TE CONNECTIVITY 68011-1
Specifications
Manufacturer
TE Connectivity
Manufacturers Part #
68011-1
Industry Aliases
68011-1
Sub-Category
Hardware Tools
Brand
AMP
Factory Pack Quantity
1
Datasheet
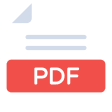
DDEController?Action=showdoc&DocId=Specification+Or+Standard%7F408-2281%7FCD%7Fpdf%7FEnglish%7FENG_SS_408-2281_CD_408-2281.pdf
512 KiB
Extracted Text
Instruction Sheet Crimping Die Assemblies for COPALUM* Sealed Terminals 408-2281 and Splices 25 JAN 18 Rev CP Stationary Die Shank (Nest) Alignment Dot Moving Die (Anvil) Front of Die Assembly Alignment Dot Shank Figure 1 CRIMPING DIE HYDRAULIC HYDRAULIC CRIMPING HEAD ASSEMBLY CRIMPING HEAD (INSTRUCTION SHEET) 68006 68007 68008● 58422-1 408-9535 68008-1 69066 408-2453 68009 1752787-1 408-8914 68010 1752877-1 408-8956 68010-1■ 68010-2 314964-1▲ 59877-1 68011-1 314948-1 1976441-1 1976442-1 1976443-1 2217781-1 58422-1 408-9535 2217855-1 1752787-1 408-8914 2280034-1 2280035-1 2844065-1 2844065-2 2844425-2 2844430-1 2844430-2 ●Superseded by 68008-1 ■Superseded by 68010 ▲Low Pressure Crimp Die Set Table 1 © 2018 TE Connectivity Ltd. family of companies. PRODUCT INFORMATION 1-800-522-6752 This controlled document is subject to change. 1 of 12 All Rights Reserved. For latest revision and Regional Customer Service, *Trademark visit our website at www.te.com. TE Connectivity, TE connectivity (logo), and TE (logo) are trademarks. Other logos, product, and/or company names may be trademarks of their respective owners. ORIGINAL INSTRUCTIONS 408-2281 1. INTRODUCTION The crimping die assemblies are designed to be installed into the hydraulic crimping heads listed in Table 1 and are used to crimp COPALUM sealed terminals and splices. Read these instructions thoroughly before crimping any terminals or splices. Reasons for reissue of this instruction sheet are provided in Section 8, REVISION SUMMARY. NOTE Dimensions in this instruction sheet are in millimeters [with inches in brackets]. Illustrations are for reference only and are not drawn to scale. 2. DESCRIPTION Each crimping die assembly consists of a stationary die (nest) and moving die (anvil). Each die features an alignment dot on the front of the die. See Figure 1. 3. DIE ASSEMBLY INSTALLATION For information concerning die installation and general performance of the hydraulic crimping head, refer to the instruction sheet packaged with the crimping head. DANGER To avoid personal injury, ALWAYS DISCONNECT electrical and air supply to power unit before installing the hydraulic crimping head or die assembly. In order to achieve proper mating of the dies during installation, ensure that: — the shanks of the dies are offset to the same surface of the die, but that the alignment dots align and face the operator — the anvil moves and the nest is stationary CAUTION DO NOT mix dies from different or the same die assemblies (because of inconsistent wearing) — it is important that the dies are used as the set. DANGER To avoid personal injury, make sure to close the yoke of the hydraulic crimping head and fully insert the pin. When operating the power unit, be careful when handling terminals, splices, or wire near the crimping area of the die assembly. 4. CRIMPING PROCEDURE Select the die assembly and terminal or splice, and prepare the wire as follows: 1. Refer to Figure 2/Table 2 to select the appropriate die assembly and terminal or splice according to the wire. NOTE For aluminum-to-aluminum application, butt splices will accept the same wire size at either end. For aluminum-to-copper application, the copper wire size must be smaller to compensate for differences in the electrical properties of copper and aluminum. This also applies when using copper wire in a terminal as listed in Table 2. 