OMRON AUTOMATION F3SJ-E0625P25
Specifications
Manufacturer
Omron Automation
Manufacturers Part #
F3SJ-E0625P25
Industry Aliases
F3SJ-E0625P25
Sub-Category
Specialized Sensors
Factory Pack Quantity
1
Datasheet
Extracted Text
Safety Light Curtains F3SJE F3SJ-E For full product information, visit www.sti.com. Use the SpeedSPEC Code for quick access to the specific web page. Safety Light Curtains • Fast and easy installation • Resolution: 25 mm (1.01 in.) • Range: 7 m (23 ft.) • Protected heights: 185 to 1105 mm (7.28 to 43.50 in.) • Very compact size: 30 x 30 mm (1.18 x 1.18 in.) • Cross-talk prevention • 3 m integrated cables • A Rapid Delivery Product: Select models are available for shipment today or within 3 to 5 days Description The EASY type safety light curtain is well suited for straight- Global Support forward on/off detection applications. Omron will support you through the our global network. By carefully selecting the available functions, we have reduced man hours necessary for installation by approximately 1/2 when compared with existing STI models. Reduced installation time means added savings to your project’s budget, start with the EASY type. Machine safety I only need first, narrowed simple functions down to the simplest Global Support functions: Upon detection of personnel, the machine stops. Easy-to-view Diagnostics Simple yet very These indicators enable you to intuitively know the status optimal. and cause of any error. This allows faster installation while reducing machine down time. 1/2 the mounting time. Fixed response time makes calculation of the safety distance easier. Reduced wiring, quick mount brackets and easy-to-view alignment beams all add up to cost savings. Additionally, with one fixed response time, it is now easier to calculate the safety distance. Easy-to-View Diagnostics mounting time Existing E type Mounting Time models Select models are available for Rapid Delivery. Visit this product on www.sti.com for details. www.sti.com/info Safety Light Curtain F3SJ-E EASY type reduces implementation costs with 1/2 the mounting time. • In pursuit of simple functions: Upon detection of personnel, Related Dimensions : Page 54 to 60 Function List : Page 97 to 97 information the machine stops. Safety Precautions : Page 99 Precautions on Safety : Page 100 to 104 Can be used for simple hand intrusion detection. Implementation costs can be significantly reduced. Ordering Information Main Units Safety Light Curtain Model Detection Protective height Application Beam gap Operating range capability (mm) PNP output NPN output F3SJ-E@@@@P25 Hand protection Dia. 25 mm 20 mm 0.2 to 7 m 185 to 1,105 F3SJ-E@@@@N25 *1 Note: F3SJ-E uses a 3 m prewired discrete cable. *1. For S-mark compatible model, the suffix "-S" is added to the model name. (Example) F3SJ-E0185P25-S Safety Light Curtain Model List Please contact our sales representative. F3SJ-E Series (20 mm pitch) Model Number of beams Protective height [mm] *2 PNP output *1 NPN output F3SJ-E0185P25 F3SJ-E0185N25 8185 F3SJ-E0225P25 F3SJ-E0225N25 10 225 F3SJ-E0305P25 F3SJ-E0305N25 14 305 F3SJ-E0385P25 F3SJ-E0385N25 18 385 F3SJ-E0465P25 F3SJ-E0465N25 22 465 F3SJ-E0545P25 F3SJ-E0545N25 26 545 F3SJ-E0625P25 F3SJ-E0625N25 30 625 F3SJ-E0705P25 F3SJ-E0705N25 34 705 F3SJ-E0785P25 F3SJ-E0785N25 38 785 F3SJ-E0865P25 F3SJ-E0865N25 42 865 F3SJ-E0945P25 F3SJ-E0945N25 46 945 F3SJ-E1025P25 F3SJ-E1025N25 50 1,025 F3SJ-E1105P25 F3SJ-E1105N25 54 1,105 *1. For S-mark compatible model, the suffix "-S" is added to the model name. (Example) F3SJ-E0185P25-S *2. Protective height (mm) = Total sensor length 2 F3SJ-E Accessories (Sold separately) Relays with Forcibly Guided Contacts Type Appearance Specifications Model Remarks • Nodes: 4 Contact type: 2A2B G7SA-2A2B Rated switch load: For details on other models or 250 VAC 6A, 30 VDC 6A G7SA Relays with socket models, refer to the Forcibly Guided ContactsNodes: 4 OMRON's website. Contact type: 3NO+1NC G7SA-3A1B Rated switch load: 250 VAC 6A, 30 VDC 6A Nodes: 6 Contact type: 4NO+2NC G7S-4A2B-E Rated switch load: For details on other models or 250 VAC 10 A, 30 VDC 10 A G7S-@-E Relays with socket models, refer to the Forcibly Guided ContactsNodes: 6 OMRON's website. Contact type: 3NO+3NC G7S-3A3B-E Rated switch load: 250 VAC 10 A, 30 VDC 10 A Laser Pointer Appearance Output Model Laser Pointer for F3SJ F39-PTJ Spatter Protection Cover (2 cables per set, common for emitter/receiver) (10% Operating Range Attenuation) Appearance Model F39-HB@@@@ * *The same 4-digit numbers as the protective heights (@@@@ in the light curtain model names) are substituted by in the model names. Protective Bar Appearance Model Remarks 2 Light Curtain brackets 4 mounting brackets 0 to 