D-sub 25-pin male connector D-sub 9-pin female connector AC Adapter 9.5 Polarity ş2.1 The RS232C/RS485 converter is powered by a 24V DC source or an AC adapter with 9V DC, 350mA output capacity. + – The output plug of the AC adapter is shown on the right. Dimensions in mm. 7-4 USER’S MANUAL ş5.5 8: SAMPLE PROGRAM – USER COMMUNICATION TXD Introduction This example demonstrates a program to send data to a printer using the user communication TXD (transmit) instruction. Serial printers used for this example are Seiko Electronic’s DPU-201GS and Citizen’s iDP3110 printers. System Setup Protocol Selector Switch 0 Set to 1 or 3 to select user protocol 7 1 6 2 for the loader port 5 3 Printer 4 User Communication Cable 1C FC2A-KP1C 2.4m (7.87 ft.) long To RS232C Port To Loader Port Attach a connector to the open end of the (RS232C) user communication cable 1C referring to the cable connector pinouts shown below. Cable Connection for Seiko Electronic’s DPU-201GS Mini DIN Connector Pinouts D-sub 9-pin Connector Pinouts Description Color Pin Pin Description Shield — Cover 1 NC No Connection NC No Connection Black 1 2 NC No Connection NC No Connection Yellow 2 3 DATA Receive Data TXD Transmit Data Blue 3 4 NC No Connection NC No Connection Green 4 5 GND Ground DSR Data Set Ready Brown 5 6 NC No Connection SG Signal Ground Gray 6 7 NC No Connection SG Signal Ground Red 7 8 BUSY Busy signal NC No Connection White 8 9 NC No Connection The name of BUSY terminal differs depending on printers, such as DTR. The function of this terminal is to send a signal to remote equipment whether the printer is ready to print data or not. Since the operation of this signal may differ depend- ing on printers, conŢrm the operation before connecting the cable. 3 Do not connect any wiring to the NC (No Connection) pins; otherwise, the MICRO C and the printer Caution may not work correctly and may be damaged. Description of Operation Printout Example The data of counter C2 and data register D30 are printed every minute. A printout example is shown on the right. --- PRINT TEST -- - Programming Expansion Control Data Registers 11H 00M Expansion control data register D490 is used to monitor the BUSY signal and to con- trol the transmission of print data. CNT2...0050 D030...3854 Expansion Control Value Description DR --- PRINT TEST -- Enables expansion control data registers D486 - D499 4 through D491 for control signals. 3 11H 01M While DSR is on (not busy), MICRO C sends data. 3 While DSR is off (busy), MICRO C stops data CNT2...0110 transmission. D490 3 If the off duration exceeds a limit (approx. 5 sec), a transmission busy timeout error will occur, and the transmit status data register stores 22h. See pages 5-5 and 11-2. 3 MICRO C monitors the DSR signal to prevent the receive buffer of the printer from overţowing. For the DSR signal, see USER’S MANUAL 8-1 8: SAMPLE PROGRAM – USER COMMUNICATION TXD Setting Communication Parameters Set the FUN8 loader port communication parameters to match those of the printer. For details of the communication parameters of the printer, see the user’s manual for the printer. Communication Parameters: Terminator Code Baud Rate Baud rate 9600 bps FUN 8 COM-FORM (Note 1) Data bits 8 * 9600bps *0D Parity check None Data Bits Stop Bit *8bit*NON *stop1 Stop bit 1 (:I___ : 500ms) Note 1: In the user communication mode, com- munication is based on the end delimiter code Mode Selection Input Parity Receive Timeout (Note 3) Check (Note 2) speciŢed in the TXD or RXD instruction. Note 2: The receive timeout value is used for the RXD instruction in the user communication mode. Since this example uses only the TXD instruction, the receive timeout value has no effect. Note 3: When the protocol selector switch is set to 1 or 3 to select user protocol for the loader port, the mode selection input is not used and need not be speciŢed to enable the FUN8 values. Ladder Diagram The CLKR (clock read) instruction is used to read the hour, minute, and second data to three data registers. The second data is compared with 0 using the CMP= (compare equal to) instruction. Each time the condition is met, the TXD instruc- tion is executed to send the C2 and D30 data to the printer. A counting circuit for counter C2 is omitted from this sample program. M301 is the initialize pulse special internal relay. MOV S1 D1 REP 3 D490 M301 ** 3 → D490 to enable the DSR option for busy control. MOV S1 D1 REP 4 → D499 to enable expansion control data register service 4 D499 ** for D486 through D491. CLKR M317 is the in-operation output special internal relay. D20 M317 CLKR sets hour, minute, and second data to D20 through CMP= S1 S2 D1 REP D22. D22 0 M0 ** CMP= compares the D22 second data with 0. MOV S1 D1 REP C2 D31 Counter C2 data is moved to D31. ** When the D22 data equals to 0 second, TXD is executed to TXD S1 D1 D2 SOTU 73 M1 D0 send 73-byte data through the loader port to the printer. M0 SP SP SP – – – SP P R I N T SP T 20h 20h 20h 2Dh 2Dh 2Dh 20h 50h 52h 49h 4Eh 54h 20h 54h E S T SP – – – CR LF CR LF SP SP SP 45h 53h 54h 20h 2Dh 2Dh 2Dh 0Dh 0Ah 0Dh 0Ah 20h 20h 20h D20 hour data is converted into binary→BCD→ASCII, D20 Conversion: BCD→ASCII Digits: 2 REP: 01 and 2 digits are sent. H SP 48h 20h D21 minute data is converted into binary→BCD→ASCII, D21 Conversion: BCD→ASCII Digits: 2 REP: 01 and 2 digits are sent. M CR LF CR LF 4Dh 0Dh 0Ah 0Dh 0Ah SP SP SP C N T 2 . . . 20h 20h 20h 43h 4Eh 54h 32h 2Eh 2Eh 2Eh D31 counter C2 data is converted into binary→BCD→ D31 Conversion: BCD→ASCII Digits: 4 REP: 01 ASCII, and 4 digits are sent. CR LF SP SP SP D 0 3 0 . . . 0Dh 0Ah 20h 20h 20h 44h 30h 33h 30h 2Eh 2Eh 2Eh D30 data is converted into binary→BCD→ASCII, and 4 D30 Conversion: BCD→ASCII Digits: 4 REP: 01 digits are sent. CR LF CR LF 0Dh 0Ah 0Dh 0Ah END 8-2 USER’S MANUAL 9: SAMPLE PROGRAM – USER COMMUNICATION TXD & RXD Introduction This example demonstrates a program of the user communication TXD and RXD instructions to read and write data regis- 3 ters. When the computer sends a message to read data from data registers using a BASIC program, the MICRO C sends back data from predetermined data registers to the computer using the TXD instruction. When the computer sends a mes- 3 sage to write data to data registers and new data register values, the MICRO C stores the new values to predetermined data registers using the RXD instruction and returns an acknowledge reply to the computer using the TXD instruction. System Setup Protocol Selector Switch 0 Set to 1 or 3 to select user protocol 7 1 6 2 for the loader port 5 3 4 Computer Link Cable 4C To RS232C Port FC2A-KC4C 3m (9.84 ft.) long To Loader Port (RS232C) D-sub 9-pin Female Connector Mini DIN Connector Pinouts D-sub 9-pin Connector Pinouts Description Color Pin Pin Description Shield — Cover Cover Shield RTS Request to Send Black 1 1 DCD Data Carrier Detect DTR Data Terminal Ready Yellow 2 2 RXD Receive Data TXD Transmit Data Blue 3 3 TXD Transmit Data RXD Receive Data Green 4 4 DTR Data Terminal Ready DSR Data Set Ready Brown 5 5 GND Signal Ground SG Signal Ground Gray 6 6 DSR Data Set Ready SG Signal Ground Red 7 7 —— NC No Connection White 8 8 CTS Clear to Send 9 —— 3 Do not connect any wiring to the NC (No Connection) pin; otherwise, the MICRO C and the com- Caution puter may not work correctly and may be damaged. Description of Operation 3 In this example, the computer uses a BASIC program to send request messages to the MICRO C, to receive data from the 3 3 MICRO C, and to display the received data on the screen. The MICRO C uses TXD and RXD instructions to transmit and receive user communications, and does not use the RTS, DSR, and DTR control signals. Communication data between the 3 computer and the MICRO C are shown below. Monitoring Data Registers D50 and D51 If data registers D50 and D51 store 1234 and 5678 before monitoring, the data shown below are communicated. 