2. Cut the end of the wire perpendicular to the wire; DO NOT distort the shape of the wire. It is recommended to chamfer the edge around the group of wires. See Figure 2. The chamfer will aid in the insertion of the wire into the terminal or splice. 3. Strip the wire to the length indicated in Figure 2/Table 2. DO NOT nick or cut the wire strands. The strip length for the wire will depend on the number of insulation layers covering the wire. There are two approved methods for crimping the terminals and splices using these die assemblies and hydraulic crimping heads. Proceed as follows: 2 of 12 Rev CP 408-2281 4.1. Terminal IMPORTANT: To ensure a quality crimp, gage the die assembly at the beginning of a run, after changing a die assembly — and then periodically during the run. Refer to paragraph 6.2 for gaging instructions. Ring Tongue (RT) Ring Tongue (RT) Flag Ring Tongue Single Hole Terminal Double Hole Terminal (RT) Terminal Figure 2 Terminal (RT) Wire Strip Length Butt Aluminum Copper Die Crimping ±1.59 [1/16] Single Double Insulation Splice (BS) Assy Head Bent Hole Hole Range 2 2 mm mm A B AWG AWG (CMA)† (CMA)† (Insul) (Wire) 8.60 4.80 4.62-5.08 22.23 11.11 277147-[ ] --- --- 277156-[ ] 8 10 68006 (16,564) (9,354) [.182-.200] [7/8] [7/16] 14.60 8.80 5.72-6.35 22.23 12.70 277148-[ ] 55832-[ ] --- 277157-[ ] 6 8 68007 (28,280) (16,983) [.225-.250] [7/8] [1/2] 135148-[ ] 21.90 13.80 7.01-7.75 25.40 17.45 136059-[ ] 55833-[ ] --- 277158-[ ] 4 6 68008-1 (42,420) (26,818) [.276-.305] [1] [11/16] 277149-[ ] 58422-1 134848-[ ] 69066 135563-[ ] 55835-[ ] 35.00 22.00 8.64-9.65 31.75 19.10 1752787-1 2300438-[ ] 90º 277159-[ ] 2 4 68009 277150-[ ] 55935-[ ] (67,872) (42,615) [.340-.380] [1 1/4] [3/4] 1752877-1 277155-[ ] 134452-[ ] 134593-[ ] 136994-[ ] 70º 34.30 10.79-11.94 55837-[ ] 277160-[ ] 2 277151-[ ] 696632-[ ] 90º (66,500) [.425-.470] 55.50 32.54 25.40 1/0 68010 1577118-[ ] (107,464) [1 9/32] [1] 11.18-11.94 1958110-2● --- --- --- --- --- [.440-.470] 69066, 134594-[ ] 1958038-[ ] 90º 314964-1▲ 71.30 53.90 12.70-13.97 34.93 25.40 1752877-1 277152-[ ] 55839-[ ] 2289812-[ ] 90º 277161-[ ] 2/0 1/0 (138,168) (104,500) [.500-.550] [1 3/8] [1] 696972-[ ] 2317551-[ ] 45º 68011-1 277153-[ ] 2325332-[ ] 60º 87.20 68.60 13.21-16.38 34.93 25.40 696767-[ ] 55840-[ ] 277162-[ ] 3/0 2/0 59877-1 58422-1 2327315-[ ] 45º (168,872) (133,000) [.520-.645] [1 3/8] [1] 696974-[ ] 1752787-1 184113-[ ] 55841-[ ]† 110.94 85.94 14.99-17.27 33.34 25.40 --- --- 4/0 3/0 314948-1 55995-[ ] 696786-[ ] (214,928) (166,500) [.590-.680] [1 5/16] [1] Table 2 (Cont’d) 3 of 12 Rev CP 408-2281 Wire Strip Length Transitional Aluminum Copper Die Crimping ±1.59 [1/16] Insulation Butt Splice (TS) Assy Head 2 2 Range mm mm A B AWG AWG (CMA)† (CMA)† (Insul) (Wire) 55.50 22.00 AI End: 10.80-11.94 [.425-.470] 32.54 25.4 58422-1 277163-[ ] 1/0 4 68010 (107,464) (42,615) Cu End: 7.01-7.75 [.276-.305] [1 9/32] [1] 69066 1752787-1 21.90 8.80 AI End: 7.01-7.75 [.276-.305] 25.40 17.45 277164-[ ] 4 8 68008-1 1752877-1 (42,420) (16,983) Cu End: 5.33-6.48 [.210-.255] [1] [11/16] 87.20 53.90 AI End: 13.21-16.38 [.520-.645] 34.93 25.40 58422-1 277168-[ ] 3/0 1/0 59877-1 (168,872) (104,500) Cu End: 10.92-12.97 [.430-.495] [1 3/8] [1] 1752787-1 Table 2 (Cont’d) Terminal (RT) Wire Butt Die Crimping Aluminum Copper Single Double Insulation Strip Length Splice (BS) Assy Head 2 2 mm mm B (Wire) Hole Hole Range AWG AWG (CMA)† (CMA)† 8.60 4.80 5.59-6.30 11.11 696866-[ ] 696804-[ ] 696852-[ ] 8 10 68006 (16,564) (9,354) [.220-.248] [7/16] 