4 intermediate brackets for backside mounting F39-PB@@@@ *1 (quantity required for the sensing width) 0 to 4 intermediate br ackets for mounting to the sides (quantity required for the sensing width) 1 Light Curtain bracket 2 mounting brackets 0 to 2 intermediate brackets for backside mounting F39-PB@@@@-S *1 *2 (quantity required for the sensing width) 0 to 2 intermediate br ackets for mounting to the sides (quantity required for the sensing width) Note: The following are not provided with the Protective Bars. • Safety Light Curtain • Safety Light Curtain Top/Bottom Brackets • Wall Mounting Screw Unit *1. The same four digits indicating protective height that are used in the Sensor model number (@@@@) are used in the part of the Protector model number. *2. Purchase the F39-PB@@@@ (which contains two sets of brackets) to use Protective Bars for both the Emitter and Receiver. Test rod Diameter Model 14mm dia. F39-TRD14 20mm dia. F39-TRD20 25mm dia. F39-TRD25 30mm dia. F39-TRD30 3 F3SJ-E Mirrors (12% Operating Range Attenuation) Appearance Mirror material Width (mm) Thickness (mm) Length (mm) Model Remarks 406 F39-MLG0406 610 F39-MLG0610 711 F39-MLG0711 914 F39-MLG0914 2 sets of Cylindrical 1,067 F39-MLG1067 Glass mirror 145 32 mounting rod, 1,219 F39-MLG1219 4 screws are included. 1,422 F39-MLG1422 1,626 F39-MLG1626 1,830 F39-MLG1830 2,134 F39-MLG2134 Sensor Mounting Bracket (Sold separately) Appearance Specifications Model Application Remarks 2 for an emitter, Top/bottom bracket F39-LJB1 Top/bottom bracket for F3SJ-E/B 2 for a receiver, total of 4 per set In combination use with top/bottom bracket for F3SJ-E/B Intermediate bracket F39-LJB2 *1 *2 1 set with 2 pieces Can be used as free-location bracket. Quick mount bracket for F3SJ-E/B F39-LJB3-M6 *1 Supports M6 slide nut for aluminum frame. Quick mount bracket 1 set with 2 pieces Quick mount bracket for F3SJ-E/B F39-LJB3-M8 *2 Supports M8 slide nut for aluminum frame. Hexagon socket head cap F39-LJB3-M6K *1 screws (M6 x 10) are Quick mount M6 included. Bracket to mount an intermediate bracket bracket to the aluminum frame with Quick mount M8 Hexagon socket head cap a single touch. bracket F39-LJB3-M8K *2 screws (M8 x 14) are included. Mounting bracket used when 2 for an emitter, Compatible mounting F39-LJB4 replacing existing area sensors 2 for a receiver, bracket (F3SJ-A or F3SN) with the F3SJ-E/B. total of 4 per set 2 for an emitter, Bracket to closely contact the back Contact mount bracket F39-LJB5 2 for a receiver, side of the Sensor. total of 4 per set Note: All the sensor mounting brackets for F3SJ-E are sold separately. *1. Combining F39-LJB2 and F39-LJB3-M6K makes F39-LJB3-M6. *2. Combining F39-LJB2 and F39-LJB3-M8K makes F39-LJB3-M8. 4 F3SJ-E Specifications (For details, refer to the instruction manual or User's manual.) Main Units F3SJ-E@@@@P25/N25 PNP output F3SJ-E@@@@P25 Model NPN output F3SJ-E@@@@N25 Sensor type Type 4 safety light curtain Setting tool connection *1 Parameter settings: Not available Safety category Safety purpose of category 4, 3, 2, 1, or B Detection capability Opaque objects 25 mm in diameter Beam gap (P) 20 mm Number of beams (n) 8 to 54 Protective height (PH) 185 to 1,105 mm Lens diameter Diameter 5 mm Operating range *2 0.2 to 7 m Response time ON to OFF 15 ms max. (under stable light OFF to ON 70 ms max. incident condition) Startup waiting time 2 s max. Power supply voltage (Vs) SELV/PELV 24 VDC±20% (ripple p-p 10% max.) Emitter : Up to 22 beams: 41 mA max., 26 to 42 beams: 57 mA max., 46 to 54 beams: 63 mA max. PNP output Consumption Receiver : Up to 22 beams: 42 mA max., 26 to 42 beams: 47 mA max., 46 to 54 beams: 51 mA max. current Emitter : Up to 22 beams: 41 mA max., 26 to 42 beams: 57 mA max., 46 to 54 beams: 63 mA max. (no load) NPN output Receiver : Up to 22 beams: 40 mA max., 26 to 42 beams: 45 mA max., 46 to 54 beams: 48 mA max. Light source (emitted wavelength) Infrared LED (870 nm) Effective aperture angle (EAA) Based on IEC 61496-2. Within ±2.5° for both emitter and receiver when the detection distance is 3 m or over Two PNP transistor outputs, load current 200 mA max., residual voltage 2 V max. (except for voltage drop due to PNP output cable extension), Leakage current 1 mA max., load inductance 2.2 H max. *3, Maximum capacity load 1 μF *4 Safety outputs (OSSD) Two NPN transistor outputs, load current 200 mA max., residual voltage 2 V max. (except for voltage drop due to NPN output cable extension), Leakage current 1 mA max., load inductance 2.2 H max. *3, Maximum capacity load 1 μF *4 Output operation mode Safety output: On when receiving light PNP output ON voltage: Vs-3 V to Vs OFF voltage: 0 V to 1/2 Vs or open *5 Input voltage NPN output