OMRON AUTOMATION F3SNA0549P14
Specifications
Manufacturer
Omron Automation
Manufacturers Part #
F3SNA0549P14
Industry Aliases
F3SN-A0549P14
Sub-Category
Safety Light Curtains
Factory Pack Quantity
1
Datasheet
Extracted Text
F502-EN2-04.book Seite 3 Dienstag, 26. Juli 2005 5:48 17 Safety Light Curtain / Multi-Beam Safety Sensor F3SN-A/F3SH-A ● Type 4 sensor complying with IEC and EN standards (IEC61496-1, -2, EN61496-1). Complies with EU machine directives (certified by BG/DEMKO). ● Detection height = Sensor length meets the user’s requirements ● Detection height 189 to 1822 mm. Sensing distance 7 and 10 m. ● Various functions can be set by means of setting console. ● Equipped with a LED bar for easy adjustment of the optical axis and quick detection of failures. Features Select the optimum safety sensor for the application. Omron provides two safety types, the "Safety Light Curtain" and the "Multi-Beam Safety Sensor". Finger protection For presence inspection with a horizontal installation, types with minimum de- Safety light curtain tectable object sizes of 40 mm (optical axis pitch: 30 mm) and 70 mm F3SN-A####P14(H) (optical axis pitch: 60 mm) can also be manufactured. (Please contact your OMRON Representative.) Sensing distance : 7 m • Minimum detectable Body protection Multi-beam safety curtain object: 14 mm dia. F3SH-A09P03 (9 mm optical axis pitch) Sensing distance : 10 m • Detection height: • Number of optical axes: 4 beams (300 mm optical axis pitch) 189 to 1611 mm Hand protection Safety light curtain F3SN-A####P25 Sensing distance : 10 m • Minimum detectable object: 25 mm dia. (15 mm optical axis pitch) • Detection height: 217 to 1822 mm F3SN-A/F3SH-A G-3 F3SN-A/F3SH-A F502-EN2-04.book Seite 4 Dienstag, 26. Juli 2005 5:48 17 Features A superior standard of safety design prevents machine accidents. Self-failure diagnosis triggers output shut off. Wide-range implementation of fail-safe design. Safe design for F3SN-A Emitter Receiver The sensor itself is always Light source Power supply or circuit breakage checking to the internal breakage circuit of a floor sensor, or code disconnection and Light circuit Light receiving breakage unusual ON light. breakage Emergency stop Amp. CPU runs out of control Light receiving circuit breakage CPU Cable disconnection or CPU runs out of control CPU short-circuit Incident external light interference Even if a failure occurs, the same OFF signal as the Output drive circuit breakage normal break is output, and machine Output circuit breakage is stopped safely. Cable disconnection or short-circuit In addition, an external relay monitor function is also equipped. Technology-supported safety design Meets global safety standards for safety sensors. Safety is top priority based on the maximum standards of Type 4 sensors complying with IEC and EN standards safety design and FMEA analysis. Complies with international standards IEC61496-1 and Fail-safe design based on dual CPUs for mutual checking and IEC61496-2, and EN standard EN61496-1, which are state- duplex signal processing and output circuits. Relentless pur- of-the-art "musts" for safety sensors. suit of safety based FMEA analysis * to prove safe operation. * FMEA: Failure Mode and Effects Analysis Complies with EU directives Certification of compliance with EC testing and EMC direc- Circuit block diagram tives received from DEMKO and BG. Emitter Receiver Received UL certification for models for the U.S. Monitor and Canada. Monitor (Can be used in machines subject to OSHA rules and ANSI Control part Output standards.) Control part Received UL listing and UL listing for Canadian safety stan- Control part Output dards based on UL508 and IEC61496-1/2. Can be used in machines subject to OSHA directives (29 CFR 1910.212), which are directives related to labor safety in the U.S. Meets Monitor also the requirements of ANSI/RIA R15.06-1999, a U.S. stan- dard for industrial robots. IEC61496-1 IEC61496-1 Type IEC61496-2 Type 4 UL UL IEC61496-2 4 G-4 Safety Sensors / Components Emit light part Receiver unit F502-EN2-04.book Seite 5 Dienstag, 26. Juli 2005 5:48 17 Features We provide the perfect size for use in hazardous areas. A new concept that perfectly fits the needs of the user. Up to 3 sets can be connected in series. Mutual interfer- The detection height equals to the sensor length. ence can be prevented. Excess space has been minimized. A standard type and a link-up type with a connector can be combined to connect up to 3 sets in series. Machine Machine An excessive space The conventional Sensing width F3S#-A Sensing width Note: When you order for a sensor series connection type, please place an order with model-code F3SN-A####P## -01. An excessive space Select the optimum length 1822 mm 25 mm resolution Type 108 model 217 mm F3SN-A/F3SH-A G-5 F3SN-A/F3SH-A F502-EN2-04.book Seite 6 Dienstag, 26. Juli 2005 5:48 17 Features The setting console--the first in the industry--allows you an easy and safe setting of various functions. Includes two types of blanking functions Blanking function for changing the detection pattern of the safety light curtain. Basic pattern 1: Floating blanking function This function allows you to disable an unspecified 1, 2, or 3 optical axes. If more than the set optical axes is interrupted, the output shuts off. (Example of floating blanking function) The moving rod that is installed on the machine, can move up and down in the protective field. Floating-and-blanking function Basic pattern 2: Fixed blanking function Connection indicator Specific optical axes are masked by teaching and disabled. Function display (Power supply indicator) (Example of fixed blanking function) Channel display The sensor of series connection Optical axis can be shaded and disabled when a work Mode display piece is in detection area. However, nullification of mere optical axis will Operation switch remain as it is, even if UP: Mode select the work piece was removed. DOWN: Mode select, numeric value decrease Since it is undetectable even R: Mode select, digit move up if a hand invaded, it is dangerous. L: Mode select, digit move up CANCEL: Cancel button ENTER: Confirmation button Blanking Blanking Fix Blanking Function The fix blanking function with F3SN, the instant the work stand removed, resets blanking, and the invalid optical axis returns effectively. Since it is detectable even if a hand invaded, it is safe. Blanking release Other functions to be set with the setting console ● Auxiliary outputs: Outputs such as ON at Dark, ON at Light, light intensity diagnosis, and lockout can be selected. ● Large indicator lamp outputs: large indicator lamp outputs can be selected from ON at Dark, ON at Light, light inten- sity diagnosis, and lockout. ● External device monitoring function: Allows you to monitor the feedback of external devices. ● Interlock function: Interlocks can be set at power-on and restart. ● Setting copy function: Allows you to copy the settings of one sensor to another sensor. ● Protect function: Changing of sensor settings can be pro- hibited and restricted. G-6 Safety Sensors / Components A roller stop is not carried out. A roller stop!! F502-EN2-04.book Seite 7 Dienstag, 26. Juli 2005 5:48 17 Equipped with LED bar for easy use. F3SH-A Multi-beam safety sensor Easy optical axis adjustment using LED displays. En- Recommended dimensions of EN standard for ables certain installation. F3SH-A (4-optical axis multi-beam) ● Optical axis adjustment indicator (green only) Human body detection achieved 4 optical axes at a 300 mm pitch. Detects break by entire body. @Insufficent light level In EN Standard EN999 (machine safety: positioning of protec- tive devices in relation to the approach speed of human body @ON state of a sensor (Unstable state) parts), the values in the following table are recommended as the most effective regarding the height from the reference sur- @You can use in comfort. face (floor, etc.) of each optical axis of the 4 optical axis multi- beam sensor. The optical axis pitch of the F3SH-A matches the recommend- ed pitch, and, thus, in the installation shown in the following di- agram, every