696887-[ ] 696951-[ ] 14.60 8.80 6.60-7.39 12.70 696869-[ ] 696847-[ ] 6 8 68007 696953-[ ] (28,280) (16,983) [.260-.291] [1/2] 696999-[ ] 58422-1 21.90 13.80 8.23-9.04 15.88 696872-[ ] 696834-[ ] 696854-[ ] 4 6 68008-1 69066 (42,420) (26,818) [.324-.356] [5/8] 1752787-1 35.00 22.00 9.65-10.59 19.10 1752877-1 696838-[ ] 696890-[ ] 696857-[ ] 2 4 68009 (67,872) (42,615) [.380-.417] [3/4] 696830-[ ] 34.30 11.10-13.03 696875-[ ] 696957-[ ] 696843-[ ] 2 (66,500) [.437-.513] 55.50 20.57 696959-[ ] 1/0 68010 (107,464) [.810] 11.10-12.37 1958110-1● --- --- --- --- [.437-.487] 69066, 314964-1▲ 696878-[ ] 71.30 53.90 12.70-14.58 25.40 1752877-1 696840-[ ] 696861-[ ] 2/0 1/0 696819-[ ]● (138,168) (104,500) [.500-.574] [1] 68011-1 696825-[ ] 696881-[ ] 87.20 68.60 13.21-16.08 25.40 696961-[ ] 696863-[ ] 3/0 2/0 59877-1 696821-[ ]● (168,872) (133,000) [.520-.633] [1] 58422-1 696963-[ ] 1752787-1 696884-[ ] 110.94 85.94 15.62-17.35 25.40 696823-[ ]● 696893-[ ] 696849-[ ] 4/0 3/0 314948-1 (214,928) (166,500) [.615-.683] [1] 1958035-[ ] Table 2 (Cont’d) 4 of 12 Rev CP 408-2281 Terminal (RT) Wire Aluminum Copper Strip Length Die Crimping Single Double Insulation B (Wire) 2 2 Assy Head Bent mm mm Hole Hole Range ±1.59 [1/16] AWG AWG (CMA)† (CMA)† 2844065-1 2297683-[ ] --- --- 35.00 22.00 8.64 – 9.70 19.05 2844065-2 2 4 (67.872) (42,615) [.340 - .382] [3/4] --- --- 2297684-[ ] 30° 2844065-2 55.50 34.30 10.79 – 11.94 20.57 2844430-1 2300538-[ ] 2300882-[ ] --- 1/0 2 (107,464) (66,500) (.425 - .470) [.810] 2844430-2 1976441-1 1958058-[ ] 1958080-[ ] --- --- --- 2217855-1 1958060-[ ] 15° 71.30 12.70-14.58 --- --- 2/0 --- --- 1976441-1 2290515-[ ] 30° (138,168) [.500-.574] 1976441-1 --- --- 2221881-[ ] 30° --- --- 2280034-1 58422-1 1958091-[ ] --- 1958093-[ ] 15° --- --- 1976442-1 1752787-1 87.20 13.21-16.08 25.40 3/0 (168,872) [.520-.633] [1] 68.60 1976442-1 --- 2300872-[ ] --- 2/0 (133,000) 2844425-2 1976443-1 1958054-[ ] 1958078-[ ] --- --- --- 2280035-1 1958056-[ ] 15° 110.94 14.99-17.35 --- --- 4/0 --- --- 1976443-1 2290514-[ ] 30° (214,928) [.590-.683] 1976443-1 --- --- 2221742-[ ] 30° --- --- 2217781-1 107.23 14.99-17.27 25.40 1976443-1 --- 2300884-[ ] --- --- --- 4/0 (211,678) [.590-.680] [1] 2280035-1 Table 2 (Cont’d) Flag Terminal Wire Die Crimping Aluminum Copper Strip Length B (Wire) Straight 90° Bend Insulation Range Assy Head 2 2 ±1.59 [1/16] mm (CMA)† AWG mm (CMA)† AWG 58422-1 55.50 34.30 11.18-13.03 25.40 69066 696931-[ ] 696933-[ ] 1/0 2 68010-2 (107,464) (66,500) [.440-.513] [1] 1752787-1 1752877-1 696925-[ ] 71.30 53.90 12.45-14.58 20.57 696927-[ ] 2/0 1/0 68011-1 55982-[ ] (138,168) (104,500) [.490-.574] [.810] 58422-1 110.94 85.94 15.21-17.35 25.40 1752787-1 696910-[ ] 696912-[ ] 4/0 3/0 314948-1 (214,928) (166,500) [.599-.683] [1] †For Reference Only ●Break-Away Terminal Die Assembly with Straighteners ▲Low Pressure Crimp Die Set Table 2 (End) The preferred method is: 1. Before each crimp, apply a spray dry lubricant to the crimping area of the dies to reduce sticking of the terminal in the dies. 2. Insert the properly stripped wire fully into the wire barrel of the terminal. Ensure that there are no exposed strands. CAUTION DO NOT turn or twist the wire or terminal during wire insertion; otherwise, the internal screen of the terminal could turn and cut into the wires during crimping. 3. Position the terminal in the stationary die (nest) with the back of the tongue resting against the die, with the crimping head yoke closed and pin fully inserted. NOTE Make sure terminal is positioned so crimper of the moving die (anvil) will crimp the wire barrel of the terminal. See Figure 3. 