3 Computer MICRO C Request “R” CR ACK “1” “2” “3” “4” “5” “6” “7” “8” CR (52h) (0Dh) (06h) D50 monitor data (4 bytes) D51 monitor data (4 bytes) (0Dh) Reply Writing Data to Data Registers D50 and D51 If 3333 and 5555 are written to data registers D50 and D51, the data shown below are communicated. 3 Computer MICRO C Request “W” “3” “3” “3” “3” “5” “5” “5” “5” CR ACK “O” “K” CR (57h) (0Dh) (06h) (4Fh) (4Bh) (0Dh) D50 write data (4 bytes) D51 write data (4 bytes) Reply USER’S MANUAL 9-1 9: SAMPLE PROGRAM – USER COMMUNICATION TXD & RXD Setting Communication Parameters Set the FUN8 loader port communication parameters to the default values. Communication Parameters: Terminator Code Baud Rate Baud rate 9600 bps FUN 8 COM-FORM (Note 1) Data bits 7 * 9600bps *0D Parity check Even Data Bits Stop Bit *7bit*EVEN*stop1 Stop bit 1 (:I___ : 500ms) Note 1: In the user communication mode, com- munication is based on the end delimiter code Mode Selection Input Parity Receive Timeout (Note 3) Check (Note 2) speciŢed in the TXD or RXD instruction. Note 2: The receive timeout value is used for the RXD instruction in the user communication mode. When the interval between characters in the receive data exceeds 500 msec, receive timeout occurs and the RXD instruction is aborted. Note 3: When the protocol selector switch is set to 1 or 3 to select user protocol for the loader port, the mode selection input is not used and need not be speciŢed to enable the FUN8 values. BASIC Program Display Example The following example shows a screen display when data registers D50 and D51 store values 1234 and 5678 before moni- toring and when the data changes to 3333 and 5555, respectively. When the BASIC program shown on the next page is loaded and run, the screen shows the following message. Type R to read from or W to write to D50 & D51: _ If you type R and press the Enter key to read the data from data registers D50 and D51, the read data are displayed. Type R to read from or W to write to D50 & D51: R D50 value: 1234 D51 value: 5678 Type C to continue or Q to quit: _ Type C and press the Enter key to continue. Then type W and press the Enter key to write data. Enter the new value 3333 for D50 and press the Enter key, followed by the new value 5555 for D51 and the Enter key. Type R to read from or W to write to D50 & D51: R D50 value: 1234 D51 value: 5678 Type C to continue or Q to quit: C Type R to read from or W to write to D50 & D51: W Enter D50 value: 3333 Enter D51 value: 5555 OK Type C to continue or Q to quit: _ To quite the program, type Q and press the Enter key. Type C to continue or Q to quit: Q Ok 9-2 USER’S MANUAL 9: SAMPLE PROGRAM – USER COMMUNICATION TXD & RXD BASIC Program 1000 'SAVE "MONWRITE.BAS",A 1010 '+--------------------------------------+ 1020 '| | 1030 '| Monitor Data Registers D50 & D51 | 1040 '| Write to Data Registers D50 & D51 | 1050 '| | 1060 '+--------------------------------------+ 1070 CLS 1080 '-----------------------------------[Open Communication Line] 1090 OPEN "COM1:9600,E,7,1" AS #1 'Even parity, 7 data bits, 1 stop bit 1100 '-----------------------------------[Set Transmit Data] 1110 CR$=CHR$(13) 'End delimiter code (CR) 1120 TXD1$="R"+CR$ 'Monitor command 1130 '-----------------------------------[Select Transmit Command] 1140 INPUT "Type R to read from or W to write to D50 & D51: ",A$ 1150 IF A$="R" THEN GOTO 1190 1160 IF A$="W" THEN GOTO 1240 1170 BEEP: GOTO 1140 1180 '-----------------------------------[Transmit/receive monitor command] 1190 PRINT #1,TXD1$; 'Transmit monitor command 1200 RXD$=INPUT$(10,#1) 'Receive reply message 1210 PRINT "D50 value: "+MID$(RXD$,2,4) 'Display D50 value 1220 PRINT "D51 value: "+MID$(RXD$,6,5) 'Display D51 value 1230 GOTO 1360 1240 '-----------------------------------[Transmit/receive write command] 1250 WDAT$="" 'Clear write data buffer 1260 INPUT "Enter D50 value: ",WDAT$ 'Enter new value for D50 1270 TXD2$="W"+WDAT$ 'Define write command 1 1280 WDAT$="" 'Clear write data buffer 1290 INPUT "Enter D51 value: ",WDAT$ 'Enter new value for D51 1300 TXD2$=TXD2$+WDAT$+CR$ 'Define write command 2 1310 PRINT #1,TXD2$; 'Transmit write command 1320 RXD$=INPUT$(4,#1) 'Receive reply message 1330 PRINT MID$(RXD$,2,3) 'Display receive data 1340 GOTO 1360 'To Select Transmit Command 1350 '-----------------------------------[Continue or quit program] 1360 INPUT "Type C to continue or Q to quit: ",B$ 1370 PRINT 1380 IF B$="C" THEN GOTO 1130 1390 IF B$="Q" THEN CLOSE #1: END 1400 BEEP: GOTO 1360 USER’S MANUAL 9-3 9: SAMPLE PROGRAM – USER COMMUNICATION TXD & RXD Ladder Diagram 3 When the MICRO C is started, M301 is turned on to execute a MOV instruction and 0 is set to data register D499 to disable the expansion control data register service. When expansion control data registers are not required, programming to set 0 to D499 is recommended to make sure that the modem communication mode is not enabled unexpectedly. M301 is the initialize pulse special internal relay. MOV S1 D1 REP 0 D499 M301 ** 0 → D499 to disable expansion control data register service. RXD S1 D1 D2 2 M0 D0 RXD Data 1 (see below) M301 RXD S1 D1 D2 SOTU RXD Data 2 (see below) 10 M1 D2 M2 When M301, transmit completion output M2 or M3 is turned on, RST RXD instructions are executed to wait for incoming communica- M3 M2 tion. When RXD is complete, receive completion output M0 or RST M1 is turned on to execute a corresponding TXD. M3 TXD S1 D1 D2 TXD Data 1 (see below) 10 M2 D4 M0 When TXD is complete, transmit completion output M2 is turned RST on to execute RXD instructions. M0 TXD S1 D1 D2 TXD Data 2 (see below) 4 M3 D6 M1 When TXD is complete, transmit completion output M3 is turned RST on to execute RXD instructions. M1 END RXD Data 1 “R” CR (52h) (0Dh) End Delimiter Start Delimiter RXD Data 2 “W” D50 B4 2 CR (57h) (0Dh) Data Register End Delimiter D50, ASCII→BCD→Binary Conversion (4 digits), Repeat: 2 Start Delimiter TXD Data 1 ACK D50 B4 2 CR (06h) Data Register (0Dh) End Delimiter D50, Binary→BCD→ASCII Conversion (4 digits), Repeat: 2 Start Delimiter TXD Data 2 ACK “O” “K” CR (06h) (4Fh) (4Bh) (0Dh) End Delimiter Reply Message “OK” Start Delimiter 9-4 USER’S MANUAL 10: SAMPLE PROGRAM – MODEM COMMUNICATION Introduction 3 This example is an automatic monitor system using the MICRO C’s modem mode. Both modems at the local and remote 3 stations are initialized by the MICRO C. When the internal clock reaches 0 minutes and 0 seconds at every hour, the 3 3 MICRO C at the remote station dials the telephone number and sends the status of input I1 to the MICRO C at the local sta- 3 tion using the user communication TXD instruction. The MICRO C at the local station turns output Q0 or Q1 on, depending on the incoming communication whether input I1 is on or off at the remote station. Modem communication can also be started by turning input I0 on at the remote station to send the input I1 status at any time. System Setup 3 To connect a modem to the loader port on the MICRO C at both the local and remote stations, use the modem cable 1C (FC2A-KM1C). To enable the modem mode, make the three settings described below: 1. Set the protocol selector switch to 1 or 3 to select user protocol for the loader port. (See page 1-2.) After changing the 3 protocol selector switch setting while the MICRO C is powered up, press the communication enable button to enable the new communication mode. 2. Enter 6 (7, 14, or 15) to data register D499 to enable expansion control register service for D486 through D495. (See page 2-5.) 3. Enter 1 to data register D495 to enable the modem mode. (See page 2-5.) Protocol Selector Switch Sensor 0 7 1 Set to 1 or 3 to select user protocol 6 2 Switch 5 3 4 I0 I1 for the loader port Modem Modem Telephone Line Q0 Q0 Q1 Communication Enable Button Press to enable the new communication mode NG Error Indicator A B after changing the protocol selector switch Remote Station Local Station Modem Cable 1C Mini DIN Connector Pinouts FC2A-KM1C D-sub 25-pin Connector Pinouts 3m (9.84 ft.) long Description Color Pin Pin Description Shield — Cover 1 FG Frame Ground RTS Request to Send Black 1 2 TXD Transmit Data DTR Data Terminal Ready Yellow 2 3 RXD Receive Data TXD Transmit Data Blue 3 4 RTS Request to Send RXD Receive Data Green 4 5 —— DSR Data Set Ready Brown 5 6 —— SG Signal Ground Gray 6 7 SG Signal Ground SG Signal Ground Red 7 8 DCD Data Carrier Detect NC No Connection White 8 20 DTR Data Terminal Ready 3 Do not connect the NC (No Connection) pin to any line; otherwise, the MICRO C may be damaged. Caution 3 Modem cables for Apple Macintosh computers cannot be used for the MICRO C. USER’S MANUAL 10-1 10: SAMPLE PROGRAM – MODEM COMMUNICATION Allocation Numbers (Remote Station) Allocation Number Description I0 Input from a switch to start modem communication manually to send the I1 status I1 Input from a sensor to start modem communication every hour to send the I1 status Q0 Error output which goes on when retry countout, initialization string or ATZ failure occurs M0 Goes on at 0 minutes M1 Goes on at 0 seconds M2 Start transmission internal relay M3 Start/retry transmission internal relay M4 Retry interval internal relay M11 Transmit completion output for transmitting A to indicate input I1 on M12 Transmit completion output for transmitting B to indicate input I1 off M13 Receive completion output for receiving C to start disconnecting the telephone line M260 Start initialization string internal relay for the originate mode M263 Start disconnect line internal relay M273 Disconnect line completion internal relay M280 Initialization string failure internal relay M281 ATZ failure internal relay M282 Dialing failure internal relay M287 Telephone line connection status internal relay (ON: Connected, OFF: Disconnected) M301 Initialize pulse special internal relay M317 In-operation output special internal relay D1 Hour data – destination of CLKR (clock read) instruction D2 Minute data – destination of CLKR (clock read) instruction D3 Second data – destination of CLKR (clock read) instruction D11 Transmit status data register for TXD instruction to send A D12 Transmit data byte count data register for TXD instruction to send A D13 Transmit status data register for TXD instruction to send B D14 Transmit data byte count data register for TXD instruction to send B D15 Receive status data register for RXD instruction to receive C D16 Receive data byte count data register for RXD instruction to receive C D100 Retry cycle data register (Retry cycle = 0) D101 Modify initialization string data register (0 speciŢes \Q3 for AIWA’s modems) D160 Telephone number “T2” = 54 32h = 21554 D161 Telephone number “34” = 33 34h = 13108 D162 Telephone number “56” = 35 36h = 13622 D163 Telephone number “78” = 37 38h = 14136 D164 Telephone number end delimiter code CR = 0D 00h = 3328 D492 On-line mode protocol (1 speciŢes user protocol after telephone line is connected) D495 Modem mode selection (1 enables the modem mode) D499 Expansion control data register service selection (6 enables D486 through D495) T0 10-sec delay timer before transmitting A or B representing input I1 status T3 60-sec delay timer before retrying to send the initialization string C2 Retry counter to count the retry cycles of 2 10-2 USER’S MANUAL 10: SAMPLE PROGRAM – MODEM COMMUNICATION Allocation Numbers (Local Station) Allocation Number Description Q0 Goes on when receiving A indicating input I1 on at the remote station Q1 Goes on when receiving B indicating input I1 off at the remote station M0 Receive completion output for receiving A to indicate input I1 on at the remote station M1 Receive completion output for receiving B to indicate input I1 off at the remote station M2 Transmit completion output for transmitting C to start disconnecting the telephone line M265 Start initialization string internal relay for the answer mode M287 Telephone line connection status internal relay (ON: Connected, OFF: Disconnected) M301 Initialize pulse special internal relay M317 In-operation output special internal relay D0 Receive status data register for RXD instruction to receive A D1 Receive data byte count data register for RXD instruction to receive A D2 Receive status data register for RXD instruction to receive B D3 Receive data byte count data register for RXD instruction to receive B D4 Transmit status data register for TXD instruction to send C D5 Transmit data byte count data register for TXD instruction to send C D101 Modify initialization string data register (0 speciŢes \Q3 for AIWA’s modems) D492 On-line mode protocol (1 speciŢes user protocol after telephone line is connected) D495 Modem mode selection (1 enables the modem mode) D499 Expansion control data register service selection (6 enables D486 through D495) T0 1-sec delay timer before transmitting the initialization string T2 5-sec delay timer before executing the RXD instructions after telephone line connection Description of Operation Remote Station 3 When the MICRO C is powered up, the MOV instructions are executed by initialize pulse M301 to store values to data reg- isters which enable the modem mode. The telephone number is also stored to data registers. 