ON voltage: 0 V to 3 V OFF voltage: 1/2 Vs to Vs or open *5 Mutual interference Mutual interference prevention algorithm prevents interference in up to 3 sets. prevention function Self test (at power-ON and at power distribution) Test function External test (emission stop function by test input) Protection circuit Output short-circuit protection, and power supply reverse polarity protection Ambient temperature Operating: -10 to 55°C (non-freezing), Storage: -25 to 70°C Ambient humidity Operating: 35% to 85% (no condensation), Storage: 35% to 95% RH Operating ambient light intensity Incandescent lamp: 3,000 lx max., Sunlight: 10,000 lx max. Insulation resistance 20 MΩ min. (at 500 VDC) Dielectric strength 1,000 VAC 50/60 Hz, 1 min Degree of protection IP65 (IEC 60529) Vibration resistance Malfunction: 10 to 55 Hz, Multiple amplitude of 0.7 mm, 20 sweeps in X, Y, and Z directions 2 Shock resistance Malfunction: 100 m/s , 1,000 times each in X, Y, and Z directions Pollution degree Pollution degree 3 (IEC 60664-1) Connection method: Pull-out type, cable length 3 m Number of wires: Emitter: 5 wires, receiver: 6 wires Power cable Cable diameter: Dia. 6 mm Allowable bending radius: R5 mm Extension cable 30 m max. *6 Case: Aluminum Cap: ABS resin, PBT Material Optical cover: PMMA resin (acrylic) Cable: Oil resistant PVC Weight (packed state) Weight (g) = (protective height) x 2.6 + 800 Accessories Instruction Manual, User's Manual (CD-ROM) *7 IEC 61496-1, EN 61496-1, UL 61496-1, Type 4 ESPE (Electro-Sensitive Protective Equipment) IEC 61496-2, CLC/TS 61496-2, UL 61496-2, Type 4 AOPD (Active Opto-electronic Protective Devices) Applicable standards IEC 61508-1 to -3, EN 61508-1 to -3 SIL3 ISO 13849-1: 2006, EN ISO 13849-1: 2008 (PLe/Safety Category 4) UL 508, UL 1998, CAN/CSA C22.2 No.14, CAN/CSA C22.2 No.0.8 *1. Do not use the Support Software and Setting Console for F3SJ-A. Operation cannot be guaranteed. *2. Use of the Spatter Protection Cover causes a 10% maximum sensing distance attenuation. *3. The load inductance is the maximum value when the safety output frequently repeats ON and OFF. When you use the safety output at 4 Hz or less, the usable load inductance becomes larger. *4. These values must be taken into consideration when connecting elements including a capacitive load such as capacitor. *5. The Vs indicates a voltage value in your environment. *6. To extend a cable of the F3SJ-E, refer to the User's Manual (SCHG-733/732). *7. Mounting brackets are sold separately. 5 F3SJ-E Indicator Emitter Name of indicator Label ON Blinking Turns ON when the top beam is receiving Top-beam-state indicator TOP --- light. Turns ON when incidence level is more than Blinks when the safety output is turned OFF Stable-state indicator STB 170% of the output ON threshold. due to disturbance light or vibration. ON Green: Turns ON when safety output is ON. Red: Blinks when the F3SJ-E enters a lockout ON/OFF-state indicator OFF Red: Turns OFF when safety output is OFF. due to a safety output error. Turns ON when the F3SJ-E enters a lockout Blinks when the F3SJ-E enters a lockout on Lockout indicator LOCKOUT on the receiver. the emitter. Blinks when the F3SJ-E enters a lockout due Power indicator POWER Turns ON while the power of the emitter is ON. to power voltage/noise. Test indicator TEST --- Blinks when external test is being performed. Turns ON when the bottom beam is receiving Bottom-beam-state indicator BTM --- light. Receiver Name of indicator Label ON Blinking Turns ON when the top beam is receiving Top-beam-state indicator TOP --- light. Turns ON when incidence level is more than Blinks when the safety output is turned OFF Stable-state indicator STB 170% of the output ON threshold. due to disturbance light or vibration. ON Green: Turns ON when safety output is ON. Red: Blinks when the F3SJ-E enters a lockout ON/OFF-state indicator OFF Red: Turns OFF when safety output is OFF. due to a safety output error. Turns ON when the F3SJ-E enters a lockout Blinks when the F3SJ-E enters a lockout on Lockout indicator LOCKOUT on the emitter. the receiver. Blinks when the F3SJ-E enters lockout due to Turns ON when communication between Communication indicator COM a communication error between receiver and emitter and receiver is established. emitter. Blinks when the F3SJ-E enters lockout due to Configuration indicator CFG --- a model type error between receiver and emitter. Blinks when the F3SJ-E enters a lockout due Internal error indicator INTERNAL --- to an internal error. Turns ON when the bottom beam is receiving Bottom-beam-state indicator BTM --- light. Accessories Laser Pointer Item Model F39-PTJ Applicable sensor F3SJ Series Power supply voltage 4.65 or 4.5 VDC Battery Three button batteries (SR44 or LR44) Battery life * SR44: 10 hours of continuous operation, LR44: 6 hours of continuous operation Light source Red semiconductor laser (wavelength: 650 nm, 1 mW max. JIS class 2, EN/IEC class 2, FDA class II) Spot diameter (typical value) 6.5 mm at 10 m Ambient temperature Operating: 0 to 40°C Storage: -15 to 60°C (with no icing or condensation) Ambient humidity Operating and storage: 35% to 85% (with no condensation) Material Laser module case: aluminum Mounting bracket: aluminum and stainless Weight Approx. 