5 of 12 Rev CP 408-2281 Yoke Terminal Tongue Resting Against Side of Die Pin Fully Inserted Crimper of Moving Die (Anvil) Positioned to Crimp Wire Barrel of Terminal Figure 3 4. Holding the wire in place and fully inserted, activate the power unit to complete the crimp. 5. Remove the crimped terminal from the die assembly. When removing a terminal from the die assembly, grip it as shown in Figure 4. NOTE If terminal sticks in die after crimping, apply a rocking action to free it. Wipe light oil or use spray dry lubricant on dies to prevent sticking. When Removing, Grip Terminal Between Die Assembly and Terminal Cutout Die Assembly Terminal Cutout Figure 4 An alternate method is: NOTE This method is only slightly different than the preferred method. The difference is when the wire is inserted into the wire barrel. 1. Before each crimp, apply a spray dry lubricant to the crimping area of the dies to reduce sticking of the terminal in the dies. 2. Position the terminal in the stationary die (nest) with back of tongue resting against die, with the crimping head yoke closed and pin fully inserted. NOTE Make sure terminal is positioned so crimper of the moving die (anvil) will crimp the wire barrel of the terminal. See Figure 3. 3. Jog the power unit to advance the ram to hold the terminal in place. Make sure not to deform the wire barrel; otherwise, it may be difficult to insert the wire into the wire barrel of the terminal. 6 of 12 Rev CP 408-2281 4. Insert the properly stripped wire fully into the wire barrel of the terminal. Ensure that there are no exposed strands. CAUTION DO NOT turn or twist the wire or terminal during wire insertion; otherwise, the internal screen of the terminal could turn and cut into the wires during crimping. 5. Holding the wire in place and fully inserted, activate the power unit to complete the crimp. 6. Remove the crimped terminal from the die assembly. When removing a terminal from the die assembly, grip it as shown in Figure 4. NOTE If terminal sticks in die after crimping, apply a rocking action to free it. Wipe light oil or use spray dry lubricant on dies to prevent sticking. 4.2. Splice IMPORTANT: To ensure a quality crimp, gage the die assembly at the beginning of a run, after changing a die assembly — and then periodically during the run. Refer to Paragraph 6.2 for gaging instructions. The preferred method is: 1. Before each crimp, apply a spray dry lubricant to the crimping area of the dies to reduce sticking of the splice in the dies. 2. Insert the properly stripped wire fully into the wire barrel of the splice. When crimping a splice with a color-coded band, insert the correct copper wires into the color-coded banded end of the splice. Ensure that there are no exposed strands. CAUTION DO NOT turn or twist the wire or splice during wire insertion; otherwise, the internal screen of the splice could turn and cut into the wires during crimping. 3. Position the splice in the stationary die (nest) so that edge of the die is within the width of the circumferential crimp alignment mark of the splice. The asterisk alignment mark on the splice must be inside the die, facing up, and in alignment with the alignment dot of the die. See Figure 5. NOTE Make sure that the splice is properly aligned in the stationary die (nest) so that the moving die (anvil) will crimp the wire barrel of the splice. 4. Holding the wire in place, activate the power unit to complete the first wire barrel crimp. 5. When the first wire barrel crimp is completed, remove the crimping head pin, open the yoke, and remove the splice. 