3 At 0 minutes and 0 seconds every hour, the MICRO C at the remote station sends the initialization string to the modem and dials the telephone number 234-5678. If the modem initialization or ATZ fails, output Q0 is turned on to indicate an error. When dialing fails, two more attempts will be made. When the retry fails, output Q0 is turned on to signal that the tele- phone line connection failed. CR Ten seconds after the telephone line is connected, the status of input I1 is sent to the local station. When I1 is on, A is sent. When I1 is off, B CR is sent. The status of input I1 can also be sent any time by turning input I0 on. 3 When receiving C CR from the local station, the MICRO C at the remote station disconnects the telephone line. Local Station 3 When the MICRO C is powered up, the MOV instructions are executed by initialize pulse M301 to store values to data reg- isters which enable the modem mode. 3 One second later, the MICRO C at the local station sends the initialization string to the modem. Five seconds after the telephone line is connected, the RXD instructions are executed to wait for incoming communica- tion. When receiving A CR , output Q0 is turned on and output Q1 is turned off. When receiving B CR , output Q0 is turned off and output Q1 is turned on. 3 When receiving is complete, the MICRO C at the local station sends C CR to reply to the remote station. USER’S MANUAL 10-3 10: SAMPLE PROGRAM – MODEM COMMUNICATION Ladder Diagram (Remote Station) In-operation M317 is the in-operation output special internal relay. CLKR D1 M317 CLKR (clock read) stores the hour, minute, and second data to D1, D2, and D3, respectively. CMP= S1 S2 D1 REP D2 0 M0 ** When D2 (minute) equals 0, M0 is turned on. CMP= S1 S2 D1 REP When D3 (second) equals 0, M1 is turned on. D3 0 M1 ** 0 min 0 sec Error Line Connected Start Transmission At 0 minutes and 0 seconds every hour, transmission is started. M0 M1 Q0 M287 M2 Start Transmission When manual start input I0 is turned on, transmission is started. M2 Manual Start I0 Retry Timer Error Line Connected Start/Retry Trans. When retry timer T3 times out, T3 output goes on and off; M2 T3 Q0 M287 M3 then start/retry transmission M3 is turned on again. M3 Retry Counter Reset When start transmission M2 or manual start I0 is turned on, SOTU the retry counter is reset. M2 C2 Retry counter C2 counts the pulse inputs from retry timer 2 T3. I0 Retry Timer Pulse When T3 times out 2 cycles, C2 counts out. T3 Retry Counter Error SET C2 Q0 When retry counter C2 counts out, initialization string fail- ure M280 is turned on, or ATZ failure M281 is turned on, Initialization String Failure M280 then error output Q0 is set to on. ATZ Failure M281 Start/Retry Transmission Start Initialization String When start/retry transmission M3 is turned on, M260 is turned on to send the initialization string to the modem. M3 M260 Dialing Failure Retry Interval When the initialization string and ATZ are completed but dialing has failed, M4 is turned on to start retry timer T3. M280 M281 M282 T3 M4 Retry Timer 60 sec When T3 times out 60 sec, M4 is turned off and T3 is reset, T3 600 turning M3 on and off to retry initialization string M260. M4 Line Connected Transmission Delay Timer 10 sec When the telephone line is connected, M287 is turned on T0 100 and timer T0 starts to time down before user communica- M287 tion is started. TXD S1 D1 D2 SOTU 2 M11 D11 T0 I1 When timer T0 times out 10 sec, TXD is executed. TXD Data “A” CR When input I1 is on, A CR is transmitted. (41h) (0Dh) When transmission is complete, transmit completion M11 is turned on. TXD S1 D1 D2 2 M12 D13 I1 When input I1 is off, B CR is transmitted. TXD Data When transmission is complete, transmit completion M12 “B” CR (42h) (0Dh) is turned on. 10-4 USER’S MANUAL 10: SAMPLE PROGRAM – MODEM COMMUNICATION Ladder Diagram (Remote Station), continued Transmit A Complete When A or B is transmitted successfully, RXD is executed RXD S1 D1 D2 2 M13 D15 to wait for incoming data C CR . M11 RXD Data When receiving is complete, receive completion M13 is “C” CR (43h) (0Dh) turned on. Transmit B Complete RST M12 M11 RST M12 Receive C Complete Start Disconnect Line When C CR is received successfully, M13 turns M263 on to disconnect the telephone line. M13 M263 Disconnect Line Complete RST M273 M13 Initialize Pulse 6 → D499 to enable the expansion control data register ser- MOV S1 D1 REP 6 D499 vice for D486 through D495. M301 ** MOV S1 D1 REP 1 → D495 to enable the modem mode. 1 D495 ** MOV S1 D1 REP 1 → D492 to select user protocol for the loader port after 1 D492 ** telephone line is connected. MOV S1 D1 REP 0 → D101 to select \Q3 in the initialization string for 0 D101 ** AIWA’s modems. MOV S1 D1 REP 0 → D100 to select no retry in the modem mode. SOTD 0 D100 ** In this example, retry cycles are programmed using timer and counter. See Note below. MOV S1 D1 REP 21554 D160 ** D160 through D164 store touch-tone modiŢer T, telephone MOV S1 D1 REP 13108 D161 number 234-5678, and an end delimiter. ** MOV S1 D1 REP D160 21554 54 32h = “T2” 13622 D162 ** 13108 33 34h = “34” D161 MOV S1 D1 REP 13622 35 36h = “56” D162 14136 D163 ** 14136 37 38h = “78” D163 MOV S1 D1 REP D164 3328 0D 00h = “0” CR 3328 D164 ** END Note: At the END processing in the Ţrst scan when the modem mode is enabled, default values are set to data registers used for the modem mode; D100 stores the default retry cycles of 3 and D135 through D159 store the default initialization string. These values can be changed in a subsequent scan. In this sample program, SOTD (single output down) is used to replace the D100 default value with 0. USER’S MANUAL 10-5 10: SAMPLE PROGRAM – MODEM COMMUNICATION Ladder Diagram (Local Station) In-operation 3 When MICRO C is started, M317 is turned on to start timer T0 10 T0 for 1-sec time delay to enable the modem mode before M317 1 sec Start Initialization String sending the initialization string. When timer T0 times out, M265 is turned on to send the T0 M265 Line Connected initialization string to the modem. T2 50 When the telephone line is connected, M287 is turned on M287 5 sec and timer T2 starts to time down before user communica- RXD S1 D1 D2 SOTU tion is started. 