type of intrusion is detected, including intrusion by passing under the lowest optical axis and intrusion by The indicator LED passing over the highest optical axis. are visible from two directions (Installation example based on EN999 recommended dimen- Error modes can be clearly indicated to provide a sions for multi-beam safety sensors) safety backup. The top end of People cannot get over. the optical axis Error display example (red only) max.10m A wiring mistake and disconnection of an interlock selection input line or a reset input line People cannot Optical axis The welding of a relay, restoration takes time, pass through. range a wiring mistake and disconnection of an external relay monitor line Disconnection of a communication cable (RS-485), a wiring mistake, other error People cannot The bottom end of pass through. the optical axis Short-circuit of a control output, a wiring mistake, failure of a control output circuit 300mm 600mm 900mm 1200mm Independence stand Full lineup of accessories (optional) Floor face @Large-sized display @Reflecting mirror @Spatter protection indicator F39-A F39-MDG cover F39-HN The number of optical axis Height from datum plane (floor etc.) (mm) 4 300, 600, 900, 1200 When connecting, a series When the optical axis from connection model (model end an emitter is reflected at the angle of 90 degrees number -01) is required.The setting console can select with using a mirror, the the kind of signal. 2nd plane and the 3rd plane can be protected by one set of sensors. Sensing distance is lowered 15% per mirror. ● Protective tube ● Slit cover Easy safety application ● Free location brackets Various safety functions are implemented. ● Muting controller Can be adapted to various safety circuit system ● PSDI controller configurations. ● Interlock function ● Auto reset / manual reset can be selected ● External device monitoring function F3SN-A/F3SH-A G-7 F3SN-A/F3SH-A F502-EN2-04.book Seite 8 Dienstag, 26. Juli 2005 5:48 17 Ordering information Sensors Safety light curtain Infrared ray Minimum Optical Series Number of Detection detection axis Shape Sensing distance connection, Model*1 optical axes width object pitch connector F3SN-A####P14 189 to No 14 mm dia. 21 to 179 F3SN-A####P14H 1,611 mm (Finger 9 mm (odd num- 0.2 to 7m (18 mm protection) bers only) F3SN-A####P14-01*2 each) Yes F3SN-A####P14H-01 217 to F3SN-A####P25 No 25 mm dia. 1,822 mm (Hand 15 mm 13 to 120 0.2 to 10m (25 mm protection) each) Yes F3SN-A####P25-01 No F3SN-A####P40 40 mm dia. 217 to (for presence 30 mm 7 to 60 0.2 to 10m 1,807 mm protection) Yes F3SN-A####P40-01 No F3SN-A####P70 70 mm dia. 277 to (for presence 60 mm 5 to 30 0.2 to 10m 1,777 mm detection) Yes F3SN-A####P70-01 *1. #### in the model name indicates the detection width (mm). *2. F3SN-A####P14-01is a customized model. For order placement, please contact your OMRON representative. Infrared ray Multi-beam safety sensor Distance between Series Number of Optical axis pitch Shape Sensing distance optical connection, Model optical axes axes at connector each end No F3SH-A09P03 Body protection 4 900 mm 0.2 to 10m Yes F3SH-A09P03-01 Accessories (Order Separately) Control Unit Appearance Output Model Remarks For connection with the F3SN-A, and Relay, 3NO + 1NC F3SP-B1P F3SH-A, use F39-JC@B cables fitted with connectors at both ends. G-8 Safety Sensors / Components F502-EN2-04.book Seite 9 Dienstag, 26. Juli 2005 5:48 17 Safety Relay Unit Appearance Output Model Remarks For connection with the F3SN-A, and Relay, 3NO G9SA-300-SC F3SH-A, use F39-JC@C cables fitted with connectors at both ends. Muting Controller Appearance Model Remarks F3SP-U2P-TGR For connection with the F3SN-A, and F3SH-A, use F39-JC@A cables fitted with connectors at single end. F3SP-U4P-TGR Setting Console Appearance Model Accessories One branching connector, one connector cap, F39-MC11 2-m cable, instruction manual Branching Connector Appearance Model Remarks Purchase this connector when needed additionally for installing the F39-CN1 F39-MC11. Single-ended Connector Cable (For Emitter and Receiver Set) Appearance Cable length Specification Model 3 m F39-JC3A 7 m F39-JC7A M 12 connector (8 pin) 10 m F39-JC10A 15 m F39-JC15A Double-ended Connector Cable (For Emitter and Receiver Set) Appearance Cable length Specification Model Application 0.2 m F39-JCR2B Series connection or 0.5 m F39-JCR5B connection with F3SP-B1P 3 m F39-JC3B 5 m F39-JC5B M12 connector (8 pins) 7 m F39-JC7B 10 m F39-JC10B Connection with F3SP-B1P (see note 1) 15 m F39-JC15B 20 m F39-JC20B 0.2 m F39-JCR2C 1 m F39-JC1C 3 m F39-JC3C M12 connector Connection with G9SA-300-SC (8 pins) (see notes 1 and 2) 7 m F39-JC7C 10 m F39-JC10C 15 m F39-JC15C Note: 1. Cannot be used for series-connection purpose. 2. When two or more cables have to be used for connection with the G9SA-300-SC, connect the necessary number of F39-JC@B cables to one F39-JC@C cable. (Example) When a 35 m long cable is required, connect two F39-JC@B cables to one F39-JC@C. F3SN-A/F3SH-A G-9 F3SN-A/F3SH-A F502-EN2-04.book Seite 10 Dienstag, 26. Juli 2005 5:48 17 External Indicators (Separate Models for Emitters and Receivers) Appearance Specification Indicator Type Model Emitter F39-A01PR-L Red Receiver F39-A01PR-D M12 connector for PNP output Emitter F39-A01PG-L Green Receiver F39-A01PG-D Note: These indicators are used for connecting with series-connection type emitters/receivers (models ending in -01). The desired turn-ON timing (type of signal) can be selected on setting console. Spatter protection covers (1 set of 2 covers for both Emitter and receiver) Shape Applicable models Model F3SN-A####P14 F39-HN####-14 F3SN-A####P25 F39-HN####-25 F3SN-A####P25-01 F3SH-A09P03 F39-HH09-03 Note: #### in the model name indicates the 4-digit sensor detection width (in sensor models). Refection mirror (15% sensing distance attenuation) Mirror material Width (mm) Thickness (mm) Length (mm) Model F39-MDG0310 310 F39-MDG0460 460 F39-MDG0607 607 F39-MDG0750 750 F39-MDG0907 907 Glass mirror 125 31 F39-MDG1057 1,057 F39-MDG1207 1,207 F39-MDG1357 1,357 F39-MDG1500 1,500 F39-MDG1657 1,657 Note: Other sizes are available upon request IP67 environment-resistant Enclosure (A Package of tube, Gasket, and Bracket; see note) Appearance Applicable sensor Model F3SN-A@@@@P14(-01) F39-HP@@@@-14 F3SN-A@@@@P25(-01) F3SN-A@@@@P40(-01) F39-HP@@@@-25 F3SN-A@@@@P70(-01) F3SH-A09P03(-01) F39-HPH09-03 Note: Purchase 2 sets when using both an emitter and a receiver. G-10 Safety Sensors / Components F502-EN2-04.book Seite 11 Dienstag, 26. Juli 2005 5:48 17 Mounting Bracket for Sensor (Optional) Appearance Specification Model Remarks For emitter: 2 pcs. Wall mounting bracket F39-L18 For receiver: 2 pcs. Material: Iron (zinc plating) (see note) Total: 4pcs./set Free-location bracket Materials: Zinc die-cast (zinc plating) F39-L19 Minimum order quantity: 1 pc. Note: Not provided with an angle deflection mechanism for beam control. Free-location bracket Materials Sensor fixing element: Zinc die-cast (zinc plating) F39-L20 Minimum order quantity: 1 pc. Mounting bracket: Iron (zinc plating) Note: Provided with an angle deflection mechanism for beam control Note: Use these brackets for sensors having an operating range where no intermediate bracket is required (with an operating range of less than 640 mm) F3SN-A/F3SH-A G-11 F3SN-A/F3SH-A F502-EN2-04.book Seite 12 Dienstag, 26. Juli 2005 5:48 17 List of Safety Light Curtains F3SN-A####P14, F3SN-A####P14-01, F3SN-A####P14H-01 Detec- Number Detec- Number Detec- Number Model tion of optical Model tion of optical Model tion of optical height axes height axes height axes F3SN-A0675P14 (-01) F3SN-A1143P14H(-01) 675 75 1143 127 F3SN-A0189P14 (-01) 189 21 F3SN-A0693P14 (-01) F3SN-A1161P14H(-01) 693 77 1161 129 F3SN-A0207P14 (-01) 207 23 F3SN-A0711P14 (-01) F3SN-A1179P14H(-01) 711 79 1179 131 F3SN-A0225P14 (-01) 225 25 F3SN-A0729P14 (-01) F3SN-A1197P14H(-01) 729 81 1197 133 F3SN-A0243P14 (-01) 243 27 F3SN-A0747P14 (-01) F3SN-A1215P14H(-01) 747 83 1215 135 F3SN-A0261P14 (-01) 261 29 F3SN-A0765P14 (-01) F3SN-A1233P14H(-01) 765 85 1233 137 F3SN-A0279P14 (-01) 279 31 