6. To crimp the other wire barrel of the splice, rotate the splice or crimping head 180 degrees, and position the splice in the die so that the asterisk alignment mark on the splice is inside the die, facing up, and in alignment with alignment dot of the die. See Figure 5. Follow the same steps used to crimp the first wire barrel (Steps 1 through 5). An alternate method is: NOTE This method is only slightly different than the preferred method. The difference is when the wire is inserted into the wire barrel. 1. Before each crimp, apply a spray dry lubricant to the crimping area of the dies to reduce sticking of the splice in the dies. 2. Position the splice in the stationary die (nest) so that edge of the die is within the width of the circumferential crimp alignment mark of the splice. The asterisk alignment mark on the splice must be inside the die, facing up, and in alignment with the alignment dot of the die. See Figure 5. 7 of 12 Rev CP 408-2281 Edge of Anvil (Moving Die) within Width of Circumference Crimp Alignment Knurl of Splice Die Alignment Dot Asterisk Alignment Wire Mark of Splice Pin Die Alignment Dot Circumferential Crimp Alignment Knurl of Splice Anvil (Moving Die) Figure 5 3. Jog the power unit to advance the ram to hold the splice in place. Make sure not to deform the wire barrel; otherwise, it may be difficult to insert the wire into the wire barrel of the splice. 4. Insert the properly stripped wire fully into wire barrel of the splice. When crimping a splice with a color-coded band, insert the correct copper wires into the color-coded banded end of the splice. Ensure that there are no exposed strands. CAUTION DO NOT turn or twist the wire or splice during wire insertion; otherwise, the internal screen of the splice could turn and cut into the wires during crimping. 5. Holding the wire in place, activate the power unit to complete the other wire barrel crimp. 6. When the wire barrel crimp is completed, remove the crimping head pin, open yoke, and remove the splice. 7. To crimp the other wire barrel of the splice, rotate the splice or crimping head 180 degrees, and position the splice in the die so that the asterisk alignment mark on the splice is inside the die, facing up, and in alignment with alignment dot of the die. See Figure 5. Follow the same steps used to crimp the first wire barrel (Steps 1 through 5). 5. CRIMP INSPECTION Refer to Application Specification 114-2134 for detailed criteria to check that crimp is applied properly. The crimp inspection mark (created by the die assembly) on the terminal or splice can be used as a visual indicator of an acceptable termination, but it does not indicate that the crimp is not acceptable. If the crimp inspection mark is centered in the crimp area and is evenly and distinctly formed, the crimp is considered properly applied; however, if it is not: — refer to Table 2 to verify that the proper terminal or splice and die combination according to the wire size was used, — verify that the dies fully bottom during the crimp cycle, and — ensure that the die assembly is dimensionally correct as specified in paragraph 6.2 8 of 12 Rev CP 408-2281 6. MAINTENANCE AND INSPECTION Each die assembly is inspected before shipment. It is recommended that the die assembly be inspected immediately upon arrival at your facility to ensure that it conforms to the gage dimensions provided in Figure 7 and that it has not been damaged during shipment. Keep the dies together as a complete set (assembly). DO NOT mix dies from different die assemblies or the same die assemblies. Die part numbers for each die assembly are listed in Figure 6. DANGER To avoid personal injury, ALWAYS DISCONNECT electrical and air supply to power