2 M0 D0 M287 T2 When timer T2 times out 5 sec, RXD is executed to wait for RXD Data “A” CR incoming communication. (41h) (0Dh) When A CR is received, receive completion M0 is turned on. RXD S1 D1 D2 2 M1 D2 When B CR is received, receive completion M1 is turned on. RXD Data “B” CR (42h) (0Dh) When M0 is turned on, output Q0 is turned on and output Receive A Complete Q1 is turned off. SET M0 Q0 RST Q1 When M1 is turned on, output Q0 is turned off and output Receive B Complete Q1 is turned on. RST M1 Q0 SET When receiving is complete and M0 or M1 is turned on, Q1 TXD is executed to send C CR . TXD S1 D1 D2 SOTU 2 M2 D4 M0 TXD Data “C” CR (43h) (0Dh) M1 When transmission is complete, transmit completion M2 is Transmit C Complete Receive A Complete turned on; then M0, M1, and M2 are reset. RST M2 M0 Receive B Complete RST M1 Transmit C Complete 6 → D499 to enable the expansion control data register ser- RST M2 vice for D486 through D495. Initialize Pulse MOV S1 D1 REP 1 → D495 to enable the modem mode. 6 D499 M301 ** MOV S1 D1 REP 1 → D492 to select user protocol for the loader port after 1 D495 ** telephone line is connected. MOV S1 D1 REP 0 → D101 to select \Q3 in the initialization string for 1 D492 ** AIWA’s modems. MOV S1 D1 REP 0 D101 ** END 10-6 USER’S MANUAL 11: TROUBLESHOOTING Introduction This chapter describes the procedures to determine the cause of trouble and actions to be taken when any trouble occurs 3 while operating the MICRO C programmable controller. For descriptions about error indicators ERR1 and ERR2, reading error data using FUN20, and general error codes, see the 3 MICRO User’s Manual. 3 3 In addition to error information for the MICRO , the MICRO C has two extra functions for detecting errors: • Additional causes for type codes 5 and 6 in the user program syntax error • User communication error codes Error Causes and Actions 80h: User Program Syntax Error (Syntax) This error indicates that the user program has a syntax error or that FUN1 through FUN10 is set incorrectly. Correct the 3 user program or FUN settings, and transfer the corrected user program to the MICRO C. The error code is cleared when a correct user program is transferred. When this error occurs, the error message is displayed with a type code and an address code of 7 digits total. FUN 20 ERROR 80 Error Code Syntax0060026 Error Message Address Code Type Code User Program Syntax Error Type Code and Address Code Type Code Address Code Error Details 0001 Stop input number selection error (FUN1) 0002 Reset input number selection error (FUN2) 0003 Internal relay “keep” designation error (FUN3) 0004 Shift register “keep” designation error (FUN4) 0005 Processing mode selection error (FUN5) 1 0006 Catch input edge selection error (FUN6) 0007 Input Ţlter time selection error (FUN7) 0008 Loader port communication mode setting error (FUN8) 0009 PLC address error for network communication (FUN9) 0010 Control data register setting error (FUN10) 2 Invalid opcode for basic instruction 3 Invalid operand for basic instruction 4 Invalid timer/counter preset value 0000 to 1012 Invalid opcode for advanced instruction 5 (Note) Address of the incorrect TXD/RXD programmed in the high-speed processing mode program Invalid data for advanced instruction 6 (Note) Same data register designated as status DR for TXD and RXD 7 (Note) Invalid repeated usage of advanced instruction 8 User program capacity over error Note: When type code 5, 6, or 7 is displayed, the details are shown by the error code of the ADV Error (advanced instruc- 3 tion syntax error). See page 18-5 in the MICRO User’s Manual. USER’S MANUAL 11-1 11: TROUBLESHOOTING User Communication Error When a user communication error occurs, a user communication error code is stored in the data register designated as a transmit status in the TXD instruction or as a receive status in the RXD instruction. When multiple errors occur, the Ţnal error code overwrites all preceding errors and is stored in the status data register. To correct the error, correct the user program by referring to the error causes described below: User Communication Error Code User Communication Error Cause Transmit/Receive Completion Output Error Code Transmit completion outputs of the Ţrst 5 TXD Start inputs to more than 5 TXD instructions are 1 instructions from the top of the ladder diagram on simultaneously. are turned on. 2 Transmission destination busy timeout Goes on after busy timeout. Among the Ţrst 5 RXD instructions from the top Start inputs to more than 5 RXD instructions with of the ladder diagram, receive completion out- 3 a start delimiter are on simultaneously. puts of RXD instructions go on if the start delim- iter matches the Ţrst byte of the received data. While an RXD instruction without a start delimiter The receive completion output of the RXD instruc- 4 is executed, another RXD instruction with or with- tion at a smaller address goes on. out a start delimiter is executed. 5 Reserved — 6 Reserved — No effect on the receive completion output. The Ţrst byte of received data does not match If incoming data with a matching start delimiter 7 the speciŢed start delimiter. is received subsequently, the receive completion output goes on. When ASCII→binary or ASCII→BCD→binary con- version is speciŢed in the receive format, any 8 code other than 0 to 9 and A to F is received. The receive completion output goes on. (These codes are regarded as 0 during conver- sion.) BCC calculated from the RXD instruction does 9 not match the BCC appended to the received The receive completion output goes on. data. The end delimiter code speciŢed in the RXD A instruction does not match the received end The receive completion output goes on. delimiter code. Receive timeout between characters (After receiving one byte of data, the next byte is B The receive completion output goes on. not received in the period speciŢed for the receive timeout value in FUN8.) Overrun error C (Before the receive processing is completed, the The receive completion output goes on. next data is received.) Framing error D No effect on the completion output. (Detection error of start bit or stop bit) Parity check error E No effect on the completion output. (Error is found in the parity check.) TXD or RXD instruction is executed while the pro- F tocol selector switch is set to select loader proto- No effect on the completion output. col for the loader port. 11-2 USER’S MANUAL 11: TROUBLESHOOTING Troubleshooting Diagrams 3 When one of the following problems is encountered, see the troubleshooting diagrams described in the MICRO User’s Manual or on the following pages in this manual. Problem Troubleshooting Diagram See Manual 3 The POW (power) indicator does not go on. Diagram 1 MICRO User’s Manual 3 The RUN indicator does not go on. Diagram 2 MICRO User’s Manual 3 Error indicator ERR1 is on. Diagram 3 MICRO User’s Manual 3 Error indicator ERR2 is on. Diagram 4 MICRO User’s Manual 3 Inputs do not operate normally. Diagram 5 MICRO User’s Manual 3 Outputs do not operate normally. Diagram 6 MICRO User’s Manual Communication between the program loader and the Diagrams 7-1 through 7-3 This manual 3 MICRO C base unit is not possible. 3 Stop and reset operation cannot be performed. Diagram 8 MICRO User’s Manual 3 Normal voltage does not appear on sensor power terminals. Diagram 9 MICRO User’s Manual Expansion link or data link is impossible. Diagram 10 This manual Output pulses are not generated at output Q0 when using the 3 Diagram 11 MICRO User’s Manual PULS or PWM instruction. 