F3SN-A0783P14 (-01) F3SN-A1251P14H(-01) 783 87 1251 139 F3SN-A0297P14 (-01) 297 33 F3SN-A0801P14 (-01) F3SN-A1269P14H(-01) 801 89 1269 141 F3SN-A0315P14 (-01) 315 35 F3SN-A0819P14 (-01) F3SN-A1287P14H(-01) 819 91 1287 143 F3SN-A0333P14 (-01) 333 37 F3SN-A0837P14 (-01) F3SN-A1305P14H(-01) 837 93 1305 145 F3SN-A0351P14 (-01) 351 39 F3SN-A0855P14 (-01) F3SN-A1323P14H(-01) 855 95 1323 147 F3SN-A0369P14 (-01) 369 41 F3SN-A0873P14 (-01) F3SN-A1341P14H(-01) 873 97 1341 149 F3SN-A0387P14 (-01) 387 43 F3SN-A0891P14 (-01) F3SN-A1359P14H(-01) 891 99 1359 151 F3SN-A0405P14 (-01) 405 45 F3SN-A0909P14 (-01) F3SN-A1377P14H(-01) 909 101 1377 153 F3SN-A0423P14 (-01) 423 47 F3SN-A0927P14 (-01) F3SN-A1395P14H(-01) 927 103 1395 155 F3SN-A0441P14 (-01) 441 49 F3SN-A0945P14 (-01) F3SN-A1413P14H(-01) 945 105 1413 157 F3SN-A0459P14 (-01) 459 51 F3SN-A0963P14 (-01) F3SN-A1431P14H(-01) 963 107 1431 159 F3SN-A0477P14 (-01) 477 53 F3SN-A0981P14 (-01) F3SN-A1449P14H(-01) 981 109 1449 161 F3SN-A0495P14 (-01) 495 55 F3SN-A0999P14 (-01) F3SN-A1467P14H(-01) 999 111 1467 163 F3SN-A0513P14 (-01) 513 57 F3SN-A1017P14 (-01) F3SN-A1485P14H(-01) 1,017 113 1485 165 F3SN-A0531P14 (-01) 531 59 F3SN-A1035P14 (-01) F3SN-A1503P14H(-01) 1,035 115 1503 167 F3SN-A0549P14 (-01) 549 61 F3SN-A1053P14 (-01) F3SN-A1521P14H(-01) 1,053 117 1521 169 F3SN-A0567P14 (-01) 567 63 F3SN-A1071P14 (-01) F3SN-A1539P14H(-01) 1,071 119 1539 171 F3SN-A0585P14 (-01) 585 65 F3SN-A1089P14 (-01) F3SN-A1557P14H(-01) 1,089 121 1557 173 F3SN-A0603P14 (-01) 603 67 F3SN-A1107P14 (-01) F3SN-A1575P14H(-01) 1,107 123 1575 175 F3SN-A0621P14 (-01) 621 69 F3SN-A11125P14 (-01) F3SN-A1593P14H(-01) 1,125 125 1593 177 F3SN-A0639P14 (-01) 639 71 F3SN-A1611P14H(-01) 1611 179 F3SN-A0657P14 (-01) 657 73 Highlighted products are prefered stock types G-12 Safety Sensors / Components F502-EN2-04.book Seite 13 Dienstag, 26. Juli 2005 5:48 17 F3SN-A####P25, F3SN-A####P25-01 Detec- Number Detec- Number Detec- Number Model tion of optical Model tion of optical Model tion of optical height axes height axes height axes F3SN-A0217P25 (-01) F3SN-A0757P25 (-01) F3SN-A1297P25 (-01) 217 13 757 49 1,297 85 F3SN-A0232P25 (-01) F3SN-A0772P25 (-01) F3SN-A1312P25 (-01) 232 14 772 50 1,312 86 F3SN-A0247P25 (-01) F3SN-A0787P25 (-01) F3SN-A1327P25 (-01) 247 15 787 51 1,327 87 F3SN-A0262P25 (-01) F3SN-A0802P25 (-01) F3SN-A1342P25 (-01) 262 16 802 52 1,342 88 F3SN-A0277P25 (-01) F3SN-A0817P25 (-01) F3SN-A1357P25 (-01) 277 17 817 53 1,357 89 F3SN-A0292P25 (-01) F3SN-A0832P25 (-01) F3SN-A1372P25 (-01) 292 18 832 54 1,372 90 F3SN-A0307P25 (-01) F3SN-A0847P25 (-01) F3SN-A1387P25 (-01) 307 19 847 55 1,387 91 F3SN-A0322P25 (-01) F3SN-A0862P25 (-01) F3SN-A1402P25 (-01) 322 20 862 56 1,402 92 F3SN-A0337P25 (-01) F3SN-A0877P25 (-01) F3SN-A1417P25 (-01) 337 21 877 57 1,417 93 F3SN-A0352P25 (-01) F3SN-A0892P25 (-01) F3SN-A1432P25 (-01) 352 22 892 58 1,432 94 F3SN-A0367P25 (-01) F3SN-A0907P25 (-01) F3SN-A1447P25 (-01) 367 23 907 59 1,447 95 F3SN-A0382P25 (-01) F3SN-A0922P25 (-01) F3SN-A1462P25 (-01) 382 24 922 60 1,462 96 F3SN-A0397P25 (-01) F3SN-A0937P25 (-01) F3SN-A1477P25 (-01) 397 25 937 61 1,477 97 F3SN-A0412P25 (-01) F3SN-A0952P25 (-01) F3SN-A1492P25 (-01) 412 26 952 62 1,492 98 F3SN-A0427P25 (-01) F3SN-A0967P25 (-01) F3SN-A1507P25 (-01) 427 27 967 63 1,507 99 F3SN-A0442P25 (-01) F3SN-A0982P25 (-01) F3SN-A1522P25 (-01) 442 28 982 64 1,522 100 F3SN-A0457P25 (-01) F3SN-A0997P25 (-01) F3SN-A1537P25 (-01) 457 29 997 65 1,537 101 F3SN-A0472P25 (-01) F3SN-A1012P25 (-01) F3SN-A1552P25 (-01) 472 30 1,012 66 1,552 102 F3SN-A0487P25 (-01) F3SN-A1027P25 (-01) F3SN-A1567P25 (-01) 487 31 1,027 67 1,567 103 F3SN-A0502P25 (-01) F3SN-A1042P25 (-01) F3SN-A1582P25 (-01) 502 32 1,042 68 1,582 104 F3SN-A0517P25 (-01) F3SN-A1057P25 (-01) F3SN-A1597P25 (-01) 517 33 1,057 69 1,597 105 F3SN-A0532P25 (-01) F3SN-A1072P25 (-01) F3SN-A1612P25 (-01) 532 34 1,072 70 1,612 106 F3SN-A0547P25 (-01) F3SN-A1087P25 (-01) F3SN-A1627P25 (-01) 547 35 1,087 71 1,627 107 F3SN-A0562P25 (-01) F3SN-A1102P25 (-01) F3SN-A1642P25 (-01) 562 36 1,102 72 1,642 108 F3SN-A0577P25 (-01) F3SN-A1117P25 (-01) F3SN-A1657P25 (-01) 577 37 1,117 73 1,657 109 F3SN-A0592P25 (-01) F3SN-A1132P25 (-01) F3SN-A1672P25 (-01) 592 38 1,132 74 1,672 110 F3SN-A0607P25 (-01) F3SN-A1147P25 (-01) F3SN-A1687P25 (-01) 607 39 1,147 75 1,687 111 F3SN-A0622P25 (-01) F3SN-A1162P25 (-01) F3SN-A1702P25 (-01) 622 40 1,162 76 1,702 112 F3SN-A0637P25 (-01) F3SN-A1177P25 (-01) F3SN-A1717P25 (-01) 637 41 1,177 77 1,717 113 F3SN-A0652P25 (-01) F3SN-A1192P25 (-01) F3SN-A1732P25 (-01) 652 42 1,192 78 1,732 114 F3SN-A0667P25 (-01) F3SN-A1207P25 (-01) F3SN-A1747P25 (-01) 667 43 1,207 79 1,747 115 F3SN-A0682P25 (-01) F3SN-A1222P25 (-01) F3SN-A1762P25 (-01) 682 44 1,222 80 1,762 116 F3SN-A0697P25 (-01) F3SN-A1237P25 (-01) F3SN-A1777P25 (-01) 697 45 1,237 81 1,777 117 F3SN-A0712P25 (-01) F3SN-A1252P25 (-01) F3SN-A1792P25 (-01) 712 46 1,252 82 1,792 118 F3SN-A0727P25 (-01) F3SN-A1267P25 (-01) F3SN-A1807P25 (-01) 727 47 1,267 83 1,807 119 F3SN-A0742P25 (-01) F3SN-A1282P25 (-01) F3SN-A1822P25 (-01) 742 48 1,282 84 1,822 120 Highlighted products are prefered stock types F3SN-A####P40, F3SN-A####P40-01 Detec- Number Detec- Number Detec- Number Model tion of optical Model tion of optical Model tion of optical height axes height axes height axes F3SN-A0757P40(-01) 757 25 F3SN-A1297P40(-01) 1297 43 F3SN-A0217P40(-01) 217 7 F3SN-A0787P40(-01) 787 26 F3SN-A1327P40(-01) 1327 44 F3SN-A0247P40(-01) 247 8 F3SN-A0817P40(-01) 817 27 F3SN-A1357P40(-01) 1357 45 F3SN-A0277P40(-01) 277 9 F3SN-A0847P40(-01) 847 28 F3SN-A1387P40(-01) 1387 46 F3SN-A0307P40(-01) 307 10 F3SN-A0877P40(-01) 877 29 F3SN-A1417P40(-01) 1417 47 F3SN-A0337P40(-01) 337 11 F3SN-A0907P40(-01) 907 30 F3SN-A1447P40(-01) 1447 48 F3SN-A0367P40(-01) 367 12 F3SN-A0937P40(-01) 937 31 F3SN-A1477P40(-01) 1477 49 F3SN-A0397P40(-01) 397 13 F3SN-A0967P40(-01) 967 32 F3SN-A1507P40(-01) 1507 50 F3SN-A0427P40(-01) 427 14 F3SN-A0997P40(-01) 997 33 F3SN-A1537P40(-01) 1537 51 F3SN-A0457P40(-01) 457 15 F3SN-A1027P40(-01) 1027 34 F3SN-A1567P40(-01) 1567 52 F3SN-A0487P40(-01) 487 16 F3SN-A1057P40(-01) 1057 35 F3SN-A1597P40(-01) 1597 53 F3SN-A0517P40(-01) 517 17 F3SN-A1087P40(-01) 1087 36 F3SN-A1627P40(-01) 1627 54 F3SN-A0547P40(-01) 547 18 F3SN-A1117P40(-01) 1117 37 F3SN-A1657P40(-01) 1657 55 F3SN-A0577P40(-01) 577 19 F3SN-A1147P40(-01) 1147 38 F3SN-A1687P40(-01) 1687 56 F3SN-A0607P40(-01) 607 20 F3SN-A1177P40(-01) 1177 39 F3SN-A1717P40(-01) 1717 57 F3SN-A0637P40(-01) 637 21 F3SN-A1207P40(-01) 1207 40 F3SN-A1747P40(-01) 1747 58 F3SN-A0667P40(-01) 667 22 F3SN-A1237P40(-01) 1237 41 F3SN-A1777P40(-01) 1777 59 F3SN-A0697P40(-01) 697 23 F3SN-A1267P40(-01) 1267 42 F3SN-A1807P40(-01) 1807 60 F3SN-A0727P40(-01) 727 24 F3SN-A/F3SH-A G-13 F3SN-A/F3SH-A F502-EN2-04.book Seite 14 Dienstag, 26. Juli 2005 5:48 17 F3SN-A####P70, F3SN-A####P70-01 Detec- Number Detec- Number Detec- Number Model tion of optical Model tion of optical Model tion of optical height axes height axes height axes F3SN-A0877P70(-01) 877 15 F3SN-A1477P70(-01) 1477 25 F3SN-A0277P70(-01) 277 5 F3SN-A0937P70(-01) 937 16 F3SN-A1537P70(-01) 1537 26 F3SN-A0337P70(-01) 337 6 F3SN-A0997P70(-01) 997 17 F3SN-A1597P70(-01) 1597 27 F3SN-A0397P70(-01) 397 7 F3SN-A1057P70(-01) 1057 18 F3SN-A1657P70(-01) 1657 28 F3SN-A0457P70(-01) 457 8 F3SN-A1117P70(-01) 1117 19 F3SN-A1717P70(-01) 1717 29 F3SN-A0517P70(-01) 517 9 F3SN-A1177P70(-01) 1177 20 F3SN-A1777P70(-01) 1777 30 F3SN-A0577P70(-01) 577 10 F3SN-A1237P70(-01) 1237 21 F3SN-A1657P70(-01) 1657 28 F3SN-A0637P70(-01) 637 11 F3SN-A1297P70(-01) 1297 22 F3SN-A1717P70(-01) 1717 29 F3SN-A0697P70(-01) 697 12 F3SN-A1357P70(-01) 1357 23 F3SN-A1777P70(-01) 1777 30 F3SN-A0757P70(-01) 757 13 F3SN-A1417P70(-01) 1417 24 F3SN-A0817P70(-01) 817 14 G-14 Safety Sensors / Components F502-EN2-04.book Seite 15 Dienstag, 26. Juli 2005 5:48 17 Rating/Performance (see the operation manual for details) Sensors F3SN-A/F3SH-A F3SN-A@@@@P14 F3SN-A@@@@P25 F3SN-A@@@@P40 F3SN-A@@@@P70 Stand-alone F3SH-A09P03 Model (see notes 1 and 8) (see note 1) (see note 1) (see note 1) Series con- F3SN-A@@@@P14-01 F3SN-A@@@@P25-01 F3SN-A@@@@P40-01 