220 g (packed) Accessories Laser safety standard labels (EN: 1, FDA: 3) Button batteries (SR44: 3), instruction manual * Battery life varies depending on a battery used. 6 F3SJ-E Connections Basic Wiring Diagram Minimum wiring required to check the operation of the F3SJ-E[PNP Output] (Gray) Communication line (+) (Pink) Communication line (−) +24 VDC Power Note: This circuit diagram is used for operation check. supply For an actual circuit example, refer to page 23. 0 V Minimum wiring required to check the operation of the F3SJ-E[NPN Output] (Gray) Communication line (+) (Pink) Communication line (−) +24 VDC Power Note: This circuit diagram is used for operation check. supply For an actual circuit example, refer to page 23. 0 V 7 0 V (Blue) 0 V (Blue) Test input (Black) Test input (Black) Open Open Emitter Emitter +24 V (Brown) +24 V (Brown) +24 V (Brown) +24 V (Brown) Safety output 1 (Black) Safety output 1 (Black) Open Open Receiver Receiver Safety output 2 (White) Safety output 2 (White) Open Open 0 V (Blue) 0 V (Blue) F3SJ-E Input/Output Circuit Diagram [PNP Output] Entire Circuit Diagram Input circuit diagram by function Indicator +24 VDC Brown +24 VDC Black Test input Test Input Short circuit current 3 mA Circuit Emitter Emitter Main Circuit Main Circuit 0 V Blue Gray Pink Communication line (+) Communication line (-) Gray Pink Brown Receiver White Safety output 2 Main Circuit 2 Load Safety output 1 Black Receiver Main Circuit 1 Load Indicator 0 V Blue [NPN Output] Entire Circuit Diagram Input circuit diagram by function Indication +24 VDC Brown +24 VDC Test Input Test input Black Circuit Emitter Emitter Main Circuit Main Circuit Short circuit current 3 mA 0 V Blue Gray Pink Communication line (+) Communication line (-) Gray Pink Brown Load Receiver Main Circuit 2 Safety output 2 White Load Black Safety output 1 Receiver Main Circuit 1 Indication Blue 0 V 8 F3SJ-E Connection Circuit Examples Wiring for single F3SJ-E application [PNP Output] PL/safety category Model Stop category Reset Safety Light Curtain F3SJ-E@@@@P25 PLe/4 equivalent 0 Manual Safety Relay G7SA Note: The above PL is only the evaluation result of the example. The PL must be evaluated in an actual application by the customer after confirming the usage conditions. z Application Overview The power supply to the motor M is turned OFF when the beam is blocked. The power supply to the motor M is kept OFF until the beams are unblocked and the reset switch S2 is pressed. +24 V KM1 +24 V +24 V Feedback loop KM2 (Gray) Communication line (+) KM1 K1 K1 (Pink) S2 Communication line (−) KM2 K2 K2 K3 K3 K1 M K3 K1 K3 K2 K3 KM1 KM2 K2 Unblocked S1 Blocked Reset switch K3 K1 K2 (S2) External test switch / +24 VDC lockout reset switch (S1) Power supply Safety output 0 V K3 N.C. contact S1 : External test/lockout reset switch (connect to 0 V if a switch is not required) K3 N.O. contact S2 : Reset switch K1, K2, K3 : Safety relay with force-guided contact (G7SA) K1,K2 N.C. contact KM1, KM2 : Safety relay with force-guided contact (G7SA) or magnetic contactor M : 3-phase motor K1,K2 N.O. contact KM1,KM2 N.C. contact KM1,KM2 N.O. contact 9 0 V (Blue) Test input (Black) Emitter +24 V (Brown) +24 V (Brown) Safety output 1 (Black) Receiver Safety output 2 (White) 0 V (Blue) F3SJ-E Wiring for single F3SJ-E application [NPN Output] PL/safety category Model Stop category Reset Safety Light Curtain F3SJ-E@@@@N25 PLe/4 equivalent 0 Manual Safety Relay G7SA Note: The above PL is only the evaluation result of the example. The PL must be evaluated in an actual application by the customer after confirming the usage conditions. z Application Overview The power supply to the motor M is turned OFF when the beam is blocked. The power supply to the motor M is kept OFF until the beams are unblocked and the reset switch S2 is pressed. +24 V K3 +24 V +24 V KM1 Feedback loop KM1 KM2 Communication line (+) (Gray) KM1 KM2 Communication line (-) (Pink) KM2 K1 K1 S2 K2 K2 M K1 K3 K3 K1 K3 K2 K3 K3 K2 S1 K1 K2 +24 VDC Unblocked Power Blocked supply 0 V 0 V Reset switch (S2) S1 : External test/lockout reset switch (connect to 24 V if a switch is not required) External