3 High-speed counter does not work correctly. Diagram 12 MICRO User’s Manual 3 The catch input function cannot receive short pulses. Diagram 13 MICRO User’s Manual 3 The calendar/clock does not operate correctly. Diagram 14 MICRO User’s Manual 3 Transfer to and from the memory card is impossible. Diagram 15 MICRO User’s Manual Data is not communicated in the user communication mode. Diagrams 16-1 through 16-4 This manual USER’S MANUAL 11-3 11: TROUBLESHOOTING Troubleshooting Diagram 7-1 Communication between the program loader and 3 the MICRO C base unit (loader port) is not possible. Set the protocol selector switch to NO Is the protocol selector 0, 2, or 4 to select loader protocol switch set to 0, 2, or 4? for the loader port. YES Did you press the NO communication enable button for 4 sec? YES Did you power Press the communication enable NO down and up after changing button for more than 4 sec until the protocol selector the ERR1 indicator blinks once. switch? YES NO Is the loader cable 3C Connect the cable completely. connected correctly? YES See Troubleshooting Diagram 1, NO “The POW (power) indicator does Is the POW (power) 3 indicator on? not go on.” in the MICRO User’s Manual. YES Is FUN8 Loader Port NO Set the loader port communication Communication Mode mode to default. set to default? YES Call IDEC for assistance. 11-4 USER’S MANUAL 11: TROUBLESHOOTING Troubleshooting Diagram 7-2 Communication between the program loader and the 3 MICRO C base unit (data link terminals) is not possible. Set the protocol selector switch to NO Is the protocol selector 2, 3, or 4 to select loader protocol switch set to 2, 3, or 4? for the data link terminals. YES Did you press the NO communication enable button for 4 sec? YES Did you power Press the communication enable NO down and up after changing button for more than 4 sec until the protocol selector the ERR1 indicator blinks once. switch? YES NO Is the loader cable 4C Connect the wires of the cable to connected correctly? terminals A, B, and SG correctly. YES See Troubleshooting Diagram 1, NO “The POW (power) indicator does Is the POW (power) 3 indicator on? not go on.” in the MICRO User’s Manual. YES Call IDEC for assistance. Troubleshooting Diagram 7-3 When only program transfer is not possible: (both the loader port and data link terminals) Only program transfer is not possible. Cancel the program protection using the program loader. Is “Protected PC” YES displayed on the program FUN, 22, , , Pass Word, loader? 3 For details, see the MICRO User’s Manual. NO Call IDEC for assistance. USER’S MANUAL 11-5 11: TROUBLESHOOTING Troubleshooting Diagram 10 Expansion link or data link is impossible. Set the protocol selector switch to 0 or 1 to NO Is the protocol selector select data link protocol for the data link switch set to 0 or 1? terminals. YES Did you press the NO communication enable button for 4 sec? YES Did you power Press the communication enable button for NO down and up after changing more than 4 sec until the ERR1 indicator the protocol selector blinks once. switch? YES Is M306 on at the base station (expansion link) or master FUN20: PLC error data readout and reset NO station (data link)? FUN27: Link formatting sequence YES M306: Link communication prohibit ţag special internal relay M307: Link communication initialize ţag special internal relay Turn M306 off using the program loader. MON, M306, RST, (base or master station) Is the Make sure of correct wiring. communication cable NO See Expansion Link Function or Data Link connected to data link terminals 3 Function in the MICRO User’s Manual. correctly? YES Check error codes at the base station (expansion link) or at all stations (data link). FUN, 20, Reset the error codes at the base station NO Is the error code 0 (expansion link) or at all stations (data link). at all stations? FUN, 20, , DEL, YES At the base or master station, execute FUN27. FUN, 27, , Turn power off at the base or master station, Or, turn M307 on during operation. and turn power on after a few seconds. MON, M307, SET, Are error codes YES cleared to 0 at all stations? NO Call IDEC for assistance. END 11-6 USER’S MANUAL 11: TROUBLESHOOTING Troubleshooting Diagram 16-1 Data is not transmitted at all in the user communication mode. NO Is the protocol selector Set the protocol selector switch to 1 or 3 to switch set to 1 or 3? select user protocol for the loader port. YES Did you press the NO communication enable button for 4 sec? YES Did you power Press the communication enable button for NO down and up after changing more than 4 sec until the ERR1 indicator the protocol selector blinks once. switch? YES Is the standard NO Select the standard processing mode. processing mode FUN, 5, , , REP, selected? YES Is the NO communication cable Make sure of correct wiring. connected correctly? YES NO Is the input to the Turn the input to the TXD instruction on. TXD instruction on? YES See Troubleshooting Diagram 1, NO Is the POW (power) “The POW (power) indicator does not go 3 indicator on? on.” in the MICRO User’s Manual. YES Did you See Communication Monitor FUN29 on NO check the transmit data using page 3-1 and FUN50 on page 3-2 in this the communication user’s manual. monitor? YES Call IDEC for assistance. USER’S MANUAL 11-7 11: TROUBLESHOOTING Troubleshooting Diagram 16-2 Data is not transmitted correctly in the user communication mode. Are communication NO Set the communication parameters to match parameters set correctly those of the remote terminal using FUN8. using FUN8? YES Is the data register NO Correct the program to replace the repeated designated as transmit status data register with a different data register. used repeatedly? YES Are more than 5 Correct the program to make sure that more YES inputs to TXD instructions on than 5 inputs to TXD instructions do not go simultaneously? on simultaneously. NO Is duration of NO Make sure that the busy signal at the remote the busy signal at the remote terminal does not exceed 5 sec. terminal within 5 sec? YES Did you make NO Make sure that the transmit data designated sure of source 1 operand of the as source 1 operand is correct. TXD instruction? YES Call IDEC for assistance. When the user communication still has a problem after completing the above procedure, also perform the procedure of Diagram 16-1 described on the preceding page. 11-8 USER’S MANUAL 11: TROUBLESHOOTING Troubleshooting Diagram 16-3 Data is not received at all in the user communication mode. NO Is the protocol selector Set the protocol selector switch to 1 or 3 to switch set to 1 or 3? select user protocol for the loader port. YES Did you press the NO communication enable button for 4 sec? YES Did you power Press the communication enable button for NO down and up after changing more than 4 sec until the ERR1 indicator the protocol selector blinks once. switch? YES Is the standard NO Select the standard processing mode. processing mode FUN, 5, , , REP, selected? YES Is the NO communication cable Make sure of correct wiring. connected correctly? YES NO Is the input to the Turn the input to the RXD