unit before performing adjustments, inspections, or repairs. Nest (Stationary Die) (1 Per Die Assembly) Anvil (Moving Die) 97.0 [3.80] (1 Per Die Assembly) Ref Weight: 255 g [9 oz.] 44.50 [1.75] Ref Die Assembly Item 59877-1 68006 68007 68008 68008-1 68009 68010 68010-1 68010-2 68011-1 1 312309-9 312309-1 312309-2 312309-3 1-312309-4 312309-4 1-312309-0 312309-5 1-312309-1 312309-7 2 307465-9 307465-1 307465-2 307465-3 1-307465-3 307465-4 307465-5 1-307465-0 307465-5 307465-7 Die Assembly Item 314948-1 314964-1▲ 1976441-1 1976442-1 1976443-1 2217855-1 2280034-1 2280035-1 2217781-1 1 314951-1 314965-1 1-312309-2 1-312309-3 314951-2 2-312309-7 2-312309-7 314951-4 314951-4 2 307465-9 307465-7 1-307465-1 1-307465-2 1-307465-2 2-307465-8 2-307465-8 2-307465-7 2-307465-7 Die Assembly Item 2844065-1 2844065-2 2844425-2 2844430-1 2844430-2 Future 1 2-312309-8 2-312309-8 3-312309-0 2-312309-9 2-312309-9 2 2-307465-9 2-307465-9 2-307465-7 3-307465-0 3-307465-0 ▲Low Pressure Crimp Die Set Figure 6 6.1. Daily Maintenance Each operator must be made aware of - and responsible for - the following steps of daily maintenance: 1. Remove dust, dirt, and other contaminants with a clean brush or a soft, lint-free cloth. DO NOT use objects that could damage the dies. 2. Make certain the dies are protected with a thin coat of any good SAE 20 motor oil. DO NOT OIL EXCESSIVELY. 3. When the dies are not in use, mate them and store in a clean dry area. 9 of 12 Rev CP 408-2281 6.2. Gaging the Die Assembly NOTE It is highly recommended to gage the die assembly at the beginning of a run, after changing a die assembly - and then periodically during the run. Inspect the wire barrel section and insulation sealing section of the crimping chamber using plug gages that conform to the measurements provided in Figure 7 as follows: NOTE Gages can be purchased from Pennoyer-Dodge Company, 6650 San Fernando Road, Glendale, CA 91201 1. Mate the dies until it is evident they have bottomed. Hold the dies in this position. 2. Align the GO element of the plug gage with the crimping chamber. Push the element straight into the crimping chamber as shown in Figure 8. The GO element must pass completely through the crimping chamber. 3. Align the NO-GO element with the crimping chamber and try to insert it straight into the crimping chamber. The NO-GO element may start to enter, but must not pass completely through, as shown in Figure 8. If the crimping chamber conforms to the gage inspection, the die assembly is considered dimensionally correct. If not, the die assembly must be replaced. 6.3. Periodic Inspection Regular inspections should be performed by quality control personnel. A record of scheduled inspections should remain with the dies and/or be supplied to personnel responsible for the dies. Although recommendations call for at least one inspection per month, the inspection frequency should be based on the amount of use, ambient working conditions, operator training and skill, and established company standards. This inspection should be performed as follows: 1. Remove all lubrication and accumulated film by immersing the die assembly in a suitable commercial degreaser that will not affect the painted alignment dots. 2. Inspect the crimp area for flattened, chipped, cracked, worn, or broken areas. If damage is evident, the die assembly must be replaced. 7. REPLACEMENT AND REPAIR Order die assemblies through your TE Representative or call 1-800-526-5142, or send a facsimile of your purchase order to 1-717-986-7605, or write to: CUSTOMER SERVICE (038-035) TE CONNECTIVITY CORPORATION PO BOX 3608 HARRISBURG PA 17105-3608 Die assemblies may be returned for evaluation and repair. For repair service, call 1-800-526-5136. 