F3SN-A@@@@P70-01 F3SH-A09P03-01 Item nection (see notes 1, 2 and 8) (see note 1) (see note 1) (see note 1) Sensor type Type 4 Safety Light Curtain Applicable safety category 4, 3, 2, 1, B Operating range 0.2 to 7 m 0.2 to 10 m Beam pitch (P) 9 mm 15 mm 30 mm 60 mm 300 mm 21 to 179 Number of beams (n) 13 to 120 7 to 60 5 to 30 4 (odd numbers only) 189 to 1611 mm 217 to 1822 mm 217 to 1807 mm 277 to 1777 mm Protective height (PH) —— PH = n × P PH = (n – 1) × P + 37 PH = (n – 1) × P + 37 PH = (n – 1) × P + 37 Outermost beam gap —— 900 mm Non-transparent: Non-transparent: Non-transparent: Non-transparent: Detection capability —— 14 mm in diameter 25 mm in diameter 40 mm in diameter 70 mm in diameter Effective aperture angle (EAA) Within ±2.5° for the emitter and receiver at a detection distance of at least 3 m according to IEC 61496-2 Light source Infrared LED (870 nm) (luminous wavelength) Supply voltage (Vs) 24 VDC ±10% (ripple p-p 10% max.) Up to 50 beams: 140 mA max., 51 to 85 beams: 155 mA max., 86 beams and more: 170 mA max., Current con- Emitter 140 mA max. 210 mA max. for 179 beams sumption (un- der no-load Up to 50 beams: 100 mA max., 51 to 85 beams: 110 mA max., 86 beams and more: 120 mA max., Receiver 100 mA max. conditions) 140 mA max. for 179 beams Two PNP transistor outputs, load current 300 mA max., residual voltage 2 V max. OSSD (except for voltage drop due to cable extension) Auxiliary output One PNP transistor output, load current 50 mA max., residual voltage 2 V max. (non-safety output) (except for voltage drop due to cable extension) External indicator output One PNP transistor output, load current 40 mA max., residual voltage 2 V max. (non-safety output) (see note (except for voltage drop due to cable extension) 3) OSSD output: Light-ON Output operation mode Auxiliary output: Dark-ON (can be changed by the F39-MC11) External indicator output: Light-ON (can be changed by the F39-MC11) (see note 3) For test input, interlock selection input, reset input, and external relay monitor input voltages; ON voltage: 9 to 24 V (with a sink current Input voltage of 3 mA max.), OFF voltage: 0 to 1.5 V or open Self-test (after power ON, and during operation, one cycle during response time) Test functions External test (light emission stop function by test input) Time-shared beam projection system by series connection Mutual interference preven- Number of series connected light curtains: Up to 3 sets tion function Number of beams: Up to 240 beams (see note 3) Length of the series connection cable: 3 m max. Auto reset mode/manual Auto reset/manual reset (interlock) (see note 4) reset mode (interlock) EDM (External Device Monitoring) Safety-related functions (see note 4) Fixed blanking (see note 5) EDM (External Device Floating blanking (see note 5) Monitoring) Protection Output short-circuit protection, reverse polarity protection Response time ON to OFF: 10 to 15.5 ms max., 19,5 ms max. for 179 beams ON to OFF: 10 ms max. (under stable light incident OFF to ON: 40 to 78 ms max. OFF to ON: 40 ms max. condition) Startup waiting time 1 s max. Incandescent lamp: 3000 Ix max. (light intensity on the receiver surface) Ambient light intensity Sunlight: 10000 Ix max. (light intensity on the receiver surface) Ambient temperature Operating: –10 to +55 °C, storage: –30 to +70 °C (with no icing or condensation) Ambient humidity Operating/storage: 35 to 95% RH (with no condensation) Insulation resistance 20 MΩ min. (at 500 VDC) Dielectric strength voltage 1000 VAC 50/60 Hz 1 min. Vibration resistance (malfunc- 10 to 55 Hz, double amplitude: 0.7 mm, X, Y and Z directions: 20 sweeps tion) Shock resistance (malfunc- 2 100 m/s , X, Y and Z directions: 1000 times tion) Degree of protection IP65 (IEC60529) Connection method M12 connector (8 pins) Calculate with the following equation: Weight of light curtain with protective height of 189 mm to 738 mm: (g) = (Protective height + 100) × 2 + 1300 Weight (in packaging) Weight of light curtain with protective height of 747 mm to 1402 mm: (g) = (Protective height + 100) × 2 + 1700 Weight of light curtain with protective height of 1417 mm to 1822 mm: (g) = (Protective height + 100) × 2 + 2100 Materials Case: Aluminum, cap: Zinc die-cast, optical cover: PMMA (acrylic resin) Test rod (see note 6), instruction manual, error mode label, mounting brackets (top and bottom), Accessories mounting brackets (intermediate) (see note 7) F3SN-A/F3SH-A G-15 F3SN-A/F3SH-A F502-EN2-04.book Seite 16 Dienstag, 26. Juli 2005 5:48 17 F3SN-A@@@@P14 F3SN-A@@@@P25 F3SN-A@@@@P40 F3SN-A@@@@P70 Stand-alone F3SH-A09P03 Model (see notes 1 and 8) (see note 1) (see note 1) (see note 1) Series con- F3SN-A@@@@P14-01 F3SN-A@@@@P25-01 F3SN-A@@@@P40-01 F3SN-A@@@@P70-01 F3SH-A09P03-01 Item nection (see notes 1, 2 and 8) (see note 1) (see note 1) (see note 1) IEC61496-1, EN61496-1 Type 4 ESPE (Electro-Sensitive Protective Equipment) Applicable standard IEC61496-2 Type 4 AOPD (Active Opto-electronic Protective Devices) Note: 1 .The 4 digits in @@@@ in the model number represent the protective height. Use the formula given in the information on protective height specifications to calculate the height. For example, if the beam gap is 9 mm, and the No. of beams is 21, the protective height will be 9 × 21 = 189 mm. The model with this protective height is F3SN-A0189P14. 2.F3SN-A@@@@P14-01 is a customized model. Consult with your OMRON representative when ordering this model. 3 .Models ending in -01 only. 4 .For the factory setting, the manual reset mode is set to the “start/restart” interlock. Using the F39-MC11 can select either the start interlock or the restart interlock. 5 .For the factory setting, the function is not set. It can be enabled with the F39-MC11. 6 .Not provided with the F3SN-A@@@@P70 and F3SH-A. 7 .The intermediate mounting bracket is supplied with the following types: Types which have the total length of the light curtain from 640 mm to 1280 mm: 1 set for each of emitter and receiver. Types which have the total length of the light curtain over 1280 mm: 2 sets for each of emitter and receiver. 8 .For sizes above 1,125 mm add „H“ after P14, e.g. F3SN-A1143P14H. Ask for supplemental manual. Accessories Control unit Item Model F3SP-B1P G9SA-300-SC (See note) Applicable sensor F3SN-A, F3SH-A Supply voltage 24 VDC ±10% 1.7 W DC max. (does not include the sensor’s 24 VDC: 0.7 WDC max. (does not include the Power consumption current consumption) sensor’s current consumption) 100 ms max. (does not include the sensor’s 300 ms max. (does not include the sensor’s Operating time response time) response time and bouncetime) 10 ms max. (does not include the sensor’s 10 ms max. (does not include the sensor’s Response time response time) response time and bouncetime) No. of contact 3 NO + 1 NC 3 NO Relay output Rated load 25 VAC, 5 A (cos diameter = 1), 30 VDC, 5 A L/R = 0 ms 250 VAC, 5 A Rated carry voltage 5 A Between sensor’s M12 connector (8 pins) Connection method Other Terminal block Weight (in packaging) Approx. 280 g Approx. 