instruction on. RXD instruction on? YES See Troubleshooting Diagram 1, NO Is the POW (power) “The POW (power) indicator does not go indicator on? 3 on.” in the MICRO User’s Manual. YES Did you See Communication Monitor FUN29 on NO check the receive data using page 3-1 and FUN50 on page 3-2 in this the communication user’s manual. monitor? YES Call IDEC for assistance. USER’S MANUAL 11-9 11: TROUBLESHOOTING Troubleshooting Diagram 16-4 Data is not received correctly in the user communication mode. Set the communication parame- Are communication NO ters to match those of the remote parameters set correctly terminal using FUN8. using FUN8? YES Is the data register Correct the program to replace NO designated as receive status the repeated data register with a used repeatedly? different data register. YES Is a start delimiter NO speciŢed in the RXD instruction? Is one input YES NO used to start multiple RXD instructions? Correct the program to make YES Are more than 5 NO sure that more than 5 inputs to inputs to RXD instructions on RXD instructions do not go on Use one input to start one RXD simultaneously? simultaneously. instruction without a start delim- iter. YES Did you check Make sure that the start delimiter NO the start delimiter of incoming in the RXD instruction matches data? that of the incoming data. YES Make sure that the receive format Did you check NO of the RXD instruction matches the format of incoming that of the incoming data. data? YES Is an end delimiter NO speciŢed in the RXD instruction? YES Did you check Make sure that the end delimiter NO the end delimiter of incoming in the RXD instruction matches data? that of the incoming data. YES Is the receive Make sure that the receive time- NO timeout value set correctly out value is larger than character using FUN8? intervals of the incoming data. YES Did you make Make sure that the receive data NO sure of source 1 operand of the designated as the source 1 oper- RXD instruction? and is correct. YES Call IDEC for assistance. 11-10 USER’S MANUAL APPENDIX Type List 3 MICRO C CPU Base Units / Expansion I/O and Program Loader Total I/O Clock Name Points and Type No. (Inputs/Outputs) Calendar 16 points AC Power With FC2A-C16A1C Relay Output (9 in / 7 out) 24V DC Input 3 Power Voltage: MICRO C 240V AC, 2A Sink/Source 100-240V AC 24 points 30V DC, 2A CPU With FC2A-C24A1C 50/60Hz (14 in / 10 out) Base Unit, 16 points With FC2A-C16A4C DC Power Expansion Relay Output (9 in / 7 out) 24V DC Input I/O 240V AC, 2A Power Voltage: Sink/Source 24 points 30V DC, 2A 24V DC With FC2A-C24A4C (14 in / 10 out) Program Loader (loader cable not included) FC2A-HL1E 3 Note: To use the expanded capabilities of the MICRO C such as new advanced instructions for communication and compar- ison and increased data registers, use an upgraded program loader of version 2.00 or later. To check the program loader version, read FUN31 (program loader version readout/hardware check) using the FUN31 and keys on the loader. Cables and Accessories Name Function Type No. 3 Loader Cable 3C Used to connect the program loader to the MICRO C loader port FC2A-KL3C (2m/6.56 ft. long) (Note) (loader cable 3C is not included with program loader) 3 Loader Cable 4C Used to connect the program loader to MICRO C data link terminals FC2A-KL4C (2m/6.56 ft. long) (Note) (loader cable 4C is not included with program loader) 3 Computer Link Cable 4C Used to connect an IBM PC to the MICRO C loader port (1:1 com- FC2A-KC4C (3m/9.84 ft. long) (Note) puter link), with D-sub 9-pin female connector to connect to computer 3 Computer Link Cable 6C Used to connect an IBM PC to MICRO C data link terminals (1:1 com- FC2A-KC6C (2m/6.56 ft. long) (Note) puter link), with D-sub 9-pin female connector to connect to computer 3 Modem Cable 1C Used to connect a modem to the MICRO C loader port, with D-sub FC2A-KM1C (3m/9.84 ft. long) (Note) 25-pin male connector to connect to modem 3 User Communication Cable 1C Used to connect RS232C equipment to the MICRO C loader port, FC2A-KP1C (2.4m/7.87 ft. long) (Note) without a connector to connect to RS232C equipment Memory Card SRAM memory card to store 31 user programs maximum (64K bytes) FC2A-MC1 3 Expansion Cable Used to connect the MICRO C base units for close mounting in the FC2A-KE1 (250mm/9.84" long) expansion link system 3 Used for interface between an IBM PC and the MICRO C base units RS232C/RS485 Converter FC2A-MD1 in the computer link 1:N communication system or through modems RS232C Cable (4-wire) Used to connect the RS232C/RS485 converter to an IBM PC, with D- HD9Z-C52 (1.5m/4.92 ft. long) sub 9-pin female connector to connect to computer DIN Rail 3 35-mm-wide DIN rail to mount the MICRO C base unit BAA1000 (1m/3.28 ft. long) 3 Mounting Clip Used on DIN rail to fasten the MICRO C base unit BNL6 FC9Y- CUBIQ Programming and monitoring software used on a PC (3.5" diskette) LP1E314 USER’S MANUAL A-1 APPENDIX ASCII Character Code Table Upper Bit 0123456789 ABCD E F Lower Bit N D 0 U L SP 0 @ P ` p L E Decimal 0 16 32 48 64 80 96 112 128 144 160 176 192 208 224 240 S D 1 O C !1 A Q a q H 1 Decimal 1 17 33 49 65 81 97 113 129 145 161 177 193 209 225 241 S D 2 T C ”2 B R b r X 2 Decimal 2 18 34 50 66 82 98 114 130 146 162 178 194 210 226 242 E D 3 T C #3 C S c s X 3 Decimal 3 19 35 51 67 83 99 115 131 147 163 179 195 211 227 243 E D 4 O C $4 D T d t T 4 Decimal 4 20 36 52 68 84 100 116 132 148 164 180 196 212 228 244 E N 5 N A %5 EU e u Q K Decimal 5 21 37 53 69 85 101 117 133 149 165 181 197 213 229 245 A S 6 C Y &6 FV f v K N Decimal 6 22 38 54 70 86 102 118 134 150 166 182 198 214 230 246 B E 7 E T ’7 G W g w L B Decimal 7 23 39 55 71 87 103 119 135 151 167 183 199 215 231 247 C 8 BS A (8 H X h x N Decimal 8 24 40 56 72 88 104 120 136 152 168 184 200 216 232 248 9 HT EM ) 9 I Y i y Decimal 9 25 41 57 73 89 105 121 137 153 169 185 201 217 233 249 S A LF U *: J Z j z B Decimal 10 26 42 58 74 90 106 122 138 154 170 186 202 218 234 250 E B VT S +; K [ k { C Decimal 11 27 43 59 75 91 107 123 139 155 171 187 203 219 235 251 C FF FS , < L \ l | Decimal 12 28 44 60 76 92 108 124 140 156 172 188 204 220 236 252 D CR GS - = M ] m } Decimal 13 29 45 61 77 93 109 125 141 157 173 189 205 221 237 253 E SO RS . > N ^ n ~ Decimal 14 30 46 62 78 94 110 126 142 158 174 190 206 222 238 254 F SI US / ? O _ o Decimal 15 31 47 63 79 95 111 127 143 159 175 191 207 223 239 255 A-2 USER’S MANUAL INDEX data register allocation numbers 2-4 # 1:1 communication 1-5 data registers for modem mode 4-2 1:N communication 7-1 day (calendar) 2-5 A AC adapter 1-4, 1-5, 7-4 dialing 4-2 advanced instruction telephone number 4-4 CMP2 6-1 dimensions 1-10, 7-4 RXD 5-8 disconnect TXD 5-1 line 4-2 allocation numbers 2-1 mode 4-2, 4-5 analog potentiometer 1-1 double-word comparison 6-1 answer mode 4-2, 4-6 DSR control signal option 2-6 AT DTR control signal option 2-7 command result code 4-2 E editing general command mode 4-2, 4-5 RXD instruction 5-18 ATH 4-5 TXD instruction 5-7 ATZ 4-2, 4-3, 