10 of 12 Rev CP 408-2281 Gage Element W C Die Wire Barrel Section Insulation Sealing Section Tip (Exposed Assy Width R (Radius) R (Radius) Length) GO NO-GO GO NO-GO (max) (max) (max) 7.518-7.526 7.769-7.772 16.205-16.213 16.609-16.612 9.91 16.15 59877-1 7.62 [.300] 8.08 [.318] [.2960-.2963] [.3059-.3060] [.6380-.6383] [.6539-.6540] [.390] [.636] 2.870-2.877 3.045-3.048 6.248-6.256 6.652-6.655 6.35 6.20 68006 3.18 [.125] 3.10 [.122] [.1130-.1133] [.1199-.1200] [.2460-.2463] [.2619-.2620] [.250] [.244] 3.200-3.208 3.375-3.378 3.556 7.518-7.526 7.922-7.925 6.35 7.47 68007 3.73 [.147] [.1260-.1263] [.1329-.1330] [.140] [.2960-.2963] [.3119-.3120] [.250] [.294] 68008 3.937-3.945 4.112-4.115 9.195-9.202 9.599-9.601 6.35 9.14 4.34 [.171] 4.57 [.180] 68008-1 [.1550-.1553] [.1619-.1620] [.3620-.3623] [.3779-.3780] [.250] [.360] 5.003-5.011 5.179-5.181 11.379-11.387 11.783-11.786 9.91 11.33 68009 5.54 [.218] 5.66 [.223] [.1970-.1973] [.2039-.2040] [.4480-.4483] [.4639-.4640] [.390] [.446] 2844065-1 5.003-5.011 5.179-5.181 11.379-11.387 11.783-11.786 9.91 11.33 5.54 [.218] 5.66 [.223] 2844065-2 [.1970-.1973] [.2039-.2040] [.4480-.4483] [.4639-.4640] [.390] [.446] 68010 6.197-6.205 6.372-6.375 13.818-13.825 14.221-14.224 9.91 13.77 6.73 [.265] 6.88 [.271] 68010-1 [.2440-.2443] [.2509-.2510] [.5440-.5443] [.5599-.5600] [.390] [.542] 6.579-6.586 6.754-6.756 13.818-13.825 14.221-14.224 9.91 13.77 68010-2 6.73 [.265] 6.88 [.271] [.2590-.2593] [.2659-.2660] [.5440-.5443] [.5599-.5600] [.390] [.542] 7.924-7.932 8.100-8.102 15.037-15.044 15.441-15.443 9.91 14.99 68011-1 7.52 [.296] 7.49 [.295] [.3120-.3123] [.3189-.3190] [.5920-.5923] [.6079-.6080] [.390] [.590] 9.550-9.558 9.802-9.804 16.205-16.213 16.609-16.612 9.91 16.15 314948-1 8.13 [.320] 8.08 [.318] [.3760-.3763] [.3859-.3860] [.6380-.6383] [.6539-.6540] [.390] [.636] 10.922-10.930 11.097-11.100 15.037-15.044 15.441-15.443 9.91 14.99 314964-1▲ 7.52 [.296] 7.49 [.295] [.4300-.4303] [.4369-.4370] [.5920-.5923] [.6079-.6080] [.390] [.590] 7.924-7.932 8.100-8.102 15.037-15.044 15.441-15.443 9.91 14.99 1976441-1 7.52 [.296] 7.49 [.295] [.3120-.3123] [.3189-.3190] [.5920-.5923] [.6079-.6080] [.390] [.590] 7.518-7.526 7.769-7.772 16.205-16.213 16.609-16.612 9.91 16.15 1976442-1 7.62 [.300] 8.08 [.318] [.2960-.2963] [.3059-.3060] [.6380-.6383] [.6539-.6540] [.390] [.636] 9.550-9.558 9.802-9.804 16.205-16.213 16.609-16.612 9.91 16.15 1976443-1 8.13 [.320] 8.08 [.318] [.3760-.3763] [.3859-.3860] [.6380-.6383] [.6539-.6540] [.390] [.636] 7.924-7.932 8.100-8.102 15.037-15.044 15.441-15.443 9.91 14.99 2217855-1 7.52 [.296] 7.49 [.295] [.3120-.3123] [.3189-.3190] [.5920-.5923] [.6079-.6080] [.390] [.590] 9.550-9.558 9.802-9.804 16.205-16.213 16.609-16.612 9.91 16.15 2217781-1 8.13 [.320] 8.08 [.318] [.3760-.3763] [.3859-.3860] [.6380-.6383] [.6539-.6540] [.390] [.636] 7.924-7.932 8.100-8.102 15.037-15.044 15.441-15.443 9.91 14.99 2280034-1 7.52 [.296] 7.49 [.295] [.3120-.3123] [.3189-.3190] [.5920-.5923] [.6079-.6080] [.390] [.590] Figure 7 (Cont’d) 11 of 12 Rev CP 408-2281 Gage Element W Die Wire Barrel Section Insulation Sealing Section C Tip Width Assy (Exposed Length) R (Radius) R (Radius) (max) GO NO-GO GO NO-GO (max) (max) 9.550-9.558 9.802-9.804 8.13 16.205-16.213 16.609-16.612 8.08 9.91 16.15 2280035-1 [.3760-.3763] [.3859-.3860] [.320] [.6380-.6383] [.6539-.6540] [.318] [.390] [.636] 7.518-7.526 7.769-7.772 7.62 16.205-16.213 16.609-16.612 8.08 9.91 16.15 2844425-2 [.2960-.2963] [.3059-.3060] [.300] [.6380-.6383] [.6539-.6540] [.318] [.390] [.636] 6.197-6.205 6.372-6.375 6.73 13.818-13.825 14.221-14.224 6.88 9.91 13.77 2844430-[ ] [.2440-.2443] [.2509-.2510] [.265] [.5440-.5443] [.5599-.5600] [.271] [.390] [.542] ▲Low Pressure Crimp Die Set Figure 7 (End) Figure 8 8. REVISION SUMMARY Revisions to this instruction sheet include: Table 2 (277 Series): Added P/Ns 2325332-[] and 2327315-[] to the 3/0 bent column 12 of 12 Rev CP