test/lockout reset switch S2 : Reset switch (S1) K1, K2, K3 : Safety relay with force-guided contact (G7SA) KM1, KM2 : Safety relay with force-guided contact (G7SA) or magnetic contactor Safety output M : 3-phase motor K3 N.C. contact K3 N.O. contact K1,K2 N.C. contact K1,K2 N.O. contact KM1,KM2 N.C. contact KM1,KM2 N.O. contact 10 0 V (Blue) Test input (Black) Emitter +24 V (Brown) +24 V (Brown) Safety output 1 (Black) Receiver Safety output 2 (White) 0 V (Blue) F3SJ-E Wiring to connect a F3SJ-E with a controller G9SP [PNP Output] PL/safety category Model Stop category Reset Safety Light Curtain F3SJ-E@@@@P25 Safety Controller G9SP PLe/4 equivalent 0 Manual Safety Relay G7SA Emergency Stop Switch A165E/A22E Note: The above PL is only the evaluation result of the example. The PL must be evaluated in an actual application by the customer after confirming the usage conditions. z Application Overview The power supply to the motor M is turned OFF when the beam is blocked. The power supply to the motor M is turned OFF when the emergency stop switch is pressed. The power supply to the motor M is kept OFF until the beams are unblocked and the reset switch S2 is pressed while the emer- gency stop switch is released. S1 : Emergency stop switch (force-opening contact) (A165E, A22E) - G9SP settings S2 : Reset switch - Manual reset mode S3 : External test/lockout reset switch - Using feedback loop (connect to 0 V if a switch is not required) KM1, KM2 : Safety relay with force-guided contact (G7SA) or magnetic contactor M : 3-phase motor Unblocked (Gray) Communication line (+) Blocked (Pink) External test/lockout reset switch Communication line (−) (S3) Reset switch (S2) Emergency stop switch (S1) Safety output KM1,KM2 N.O. contact S3 KM1,KM2 N.C. contact +24 VDC Power supply 0 V V1 Si0 Si1 Si2 Si3 Si4 Si5 Si6 Si7 V2 So0 So1 G1 T0 T1 T2 T3 G2 G2 G2 KM1 KM2 +24 VDC +24 VDC Power Power 0 V supply 0 V supply KM1 11 21 GND GND KM1 KM2 KM2 12 22 S2 S1 M Feedback loop 11 0 V (Blue) Test input (Black) Emitter +24 V (Brown) +24 V (Brown) Safety output 1 (Black) Receiver Safety output 2 (White) 0 V (Blue) F3SJ-E Wiring to connect a F3SJ-E with a controller G9SA-301 [PNP Output] PL/safety category Model Stop category Reset Safety Light Curtain F3SJ-E@@@@P25 Safety Relay Unit G9SA-301 24V AC/DC PLe/4 equivalent 0 Manual Safety Relay G7SA Emergency Stop Switch A165E/A22E Note: The above PL is only the evaluation result of the example. The PL must be evaluated in an actual application by the customer after confirming the usage conditions. z Application Overview The power supply to the motor M is turned OFF when the beam is blocked. The power supply to the motor M is turned OF F when the emergency stop switch is pressed. The power supply to the motor M is kept OFF until the beams are unblocked and the reset switch S2 is pressed while the emer- gency stop switch is released. - G9SA-301 settings Wiring for auto reset mode - Manual reset mode Feedback loop - Using feedback loop - Using emergency stop switch KM1 KM2 T31 T32 (Gray) KM1 A B Communication line (+) KM2 (Pink) Communication line (−) * If an emergency stop switch is not used, connect safety output 1 to T12 terminal and safety output 2 to T23 directly. M S1: External test/lockout reset switch (connect to 0 V if a switch is not required) S2: Interlock reset switch S3: Emergency stop switch (force-opening contact) (A165E, A22E) KM1,KM2: Safety relay with force-guided contact (G7SA) or magnetic contactor M: 3-phase motor * 12 22 +24 VDC Unblocked Power Feedback loop 11 21 S3 supply Blocked 0 V KM1 External test/lockout reset switch (S1) KM2 Interlock reset switch A1 A2 T11 T12 T31 T32 13 23 33 41 (S2) 3 Emergency stop switch 4 1 (S3) K1 K2 a K1 Safety output 1 2 K2 3 4 K1,K2 N.O. contact a Control 2 JP K1 5 b Circuit 5 6 b K2 KM1,KM2 N.O. contact 6 K1,K2 N.C. contact PE T21 T23 T22 A B 14 24 34 42 Model G9SA-301 KM1,KM2 N.C. contact KM1 KM2 12 0 V (Blue) S1 Test input (Black) Emitter +24 V (Brown) S2 +24 V (Brown) Receiver Safety output 1 (Black) Safety output 2 (White) 0 V (Blue) F3SJ-E Wiring to connect a F3SJ-E with a controller G9SA-301-P [NPN Output] PL/safety category Model Stop category Reset Safety Light Curtain F3SJ-E@@@@N25 Safety Relay Unit G9SA-301-P 24V DC PLe/4 equivalent 0 Manual Safety Relay G7SA Emergency Stop Switch A165E/A22E Note: The above PL is only the evaluation result of the example. The PL must be evaluated in an actual application by the customer after confirming the usage conditions. z Application Overview The power supply to the motor M is turned OFF when the beam is blocked. The power supply to the motor M is turned OFF when the emergency stop switch is pressed. The power supply to the