300 g Accessory Instruction manual Note: 1 .For further details on the G9SA-300-SC, refer to the G9SA catalogue. Setting console Large indicator lamps Item Model F39-MC11 Model F39-A01PR-L F39-A01PG-L (for emitter) (for emitter) Applicable sensor F3SN-A, F3SH-A F39-A01PR-D F39-A01PG-D Supply 24 V DC ±10% (supplied from sensor) Item (for light receiver) (for light receiver) voltage Applicable sensor F3SN-A####P##-01 F3SH-A09P03-01 Connection Special cable (accessory) Light source Red LED Green LED method Supply Weight 24 V DC ±10% (supplied by sensor) 360 g voltage (Packed state) Current Branch connector (1), special cable (2 m), 40 mA or less (supplied by sensor) Accessories consumption connector cap (1), operation manual Connection M12 connector (8-pin) For details on the setting console, method see the manual included with the product. Weight 80 g (Packed state) Environment-resistant Enclosure F39-HP@@@@-25 Item Model F39-HP@@@@-14 F39-HPH09-03 F3SN-A@@@@P25(-01)/P40(-01)/P70(-01), Applicable sensor F3SN-A@@@@P14(-01) F3SH-A09P03(-01) Operating range characteristics 0.2 to 6 m 0.2 to 10 m Degree of protection (see note) IP67 (IEC60529) Materials Case: Acrylic resin, rubber: NBR60, mounting bracket: SUS316L, screw: SUS316L Note: To conform to IP67, tighten the screws according to the “Cautions for Use” as described in the manual packaged together with the product. G-16 Safety Sensors / Components F502-EN2-04.book Seite 17 Dienstag, 26. Juli 2005 5:48 17 Connection Using a manual reset function and an external When using a auto reset function device monitoring function Emitter Emitter Receiver Emitter cable Receiver cable F39-JC#A-L F39-JC#A-D S1 S3 DC24V RS-485(A) (gray) RS-485(B) (pink) S1: External test switch S2: Interlock/lockout reset switch S3: Lock-out reset switch (if the switch is not needed, connect to 24 V DC) K1 K1, K2: Relays for control of dangerous parts of ma- chine. K3: Load, PLC, etc. (for monitor) K3 K1 K2 Note: If you do not intend to use the external relay mon- K2 S1 S2 itor, connect the auxiliary output that is set for dark: ON operation to the external relay monitor DC24V input, or use F39-MC11 to disable the external re- lay monitor function. Correct Usage This catalog is intended as a guide for product selection. Be sure to use the instruction manual provided with the product for actual operation. (5) The F3SN-A/F3SH-A received the following approvals from Regulations and Standards BG-PRUFZERT of Germany: 1. “Type Approval” specified in the Chapter 44. 2 of the Industrial BG test and approval mark Safety and Health Law in Japan does not apply to independent License units of the F3SN-A/F3SH-A sensors. This law applies to sys- tems incorporated with the sensor’s. Type 4 ESPE (EN61496-1) When using the F3SN-A/F3SH-A sensor in Japan as “safety Type 4 AOPD (prEN61496-2) devices for presses or shearing machines” as specified in the 3. The F3SN-A/F3SH-A is designed according to the following stan- Chapter 42 of the same law, apply for approval as a system. dards. To make sure that the F3SN-A/F3SH-A complies with the 2. (1) The F3SN-A/F3SH-A is electro-sensitive protective equip- following standards and regulations, you are asked to design and ment (ESPE) in accordance with European Union (EU) use it as provided by any other related standards, laws, and regula- Machinery Directive Annex IV, B, Safety Components, Item 1. tions. (Underlined regulations are applicable to the F3SN-A only.) Consult UL or other standardization bodies if you have any ques- (2) The F3SN-A/F3SH-A complies with the following regulations tions. and standards: EN415-4, prEN691, EN692, prEN693 (European stan- 1. EU Regulations dards) Machinery Directive: Directive 98/37/EC OSHA 29 CFR 1910. 212 (US Industrial Safety and EMC Directive: Directive 89/336/EEC Health Regulation) 2. European standards: EN61496-1 (TYPE 4 ESPE), OSHA 29 CFR 1910. 217 (US Industrial Safety and prEN61496-2 (TYPE 4 AOPD) Health Regulation) 3. International standards: IEC61496-1 (TYPE 4 ESPE), ANSI B11. 1 - B11. 19 (US standard) IEC61496-2 (TYPE 4 AOPD) ANSI/RIA 15. 06 (US standard) 4. American standards: UL61496-1 (type 4 ESPE), UL61496-2 (type 4 AOPD), UL508, UL1998, CAN/CSA22.2 No. 14, CAN/CSA22.2 No. 0.8 5. JIS standards: JIS B9704-1 (type 4 ESPE), JIS B9704-2 (type 4 AOPD) (3) The F3SN-A/F3SH-A received the following approvals from the EU accredited body DEMKO A/S: EC Type-Examination in accordance with the EU Machin- ery Directive (TYPE 4 ESPE) Certificate of a competent body for EMC DEMKO Type Approval Type 4 ESPE (EN61496-1) Type 4 AOPD (prEN61496-2) (4) The F3SN-A/F3SH-A received the following approvals from the Third Party Assessment Body UL: Certificate of UL listing for US and Canadian safety standards Both of which are: TYPE 4 ESPE (UL61496-1), TYPE 4 AOPD (UL61496-2) F3SN-A/F3SH-A G-17 Shielded 0V (blue) (Red) Open Test input (green) Reset input (yellow) Inter lock selection input (white) +24V (brown) +24V (brown) EDM input (red) Auxiliary (yellow) OSSD (white) OSSD (green) 0V (blue) shield Shielded 0V (blue) (Red) Open Test input (green) Reset input (yellow) Inter lock selection input (white) Open +24V (brown) F3SN-A/F3SH-A F502-EN2-04.book Seite 18 Dienstag, 26. Juli 2005 5:48 17 Detection zone and intrusion path Distances from reflective surfaces F3SN-A Safety Light Curtain Be sure to install the F3SN-A/F3SH-A to minimize the effects of re- flection from nearby surfaces. Install protective structures around the machine so that you must Failure to do so may cause detection to fail and may result in serious pass through the detection zone of the F3SN-A to reach a hazardous injury. part of the machine. Install the F3SN-A so that some part of the operator’s body remains Side View Top View in the detection zone at all times when the operator works in a haz- Reflecting ceiling Reflecting surface ardous area. Failure to do so may result in serious injury. Correct Installation D D Emitter Receiver Emitter Receiver θθ A hazardous part of a machine Some part of the operator's can be reached only by passing body remains in the detection Detection zone through the sensor detection zone while they are working. L L zone. θ= 5˚ (F3SN-A/ F3SH-A) D θ= 10˚ (F3SN-B) Reflecting floor Install the F3SN-A/F3SH-A with minimum Distance D shown above from reflective surfaces (highly reflective surfaces) such as metal walls, floors, ceilings, and work pieces. Distance between Minimum installation distance D emitter and receiver F3SN-A/ F3SH-A (Operating range L) 0. 2 to 3 m 0.13 m Incorrect Installation over 3 m L/2 × tan 2.5° = L × 0.044 (m) A hazardous part of a machine A worker is between the sensor can be reached without passing detection zone and a Safety distance through the sensor detection hazardous part of a machine. zone. Always maintain a safe distance (S) between the light curtain and a hazardous part of a machine. Failure to do so causes the machine to fail to stop before an operator reaches the dangerous area and may result in serious injury. Use of the floating blanking increases the size of the detection capa- bility. To calculate a safety distance, be sure to use the increased size of the detection capability. Failure to do so causes the machine to fail to stop before an operator reaches the dangerous area and may result in serious injury. The “safety distance” is the minimum distance that must be main- F3SH-A Multi-beam Safety Sensor tained between the F3SN-A/F3SH-A and a hazardous part of a ma- Install protective structures around the machine so that you must chine in order to stop the machine before someone or something pass through the detection zone of the F3SH-A to reach a hazardous reaches it. The safety distance is calculated based on the following part of the machine. equation when a person moves perpendicular to the detection zone If it is possible for an operator to get between the sensor’s detection of a light curtain. zone and the hazardous part of the machine, design the system so Safety distance (S) = Intrusion speed into the detection zone (K) that machinery cannot start up automatically. Make sure that machin- × Total response time for the machine and light curtain (T) ery cannot restart while the operator is in the hazardous area. Posi- tion the switch for restarting machinery in a location from which the + Additional distance calculated based on the detection capability of the light curtain (C) .......................................... (1) status of the hazardous area can be seen clearly. The switch position location must be a place where the switch cannot be operated from The safety distance varies with national standards and individual ma- within the hazardous area. chine standards. The equation is also different if the direction of in- Failure to do so may result in serious injury. trusion is not perpendicular to the detection zone of the light curtain. Be sure to refer to related standards. Use of the fixed blanking function After setting the fixed blanking, check that the F3SN-A detects a test F3SN-A Safety Light Curtain rod at any position in the detection zone through which a person can Reference reach the hazardous part of the machine. If any positions are found by check above, install protective