4-6 end delimiter 5-12 B BASIC program 9-3 error causes and actions 11-1 display example 9-2 escape sequence 4-5 BCC (block check character) 5-3, 5-13 expansion busy control data register service selection 2-5 control 2-6 control data registers 2-4 signal 8-1 link system 1-7, 2-2 C checking modem operation 4-10 F FUN10 control data register setting 2-4 CLKR 8-2, 10-4 FUN11 program capacity and PLC type selection clock read instruction 8-2, 10-4 Preface-2 CMP2 6-1 FUN20 PLC error data readout and reset 11-6 communication FUN27 link formatting sequence 11-6 enable button 1-1, 1-2 FUN29 user communication status readout 3-1 monitor 3-1 FUN31 program loader version readout/hardware check parameters 8-2, 9-2 Preface-2, A-1 specifications 1-8 FUN50 user communication data monitor 3-2, 4-10 comparison instruction 6-1 FUN8 loader port communication mode setting 1-9, 4-8, computer link 4-9, 5-2, 5-11, 5-12, 8-2, 9-2 1:N communication 7-1 FUN9 PLC address for network communication 7-1 using modems 7-2 function selector switch 1-1, 1-2 cable 4C 1-5, 9-1 value 2-10 cable 6C 1-5, 3-1 I I/O allocation numbers for expansion link system 2-2 interface initialization string 4-2, 4-3, 4-6, 7-2 cable 7-2 commands 4-7 unit 7-2 internal relays for modem mode 4-2 system 1-7 through data link terminals 1-5 K key operation for programming through loader port 1-5 RXD instruction 5-17 connecting TXD instruction 5-6 modem through loader port 1-6 program loader to L ladder diagram 8-2, 9-4, 10-4, 10-6 data link terminals 1-4 line connection 4-2 loader port 1-3 link RS232C equipment through loader port 1-6 communication control signal status 2-6 initialize flag 2-3 conversion type 5-2, 5-10 stop flag 2-3 systems 1-7 D data link loader protocol 1-2 cable 3C 1-3 system 1-7 cable 4C 1-4, 3-1 terminal communication port 1-1 parameters 1-9 communication protocol 4-4 specifications 1-9 status internal relays 4-2 with program loader 1-9 protocol 1-2 terminals 1-1 USER’S MANUAL i INDEX M modem 1-6, 7-2 T telephone number 4-2, 4-4 cable 1C 1-6, 4-1, 10-1 transmit 5-1 mode 4-1 bytes 5-3 mode selection 2-5 completion output 5-1, 5-5 mode status 2-5, 4-2 data 5-1, 5-2 data register 4-6 data byte count 5-5 modify initialization string 4-2 digits 5-3 month (calendar) 2-5 status 5-1, 5-5 mounting hole layout 1-10, 7-4 status code 5-5 troubleshooting 11-1 O on-line mode protocol 4-2 diagrams 11-3 operating status and control signals 2-9 TXD 5-1 operational state 4-2 editing 5-7 originate mode 4-2, 4-3 sample program 8-1 P parts description 1-1 U user communication preparation before using modem 4-8 cable 1C 1-6, 8-1 program loader 1-3, 1-4, 1-9 data monitor 3-2 programming error 11-2 data registers and internal relays 4-8 error code 5-5, 11-2 expansion control data registers 8-1 instructions 5-1 protocol mode specifications 1-8 selection in modem mode 2-5 status readout 3-1 selector switch 1-1, 1-2 user program syntax error 11-1 value 2-10 user protocol 1-2 transition 4-2 W weight Preface-2 R receive 5-8 completion output 5-8, 5-15 Y year (calendar) 2-5 data byte count 5-16 digits 5-9 format 5-8, 5-9 status 5-8, 5-16 code 5-16 repeat cycles 5-3, 5-10 operation in comparison instruction 6-2 retry cycles 4-2 RS232C cable 7-1, 7-4 equipment 1-6 RS232C/RS485 converter 7-1, 7-2, 7-3 RTS control signal ON/OFF timer 2-9 option 2-8 RXD 5-8 editing 5-18 S sample program modem communication 10-1 modem originate mode 4-9 user communication TXD 8-1 user communication TXD & RXD 9-1 selecting communication mode 1-3 serial interface specifications 7-3 setting communication parameters 4-8 skip 5-13 special internal relays 2-3 start and result internal relays 4-2 delimiter 5-11 syntax 11-1 ii USER’S MANUAL
Frequently asked questions
How does Electronics Finder differ from its competitors?

Is there a warranty for the FC2A-KM1C?

Which carrier will Electronics Finder use to ship my parts?

Can I buy parts from Electronics Finder if I am outside the USA?

Which payment methods does Electronics Finder accept?

Why buy from GID?
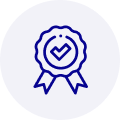
Quality
We are industry veterans who take pride in our work
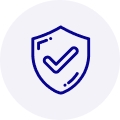
Protection
Avoid the dangers of risky trading in the gray market
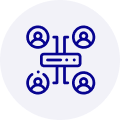
Access
Our network of suppliers is ready and at your disposal
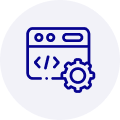
Savings
Maintain legacy systems to prevent costly downtime
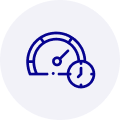
Speed
Time is of the essence, and we are respectful of yours
What they say about us
FANTASTIC RESOURCE
One of our top priorities is maintaining our business with precision, and we are constantly looking for affiliates that can help us achieve our goal. With the aid of GID Industrial, our obsolete product management has never been more efficient. They have been a great resource to our company, and have quickly become a go-to supplier on our list!
Bucher Emhart Glass
EXCELLENT SERVICE
With our strict fundamentals and high expectations, we were surprised when we came across GID Industrial and their competitive pricing. When we approached them with our issue, they were incredibly confident in being able to provide us with a seamless solution at the best price for us. GID Industrial quickly understood our needs and provided us with excellent service, as well as fully tested product to ensure what we received would be the right fit for our company.
Fuji
HARD TO FIND A BETTER PROVIDER
Our company provides services to aid in the manufacture of technological products, such as semiconductors and flat panel displays, and often searching for distributors of obsolete product we require can waste time and money. Finding GID Industrial proved to be a great asset to our company, with cost effective solutions and superior knowledge on all of their materials, it’d be hard to find a better provider of obsolete or hard to find products.
Applied Materials
CONSISTENTLY DELIVERS QUALITY SOLUTIONS
Over the years, the equipment used in our company becomes discontinued, but they’re still of great use to us and our customers. Once these products are no longer available through the manufacturer, finding a reliable, quick supplier is a necessity, and luckily for us, GID Industrial has provided the most trustworthy, quality solutions to our obsolete component needs.
Nidec Vamco
TERRIFIC RESOURCE
This company has been a terrific help to us (I work for Trican Well Service) in sourcing the Micron Ram Memory we needed for our Siemens computers. Great service! And great pricing! I know when the product is shipping and when it will arrive, all the way through the ordering process.
Trican Well Service
GO TO SOURCE
When I can't find an obsolete part, I first call GID and they'll come up with my parts every time. Great customer service and follow up as well. Scott emails me from time to time to touch base and see if we're having trouble finding something.....which is often with our 25 yr old equipment.
ConAgra Foods