motor M is kept OFF until the beams are unblocked and the reset switch S2 is pressed while the emer- gency stop switch is released. KM1 Communication KM2 line (+) (Grey) Communication line (-) (Pink) M * If an emergency stop switch is not used, connect safety output 1 to T12 terminal and safety output 2 to T23 directly. S1 : External test/ lockout reset switch * +24 VDC 12 22 (connect to 24 V if a switch is not required) Power Feedback loop S2 : Interlock reset switch Supply 0 V S3 : Emergency stop switch (force-opening contact) (A165E, A22E) 11 21 S3 KM1, KM2 : Safety relay with force-guided contact (G7SA) or KM1 magnetic contactor M : 3-phase motor KM2 Unblocked A1 A2 T11 T12 T31 T32 13 23 33 41 Blocked External test/lockout reset switch 3 4 (S1) 6 Interlock reset switch K1 a K2 K1 (S2) 1 2 Emergency stop switch K2 3 (S3) 4 a Control 2 JP K1 5 Safety output b 5 Circuit 6 b K2 K1,K2 N.O. contact 1 24 42 PE T21 T23 T22 A B 14 34 KM1,KM2 N.O. contact Model G9SA-301-P K1,K2 N.C. contact KM1 KM2 KM1,KM2 N.C. contact Note: 1. As the G9SP Safety Controller is a PNP output type, it cannot be connected to the F3SJ-E@@@@N25. Also, a Safety Controller with PNP output cannot be connected to the F3SJ-E@@@@N25. 2. The G9SA-301-P is a safety relay unit only for NPN output. 13 0V (Blue) S1 Test input (Black) Emitter +24V (Brown) S2 +24V (Brown) Receiver Safety output 1 (Black) Safety output 2 (White) 0V (Blue) F3SJ-E/F3SJ-B/F3SJ-A Function List Functions that can be used on F3SJ are shown as follows: Refer to the F3SJ User's Manual for details. For manual number, check the "Related Manuals" at the end of the catalog. ✓: Can be used. X: Cannot be used. Basic functions Function F3SJ-E (EASY) F3SJ-B (BASIC) F3SJ-A (ADVANCED) Self-test function ✓✓✓ External test function ✓✓✓ External device monitoring function X ✓ * ✓ Interlock function X ✓ * ✓ Auxiliary output function X ✓✓ Muting function X ✓✓ * Cannot be used at muting. Functions for individual applications Override function X ✓✓ Partial muting function XX ✓ Position detection muting function XX ✓ Fixed blanking function XX ✓ Floating blanking function XX ✓ Warning zone function XX ✓ Use of setting tools XX ✓ Wiring/mounting related function Series connection function X ✓✓ Dead space less (single connection) ✓✓✓ Dead space less (series connection) XX ✓ Response time integration (15 ms) * ✓✓ X Simple wiring ✓ XX Connector cable X ✓✓ Quick mounting ✓✓ X TOP/BOTTOM indicator for beam ✓✓ X adjustment Laser Pointer ✓✓✓ * Convenient to calculate safety distance. Indicator related functions External indicator output X ✓✓ Muting error display X ✓ X Note: The specifications of the models with the suffixes "-01TS", "-02TS" or "-TS" are different. Refer to the Specifications. 14 F3SJ-E/F3SJ-B/F3SJ-A Self-test Function Fixed Blanking Function A self-test is performed to check for errors when the power is turned Fixed blanking function disables a specific beam of the F3SJ. This ON. Also, the self-test is regularly performed (within the response function keeps safety output ON even when part of machinery time) while operating. equipment exists within a detection zone. External Test Function Floating Blanking Function This function stops the emission using an external signal. It can be Floating blanking function increases the diameter of the F3SJ's used to verify that a safety system should properly stop when F3SJ is detection capability and turns OFF the safety output when multiple interrupted. objects are detected. When there is a moving object with a fixed width in the detection area that we do not want to detect, the detection External Device Monitoring Function function can be disabled. This function detects malfunctions, such as welding, in external relays Warning Zone Function (or contactors) that control the hazardous part of a machine. This function constantly monitors that a specified voltage is applied to When an individual enters, a warning lamp lights or buzzer sounds the receiver's external device monitoring input line, and the system without stopping the equipment by dividing the detection zone into the enters lockout state when an error occurs. The relay's operational detection zone and a warning zone. delay can be up to 300 ms without being evaluated as an error. Setting Tool For example, if the normally closed N.C. contact does not close within The following setting tools (sold separately) can be purchased in 0.3 s after the safety outputs turn from ON to OFF, and a specified order to change or confirm various F3SJ-A parameters. voltage is not applied to the external device monitoring line, it is F39-MC21 Setting Console evaluated as an error and the system enters a lockout state. To utilize F39-GWUM SD