structures to prevent intrusion, Method for calculating safety distance as provided by European Norm which the F3SN-A can not detect. EN999 (for intrusion perpendicular to the detection zone) Failure to do so may result in serious injury. Detection capaibility: 40mm or less Substitute K = 2000 mm/s and C = 8 (d – 14 mm) in equation (1) and calculate as shown below. S = 2000 mm/s × (Tm + Ts) + 8 (d – 14 mm) ......................... (2) Where: S = Safety distance (mm) Tm = Machine response time (s) (See note 1) Ts = Light curtain response time (s) (See note 2) G-18 Safety Sensors / Components F502-EN2-04.book Seite 19 Dienstag, 26. Juli 2005 5:48 17 d = Detection capability of the light curtain (mm) Response time Protective Number Model height ON to OFF to of beams Safety distance (mm) OFF ON Beam center-line mark 277 to 757 5 to 13 10.0 ms 40 ms F3SN-A@@@@ Hazardous part P70(-01) 817 to 1297 14 to 22 12.5 ms 50 ms 1357 to 1777 23 to 30 15.0 ms 60 ms Response time for series connected types is calculated as follows: (F3SN-A) For 2 sets: Response time (ON to OFF): Response time of Light Intrusion direction curtain 1 + Response time of Light curtain 2 + 3 ms Response time (ON to OFF): Response time of Light curtain 1 + Response time of Light curtain 2 + 12 ms Detection zone For 3 sets: Response time (ON to OFF): Response time of Light e. g.: curtain 1 + Response time of Light curtain 2 + Tm = 0.05 s, Ts = 0.01 s, d = 14 mm: Response time of Light curtain 3 + 4 ms S = 2000 mm/s × (0.05 s + 0.01 s) + 8 (14 mm – 14 mm) = Response time (ON to OFF): Response time of Light 120 mm curtain 1 + Response time of Light curtain 2 + Response time of Light curtain 3 + 16 ms Use S = 100 mm if the result of equation (2) is less than 100 mm. Response time of F3SP-B1P is 10 ms, operation time is Recalculate using the following equation with K = 1600 mm/s if the re- 100 ms. sult is over 500 mm. 1 . The light curtain response time refers to the time required for output to S = 1600 mm/s × (Tm + Ts) + 8 (d – 14 mm)..........................(3) change from ON to OFF. 2 .When using the F3SP-B1P, determine the safety distance by adding Use S = 500 mm if the result from equation (3) is less than the response time of the F3SP-B1P to that of the F3SN given in the 500 mm. table above. Detection capability: over 40mm Reference Substitute K = 1600 mm/s and C = 850 mm in equation (1) Method for calculating the safety distance as provided by ANSI B11. and calculate as shown below. 19 (US) Safety distance (S) = Intrusion speed into the detection zone (K) S = 1600 mm/s × (Tm + Ts) + 850 Where: S = Safety distance (mm) Response time (Ts + Tc + Tr + Tbm) + Additional distance (Dpf) Tm = Machine response time (s) (See note 1) Where: Ts = Light curtain response time (s) (See note 2) K = Intrusion speed (Recommended value in OSHA stan- e. g.: dards is 1600 mm/s) Tm = 0.05 s, Ts = 0.01 s: S = 1600 mm/s × (0.05 s + 0.01 s) + 850 mm = 946 mm ANSI B11. 19. does not define Intrusion speed (K). When de- termining K, consider possible factors including physical ability Note: 1 .The machine response time refers to the maximum time from the mo- ment the machine receives a stop signal to the moment the hazardous of operators. part of the machine stops. The machine response time should be Ts = Time required for machine to stop (s) measured on actual machines. The machine response time should be Tr = Light curtain response time (s) (See note) measured and confirmed periodically. Tc = Maximum response time required for machine control circuit to apply brake (s) Response Time Table Tbm = Additional time (s) Response time Protective If the machine is provided with a brake monitor, Tbm = brake Number Model height ON to OFF to of beams monitor setting time – (Ts + Tc). If not provided with a brake (mm) OFF ON monitor, it is recommended to determine a value more than 20% of (Ts + Tc) as the additional time. 180 to 450 20 to 50 10.0 ms 40 ms Dpf = Additional distance. 459 to 765 51 to 85 12.5 ms 50 ms F3SNA@@@@ Dpf is calculated as follows based on ANSI standards: P14(-01) 774 to 1080 86 to 120 15.0 ms 60 ms Dpf = 3.4 × (d – 7.0) where d is the detection capability of the light curtain (mm). 1089 to 1125 121 to 125 15.5 ms 62 ms e. g.: Response time Protective Number Assume that: K = 1600 mm/s, Ts + Tc = 0.06 s, Model height ON to OFF to of beams Brake monitor setting time = 0.1s, Tr = 0.01s, d = 14 mm. (mm) OFF ON Then: 217 to 772 13 to 50 10.0 ms 40 ms F3SN-A@@@@ Tbm = 0.1 – 0.06 = 0.04 s P25(-01) 787 to 1297 51 to 85 12.5 ms 50 ms Dpf = 3.4 – (14 – 7.0) = 23.8 mm 1312 to 1822 86 to 120 15.0 ms 60 ms S = 1600 × (0.06 + 0.01 – 0.04) + 23.8 = 199.8 mm Note: The light curtain response time refers to the time required for output to Response time Protective change from ON to OFF. Number Model height ON to OFF to of beams (mm) OFF ON Reference 217 to 757 7 to 25 10.0 ms 40 ms Method for calculating the safety distance as provided by ANSI/RIA F3SN-A@@@@ R15.06 (US) (for intrusion perpendicular to the detection zone) P40(-01) 787 to 1297 26 to 43 12.5 ms 50 ms Safety distance (Ds) = K × (Ts + Tc + Tr) + Dpf 1327 to 1807 44 to 60 15.0 ms 60 ms Where: F3SN-A/F3SH-A G-19 F3SN-A/F3SH-A F502-EN2-04.book Seite 20 Dienstag, 26. Juli 2005 5:48 17 K = Intrusion speed: 1600 mm/s min. Installation Ts = Maximum stop time of machine/equipment (s) How to prevent mutual interference Tc = Maximum stop time of control system (s) The emitter and the receiver to be set facing each other should be a Tr = Light curtain response time (s) pair of the same set. Erroneous combination may create a zone Os = Diameter of the smallest detectable object (mm) where objects cannot be detected. Dpf = Additional distance (mm) Do not use the sensors for a system where the beam is reflected, or Assume that the sensor is installed with the lowest beam height object detection may be disabled. In such an application, use a beam above the floor at 300 mm and the highest beam height above the floor at 1200 mm, with the diameter of the smallest detect- path diversion mirror to prevent the beam reflected from an object able object being 64 mm or less. Then, Dpf is determined from: from entering the receiver. Dpf = 3.4 × (Os – 6.875 mm). When installing two or more pairs of the F3SN-A/F3SN-B/F3SH-A, take necessary measures to prevent mutual interference. Examples If the diameter of the smallest detectable object is more than 64 mm, Dpf is calculated to be 900 mm. of such measures include electrical interconnection and the use of baffle plates. e. g.: F3SN-A@@@@P40 Safety Light Curtain Assume that K = 1600 mm/s, Ts + Tc = 0.06 s, Tr = 0.01 s, and Os = 40 mm. Then: S = 1600 × (0.06 + 0.01) + Dpf = 1600 × (0.06 + 0.01) + 3. 4 (40 – 6.875) = 225 mm F3SN-A@@@@P70 Safety Light Curtain Assume that K = 1600 mm/s, Ts + Tc = 0.06 s, Tr = 0.01 s, and Dpf = 900 mm. Then: S = 1600 × (0.06 + 0.01) + 900 = 1012 mm Note: The light curtain response time refers to the time required for output to change from ON to OFF. F3SH-A Multi-beam Safety Sensor Reference Method for calculating safety distance as provided by European Norm EN999 (for intrusion perpendicular to the detection zone) Substitute K = 1600 mm/s and C = 850 mm in equation (1) and calcu- late as shown below. S = 1600 mm/s × (Tm + Ts) + 850 Where: S = Safety distance (mm) Tm = Machine response time (s) (See note 1) Ts = Sensor response time (s) (See note 2) e. g.: Tm = 0.05 s, Ts = 0.01 s: S = 1600 mm/s × (0.05 s + 0.01 s) + 850 mm = 946 mm Note: 1 .The machine response time refers to the maximum time from the mo- ment the machine receives a stop signal to the moment the hazardous part of the machine stops. The machine response time should be measured on actual machines. The machine response time should be measured and confirmed periodically. 