Frequently asked questions
How does Electronics Finder differ from its competitors?

Is there a warranty for the 68011-1?

Which carrier will Electronics Finder use to ship my parts?

Can I buy parts from Electronics Finder if I am outside the USA?

Which payment methods does Electronics Finder accept?

Why buy from GID?
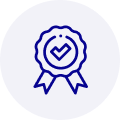
Quality
We are industry veterans who take pride in our work
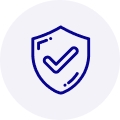
Protection
Avoid the dangers of risky trading in the gray market
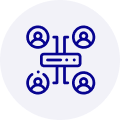
Access
Our network of suppliers is ready and at your disposal
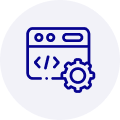
Savings
Maintain legacy systems to prevent costly downtime
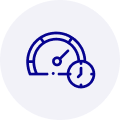
Speed
Time is of the essence, and we are respectful of yours
What they say about us
FANTASTIC RESOURCE
One of our top priorities is maintaining our business with precision, and we are constantly looking for affiliates that can help us achieve our goal. With the aid of GID Industrial, our obsolete product management has never been more efficient. They have been a great resource to our company, and have quickly become a go-to supplier on our list!
Bucher Emhart Glass
EXCELLENT SERVICE
With our strict fundamentals and high expectations, we were surprised when we came across GID Industrial and their competitive pricing. When we approached them with our issue, they were incredibly confident in being able to provide us with a seamless solution at the best price for us. GID Industrial quickly understood our needs and provided us with excellent service, as well as fully tested product to ensure what we received would be the right fit for our company.
Fuji
HARD TO FIND A BETTER PROVIDER
Our company provides services to aid in the manufacture of technological products, such as semiconductors and flat panel displays, and often searching for distributors of obsolete product we require can waste time and money. Finding GID Industrial proved to be a great asset to our company, with cost effective solutions and superior knowledge on all of their materials, it’d be hard to find a better provider of obsolete or hard to find products.
Applied Materials
CONSISTENTLY DELIVERS QUALITY SOLUTIONS
Over the years, the equipment used in our company becomes discontinued, but they’re still of great use to us and our customers. Once these products are no longer available through the manufacturer, finding a reliable, quick supplier is a necessity, and luckily for us, GID Industrial has provided the most trustworthy, quality solutions to our obsolete component needs.
Nidec Vamco
TERRIFIC RESOURCE
This company has been a terrific help to us (I work for Trican Well Service) in sourcing the Micron Ram Memory we needed for our Siemens computers. Great service! And great pricing! I know when the product is shipping and when it will arrive, all the way through the ordering process.
Trican Well Service
GO TO SOURCE
When I can't find an obsolete part, I first call GID and they'll come up with my parts every time. Great customer service and follow up as well. Scott emails me from time to time to touch base and see if we're having trouble finding something.....which is often with our 25 yr old equipment.
ConAgra Foods