Manager Setting Support Software for the F3SJ this function properly, use safety relays and contactors that have force guided or mechanically linked contact structure. Series Connection Function Up to 3 sets of the F3SJ-Bs or up to 4 sets of F3SJ-As can be series- Interlock Function connected. Series connection allows them to be used as a safety light The F3SJ turns the safety outputs OFF when its power is turned on curtain, requiring only one set to be wired to a controller and or its beam is interrupted and holds this state until reset input is preventing mutual interference. applied. This state is called "interlock". Two methods can be used to reset the interlock state: "auto reset that automatically turns control outputs ON when the interrupting object is removed" and "manual reset mode that keeps control outputs OFF until a reset signal is provided, if the interrupting object is removed". Auto Reset When the interrupting object is removed from the detection zone, the safety outputs automatically turn ON. Auto reset is used on machines where a worker is not able to enter the area between the detection zone and the hazardous part of the machine. Manual Reset When a reset input is given while no interrupting object exists in a detection zone, the safety outputs turn ON. This allows the machine to be manually reset using a reset switch after ensuring safety, preventing unexpected startup. Auxiliary Output Function The auxiliary output is used to monitor the status of the F3SJ. This output can be connected to a device such as programmable controller. Muting Function Muting function temporarily disables safety function of the F3SJ, keeping safety output ON even if beams are interrupted. This makes it possible to install safety light curtains for AGV passage, enabling both safety and productivity. Override Function The override function turns the safety outputs ON when the muting start condition is not satisfied. If a workpiece stops while passing through the F3SJ, as shown below, causing a muting error, the normal state cannot be recovered unless the workpiece is removed from the muting sensors and the detection field of the F3SJ. However, the override function will mute the safety outputs of the F3SJ so that the conveyor can be restarted to move the workpiece out of the muting sensors and detection zone. Partial Muting Function Partial muting function secures safety without enabling muting except for beams when a workpiece passes. Position Detection Muting A limit switch or other means is used to detect when the robot is in a safe position, and muting is then applied. 15 F3SJ-E/F3SJ-B/F3SJ-A Safety Precautions Description shown below is only a guideline to choose a safety (4) JIS standards sensor. To use the product properly, you must read its instruction JIS B 9704-1 (type 4 ESPE), manual that comes with the product. JIS B 9704-2 (type 4 AOPD) (5) North American standards: Legislation and Standards UL 61496-1 (type 4 ESPE), 1. Application of a sensor alone cannot receive type approval UL 61496-2 (type 4 AOPD), provided by Article 44-2 of the Industrial Safety and Health Act of UL 508, UL 1998, CAN/CSA C22.2 No.14, Japan. It is necessary to apply it in a system. CAN/CSA C22.2 No.0.8 Therefore, when using the F3SJ in Japan as a "safety system for 5. The F3SJ received the following certification from the EU- pressing or shearing machines" prescribed in Article 42 of that law, accredited body, TÜV SÜD: the system must receive type approval. EC type test based on machinery directive 2. The F3SJ is electro-sensitive protective equipment (ESPE) in Type 4 ESPE (EN 61496-1), accordance with European Union (EU) Machinery Directive Index Type 4 AOPD (CLC/TS 61496-2) Annex V, Item 2. 6. The F3SJ is scheduled to received certificates of UL listing for US 3. The F3SJ-E/B is in conformity with the following standards: and Canadian safety standards from the Third Party Assessment (1) EC legislation Body UL. Machinery Directive 2006/42/EC Type 4 ESPE (UL 61496-1), EMC Directive 2004/108/EC (2) European standards Type 4 AOPD (UL 61496-2) EN 61496-1 (type 4 ESPE), 7. The F3SJ is designed according to the standards listed below. To CLC/TS 61496-2 (type 4 AOPD), make sure that the final system complies with the following EN 61508-1 through -3 (SIL3), standards and regulations, you are asked to design and use it in EN 61000-6-4, accordance with all other related standards, laws, and regulations. EN ISO 13849-1:2008 (PLe/Safety Category 4) If you have any questions, consult with specialized organizations (3) International standards such as the body responsible for prescribing and/or enforcing IEC 61496-1 (type 4 ESPE), machinery safety regulations in the location where