2 .The sensor response time refers to the time required for output to change from ON to OFF. G-20 Safety Sensors / Components F502-EN2-04.book Seite 21 Dienstag, 26. Juli 2005 5:48 17 Correct Use When not connected Installation When installing two or more pairs of light curtains independently from How to prevent mutual interference each other due to inconvenience of wiring or other reason, take prop- Series connection (Up to 3 sets, 240 beams, sensor models ending er measures to prevent mutual interference. If mutual interference in -01, -03, -04, and -05 are required for series connection) occurs, a lockout condition will result for the F3SN-A/F3SH-A. Installation which may cause mutual interference Two or more pairs of the F3SN-A can be connected in series. When Incorrect connected in series, the F3SN-A sensors generate beams in a time- Emitter 1 Receiver 1 Emitter 2 Receiver 2 sharing manner. Thus, they prevent mutual interference and ensure safety. Correct Emitter 1 Receiver 1 Cable for connection F39-JCR2B or Incorrect Incorrect F39-JCR5B or Emitter 1 Receiver 1 F39-JC3B Emitter 1 Receiver 1 Emitter 2 Receiver 2 Emitter 2 Receiver 2 Receiver Emitter Emitter 2 Receiver 2 Incorrect Incorrect Emitter 1 Receiver 1 Emitter 1 Receiver 2 Installation to prevent mutual interference (1) Install so that the two light curtains emit in the opposite directions Receiver 2 Emitter 2 Emitter 2 Receiver 1 (staggered). Correct Receiver 1 Emitter 1 Emitter 2 Receiver 2 Do not connect the emitter and Do not combine an emitter with a receiver in series, or a lockout receiver of a different pair. condition will result. This will cause a lockout condition and detection of objects will be disabled. Correct Correct Emitter 1 Receiver 1 Receiver 1 Emitter 1 Emitter 2 Receiver 2 Receiver 2 Emitter 2 (2) Install a light interrupting wall in between sensors. Correct Emitter 1 Receiver 1 Emitter 2 Receiver 2 Light interrupting wall F3SN-A/F3SH-A G-21 F3SN-A/F3SH-A F502-EN2-04.book Seite 22 Dienstag, 26. Juli 2005 5:48 17 (3) Install the light curtains facing away from the one another to elim- Distance between Minimum installation distance D inate mutual interference. emitter and receiver F3SN-A/ F3SH-A (Operating range L) Correct Correct L Emitter 1 Receiver 1 Emitter 1 Receiver 1 0. 2 to 3 m 0.26 m θ over 3 m L × tan 5° = L × 0.088 (m) D Emitter 2 Receiver 2 (4) Use a F39-HS spatter protection slit cover. θ L D Operating range Emitter 2 Receiver 2 If the distance between the emitter and the receiver is less than 0.2 θ= 5˚ (F3SN-A/ F3SH-A) θ= 10˚ (F3SN-B) m, there is a possibility of chattering. Be sure to use the sensors with- in the rated operating range. Names and Functions of Parts Emitter (F3SN-A/ F3SH-A) Test indicator (Orange) Lockout indicator (Red) Interlock indicator (Yellow) Error mode Light intensity level indicator (Red) indicator (Green) Power indicator (Green) Receiver (F3SN-A) OFF-state indicator (Red) Error mode Light intensity ON-state indicator (Green) indicator (Red) level indicator (Green) Lockout indicator (Red) Blanking indicator (Green) Receiver (F3SH-A) OFF-state indicator (Red) Error mode Light intensity level ON-state indicator (Green) indicator (Red) indicator (Green) Lockout indicator (Red) Power indicator (Green) Function Lit when power is supplied (always lit) .............................................. F3SN-A, F3SH-A Emitter Power indicator Lit when power is supplied, flashing when the F39-MC11 is connected ...... F3SH-A Receiver (see note) Interlock indicator Lit during interlock condition Lockout indicator Flashing during lockout condition Test indicator Lit during external test (see note) ON-state indicator Lit when OSSD outputs are in ON-state OFF-state indicator Lit when OSSD outputs are in OFF-state Blanking indicator (F3SN-A only) Lit when blanking is set, flashing when the F39-MC11 is connected (see note) Note: As a preventive maintenance feature, these indicators will flash after a lapse of 30000 hours. G-22 Safety Sensors / Components F502-EN2-04.book Seite 23 Dienstag, 26. Juli 2005 5:48 17 12 345 Light intensity level 200% and above of ON threshold level 150 to 200% of ON threshold level Light intensity level indicator 100 to 150% of ON threshold level 75 to 100% of ON threshold level Lit Not lit 50 to 75% of ON threshold level Less than 50% of ON threshold level ABC Cause of error The Interlock selection input line or the reset input line is not wired correctly or became open. Relay contact is welded. Releasing time of the relay takes too long. The EDM input line is not wired correctly or became open. Error mode indicator Communication line (RS-485) is not wired correctly, became open, or causes other errors. One of the OSSD outputs is shorted or is not wired correctly. Other failure in OSSD outputs. Flashing Not lit Mutual interference. Interference light is received. Types of the receiver and emitter are not the same. Numbers of the receiver and emitter connected in series are not the same. External noise. Internal hardware failure of the receiver or the emitter. Installation How to attach mounting bracket (F39-L19/L20) To fully utilize the performance of Mounting B/2 Screw × length (mm) Tightening torque sensors, locate the F39-L19/L20 bracket A/2 mounting brackets in the number sat- F39-L19 M5 × 12 screw 2.0 N·m isfying the dimensions “A” and “B” in F39-L20 M4 × 8 screw 1.2 N·m the sensor longitudinal direction. For the F39-L19 B F39-L19 F39-L20 Spacing “A”: 670 mm max. A Emitter/ For the F39-L20 receiver-mounted Mounting M4 × 8 screw face Mounting bracket (1) Spacing “B”: 400 mm max. bracket (3) Toothed washer Note: When installing sensors at locations (2 pcs.) susceptible to vibration and shock, Emitter/ increase the number of mounting receiver-mounted brackets. face B M5 × 12 A screw Mounting bracket (2) Brackets and screws included in one set • Mounting bracket (1) .....1 F39-L19 • Mounting bracket (2) .....1 [Brackets (1) and (2), M5 × 12 screw] • M5 × 12 screw ..............1 B/2 A/2 Brackets and screws included in one set • Mounting bracket (1) .....1 • Mounting bracket (2) .....1 • M5 × 12 screw ..............1 • Mounting bracket (3) .....1 • M4 × 8 screw ................1 • Toothed washer ............2 F3SN-A/F3SH-A G-23 F3SN-A/F3SH-A F502-EN2-04.book Seite 24 Dienstag, 26. Juli 2005 5:48 17 Dimensions (Unit: mm) Main unit F3SN-A@@@@P@@ F3SN-A@@@@P@@-01 F3SN-A@@@@P@@-01 Connector cap 14 20.8 17.3 Mounting screw holes 2 mounting holes 6. 5 dia. 20 Four, M5 2 mounting brackets 22 (16) 8 2 P F 30 28 27 Two, M5 22 5.5 Two, M5 9.25 15 15 38 (41.8) E BA B 11 Intermediate 2 mounting holes bracket M5 up-set hexagon bolt F Beam 1 15 D 11 13.5 32 16 4 mounting holes 45 5.5 9 dia. 2 mounting holes 46.9 20 30 Dimensions according to the model can be calculated by using the following F3SN-A@@@@P25(-01)/P40(-01)/P70(-01), F3SN-B@@@@P25/P40/P70 equations. Dimension C1 (protective height): 4 digits in the model name F3SN-A@@@@P14(-01) Dimension A = C1 + 64 Dimension B = C1 + 32 Dimension C2 (protective height): 4 digits in the model name Dimension D = 18.5 Dimension A = C2 + 86 Dimension E = C1 – 37 Dimension B = C2 + 54 Dimension F: See the table below. Dimension D = 15.5 Dimension E = C2 – 9 Number of intermediate Dimension F Dimension F: See the table below. C1 (protective height) mounting bracket (see note) Dimension P = 9 to 0640 0 —— Number of intermediate Dimension F 0641 to 1280 1 F = B/2 C2 (protective height) mounting bracket (see note) 1281 to 1822 2 F = B/3 to 0620 0 —— Dimension P: See the table below 0621 to 1125 1 F = B/2 . Note: If value F obtained from the above equation is not used, set F Detection capability Dimension P to 670 mm or less. 25 15 40 30 70 60 G-24 Safety Sensors / Components C1 (Protective height) C2 (Protective height) F502-EN2-04.book Seite 25 Dienstag, 26. Juli 2005 5:48 17 F3SH-A09P03 F3SH-A09P03-01 F3SH-A09P03-01 Connector cap 14 20.8 17.3 Mounting screw holes 2 mounting brackets 2 mounting holes 6.5 dia. 20 Four, M5 22 (16) 8 4 beam mark 2 484.5 30 28 27 Two, M5 22 5.5 Two, M5 9.25 15 15 38 (41.8) 937 900 969 1001 969 11 Intermediate 2 mounting holes bracket M5 up-set hexagon bolt 484.5 300 4 beams 1 18.5 15 13.5 32 16 4 mounting holes 45 5.5 9 dia. 2 mounting holes 46.9 20 30 Mounting Precautions Connector cable Note: 1 .The mounting bracket (3) (see Mounting brackets (intermediate)) is shown on the left-hand side of the sensor as an example. If the mount- ing bracket (3) is on the right-hand side of the sensor then the mount- R36 mm ing holes must also be on the right-hand side. 80 mm min. 2 .When using with the cable bent, allow at least the dimensions shown on the right. (Minimum bending radius of cable: R36 mm.) 80 mm min. R36 mm Connector cable F3SN-A/F3SH-A G-25 F3SN-A/F3SH-A F502-EN2-04.book Seite 26 Dienstag, 26. Juli 2005 5:48 17 Accessories Mounting brack 5.5 6.5 dia. et (top and bottom) 9.25 14 24 13.5 20 9 dia. 4-30˚ 14.2 dia. 22 dia. Four, R2.15 45 Material: Iron (zinc plating) 4.3 30 30 2 R2 max. Note: Provided with the product. Mounting brackets (intermediate) 25 11 16 2 1 22 17 12 22 10 30 42 22 20 Material: Iron (zinc plating) M5 × 8 bracket fixing screw 16 22 2.3 Intermediate bracket (3) 6.5 dia. 11 13.75 11 18 21.25 33 38 15 Note: Provided with the product. The number of brackets re- 11 19 quired depends on the total 30 5.5 5.5 Intermediate M4 × 6 sensor fixing screw length of the Sensor. 9 dia. Intermediate bracket (2) bracket (1) Accessories (Optional) Single-ended connector cable F39-JC3A (L = 3 m) F39-JC10A (L = 10 m) F39-JC7A (L = 7 m) F39-JC15A (L = 15 m) 39.5 L (See note) 15 dia. Waterproof connector Vinyl insulated round cable 6.6 mm dia. 2 8 cores (4 twisted pairs) (conductor cross sectional area: 0.3 mm / insulation outside diameter: 1.15 mm dia.) Standard length L Note: L = 3, 7, 10, 15 m Color:Emitter (gray) Receiver (black) Double-ended connector cable F39-JCR2B (L = 0.2 m) F39-JC7B (L = 7 m) F39-JCR2C (L = 0.2 m) F39-JC10C (L = 10 m) F39-JCR5B (L = 0.5 m) F39-JC10B (L = 10 m) F39-JC1C (L = 1 m) F39-JC15C (L = 15 m) F39-JC3B (L = 3 m) F39-JC15B (L = 15 m) F39-JC3C (L = 3 m) F39-JC5B (L = 5 m) F39-JC20B (L = 20 m) F39-JC7C (L = 7 m) 39.5 L 43 15 dia. 15 dia. Waterproof connector Waterproof connector Vinyl insulated round cable 6.6 mm dia. 2 8 cores (4 twisted pairs) (conductor cross sectional area: 0.3 mm / insulation outside diameter: 1.15 mm dia.) Standard length L Color:Emitter (gray) Receiver (black) G-26 Safety Sensors / Components F502-EN2-04.book Seite 27 Dienstag, 26. Juli 2005 5:48 17 Control unit Emitter F3SP-B1P Receiver 91 24, M3 10.5 Mounting screw holes 5.9 7 × 5 = 35 Two, 4.2 dia. or M4 4.6 dia. 13 max. 9 ±0.3 76 max. 63 43 84 5.6 9 ±0.3 45 max. 5 35 R2.3 111 max. Safety relay unit G9SA-300-SC 92 24, M3 × 8 5.9 13 max. 76 max. 63 111 max. 710 80 91 max. F3SN-A/F3SH-A G-27 F3SN-A/F3SH-A F502-EN2-04.book Seite 28 Dienstag, 26. Juli 2005 5:48 17 Setting console Branching connector (supplied with F39-MC11) F39-MC11 F39-CN1 13 2 Communications jack 4 8 M12 76 5 18 13.6 32.1 CN1 Communications 17.7 22 52.8 connection indicator 4 M12 Function indicator 56 12 24.7 CN3 3 1 Channel display 2 13.6 Channel keys CN2 Two, 8 dia. Mode display 10 (spot facing depth: 2 mm) 15 Two, 4.5 dia. Up key 3 4 5 M12 136 8 Right key 6 2 17 Down key Left key Enter key CN1 Connector cable Cancel key CN2 Sensor CN3 Setting console 50 External indicator F39-A01PR-L/-D F39-A01PG-L/-D 30 dia. Lighting part 96 104.3 9.2 Waterproof connector G-28 Safety Sensors / Components F502-EN2-04.book Seite 29 Dienstag, 26. Juli 2005 5:48 17 Spatter protection cover Protection cover F39-HN@@@@-14 F39-HN@@@@-25 32 F39-HH09-03 L (see note) 10 Note: L is as follows. F39-HN@@@@-14 L = @@@@ mm Materials: PC (transparent area) ABS (non-transparent area) F39-HN@@@@-25 L = @@@@ – 22 mm F39-HH09-03 L = 915 mm Mounting dimensions Fixing bracket 32.6 37.3 37.3 Materials: SUS 9.87 14 Environment-resistant enclosure F39-HP@@@@-14 F39-HP@@@@-25 F39-HPH09-03 32 61 dia. 57.5 dia. Mounting bracket M4 × 12 screw Case L (depends on the length of housing of each model) 3 8 16 2 24 8 34 R2.8 30 9 dia. F3SN-A/F3SH-A G-29 F3SN-A/F3SH-A F502-EN2-04.book Seite 30 Dienstag, 26. Juli 2005 5:48 17 Wall mounting bracket F39-L18 90˚ 33 18 15.5 12.25 2 5.5 9 dia. 30˚ 20 22 dia. 4.3 14.2 dia. 30 Eight, R2.15 Free-location bracket Mounting F39-L19 5 30 Emitter cover or receiver cover 8.5 5 3.3 11 18 30 (6.4) 1.5 (40) 20 5.5 dia. 24 10.8 10 10 5 (32.3) 37 M5 up-set M5 up-set hexagon bolt 7 15 hexagon bolt (4.7)(15.5) Free-location bracket 25.5 F39-L20 10.5 5.5 dia. 24 43 32.75 M4 up-set 17.75 30.5 12 hexagon bolt 19.3 12 6.5 5 6 (14) (15.5) 20 15.5 23 9 dia. 20 (4.7) 6.5 dia. M5 up-set 5.5 hexagon bolt (4.7) 11 0.8 10 25.25 (15) Side mounting (43) (30.5) (30) M4 up-set hexagon bolt (14) 23 (44) 30 30 M5 up-set hexagon bolt (15) Emitter cover or receiver cover Back mounting (15) M4 up-set hexagon bolt Emitter cover or receiver cover 30 30 (44) (44) (23) (14) (4.7) (43) M5 up-set hexagon bolt ALL DIMENSIONS SHOWN ARE IN MILLIMETERS. To convert millimeters into inches, multiply by 0.03937. To convert grams into ounces, multiply by 0.03527. Cat. No. E700-EN2-01-X In the interest of product improvement, specifications are subject to change without notice. G-30 Safety Sensors / Components
Frequently asked questions
How does Electronics Finder differ from its competitors?

Is there a warranty for the F3SNA0549P14?

Which carrier will Electronics Finder use to ship my parts?

Can I buy parts from Electronics Finder if I am outside the USA?

Which payment methods does Electronics Finder accept?

Why buy from GID?
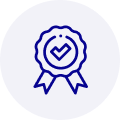
Quality
We are industry veterans who take pride in our work
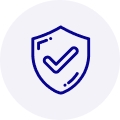
Protection
Avoid the dangers of risky trading in the gray market
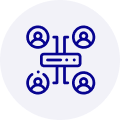
Access
Our network of suppliers is ready and at your disposal
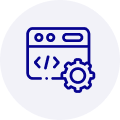
Savings
Maintain legacy systems to prevent costly downtime
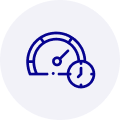
Speed
Time is of the essence, and we are respectful of yours
What they say about us
FANTASTIC RESOURCE
One of our top priorities is maintaining our business with precision, and we are constantly looking for affiliates that can help us achieve our goal. With the aid of GID Industrial, our obsolete product management has never been more efficient. They have been a great resource to our company, and have quickly become a go-to supplier on our list!
Bucher Emhart Glass
EXCELLENT SERVICE
With our strict fundamentals and high expectations, we were surprised when we came across GID Industrial and their competitive pricing. When we approached them with our issue, they were incredibly confident in being able to provide us with a seamless solution at the best price for us. GID Industrial quickly understood our needs and provided us with excellent service, as well as fully tested product to ensure what we received would be the right fit for our company.
Fuji
HARD TO FIND A BETTER PROVIDER
Our company provides services to aid in the manufacture of technological products, such as semiconductors and flat panel displays, and often searching for distributors of obsolete product we require can waste time and money. Finding GID Industrial proved to be a great asset to our company, with cost effective solutions and superior knowledge on all of their materials, it’d be hard to find a better provider of obsolete or hard to find products.
Applied Materials
CONSISTENTLY DELIVERS QUALITY SOLUTIONS
Over the years, the equipment used in our company becomes discontinued, but they’re still of great use to us and our customers. Once these products are no longer available through the manufacturer, finding a reliable, quick supplier is a necessity, and luckily for us, GID Industrial has provided the most trustworthy, quality solutions to our obsolete component needs.
Nidec Vamco
TERRIFIC RESOURCE
This company has been a terrific help to us (I work for Trican Well Service) in sourcing the Micron Ram Memory we needed for our Siemens computers. Great service! And great pricing! I know when the product is shipping and when it will arrive, all the way through the ordering process.
Trican Well Service
GO TO SOURCE
When I can't find an obsolete part, I first call GID and they'll come up with my parts every time. Great customer service and follow up as well. Scott emails me from time to time to touch base and see if we're having trouble finding something.....which is often with our 25 yr old equipment.
ConAgra Foods