the equipment IEC 61496-2 (type 4 AOPD), is to be used. IEC 61508-1 through -3 (SIL3), European standards: EN 415-4, EN 692, EN 693 ISO 13849-1:2006 (PLe/Safety Category 4) (4) JIS standardsUS Occupational Safety and Health Standards: OSHA 29 CFR JIS B 9704-1 (type 4 ESPE), 1910.212 JIS B 9704-2 (type 4 AOPD) US Occupational Safety and Health Standards: OSHA 29 CFR (5) North American standards: 1910.217 UL 61496-1 (type 4 ESPE), American National Standards: ANSI B11.1 to B11.19 UL 61496-2 (type 4 AOPD), UL 508, UL 1998, CAN/CSA C22.2 No.14,American National Standards: ANSI/RIA 15.06 CAN/CSA C22.2 No.0.8 Canadian Standards Association CSA Z142, Z432, Z434 SEMI Standards SEMI S2 4. The F3SJ-A is in conformity with the following standards: (1) EC legislation Machinery Directive 2006/42/EC EMC Directive 2004/108/EC (2) European standards EN 61496-1 (type 4 ESPE), CLC/TS 61496-2 (type 4 AOPD), EN61508-1 through -3 (SIL3) EN ISO 13849-1:2008 (PLe/Safety Category 4) (3) International standardsI EC 61496-1 (type 4 ESPE), IEC 61496-2 (type 4 AOPD), IEC 61508-1 through -3 (SIL3) ISO13849-1: 2006 (PLe/Safety Category 4) 16 F3SJ-E/F3SJ-B/F3SJ-A Precautions on Safety For installation Indication and meaning for safe use This instruction manual describes notification and/or waning with WARNING indication and symbols as shown below for safe use of F3SJ. This F3SJ-E F3SJ-B F3SJ-A notification describes very important details for safety. You must follow the description. Shown below are indication and symbols. Make sure to test the operation of the F3SJ after installation to verify that the F3SJ operates as intended. Make sure to stop the Indicates a potentially hazardous situation machine until the test is complete. which, if not avoided, will result in minor or Unintended function settings may cause a person to go moderate injury, or may result in serious WARNING undetected, resulting in serious injury. injury or death. Also, a serious damage on property may be caused. F3SJ-E F3SJ-B F3SJ-A Make sure to install the F3SJ at the safe distance from the If you fail to use a product properly, it may hazardous part of the equipment. Otherwise, the machine may CAUTION result in injuries or damage on property. not stop before a person reaches the hazardous part, resulting in serious injury. Meanings of Alert Symbols F3SJ-E F3SJ-B F3SJ-A Install a protective structure so that the hazardous part of a Inhibited machine can only be reached by passing through the sensor's Indicates general inhibition. detection zone. Install the sensors so that part of the person is always present in the detection zone when working in a machine's hazardous zones. If a person is able to step into the Alert Statements in this Manual hazardous zone of a machine and remain behind the 's detection F3SJ-E . . . . . Description applied to F3SJ-E models. zone, configure the system with an interlock function that prevents the machine from being restarted. Otherwise it may F3SJ-B . . . . . Description applied to F3SJ-B models. result in heavy injury. F3SJ-A . . . . . Description applied to F3SJ-A models. F3SJ-B F3SJ-A For users Install the interlock reset switch in a location that provides a WARNING clear view of the entire hazardous area and where it cannot be activated from within the hazardous area. F3SJ-E F3SJ-B F3SJ-A The FS3J must be installed, set, and integrated into the F3SJ-E F3SJ-B F3SJ-A mechanical control system by a qualified technician who has The F3SJ cannot protect a person from a projectile exiting the received the appropriate training. Failure to make correct hazardous zone. Install protective cover(s) or fence(s). settings may prevent detection of people and result in serious injury. F3SJ-A When detection of an area has been disabled by the fixed F3SJ-A blanking function, provide a protective structure around the When changing parameters with a setting tool (F39-GWUM or entire area that will prevent a person from passing through it and F39-MC21), the change must be made and the contents of the reaching the hazardous part of the machinery. Failure to do so change must be managed by the person in charge of the system. may prevent detection of people and result in serious injury. Unintentional or mistaken parameter changes may prevent detection of people and result in serious injury. F3SJ-A After setting the fixed blanking function, be sure to confirm that a test rod is detected within all areas that require detection. For machines Failure to do so may prevent detection of people and result in WARNING serious injury. F3SJ-E F3SJ-B F3SJ-A F3SJ-A Do not use this sensor for machines that cannot be stopped by When the fixed blanking function or the floating blanking electrical control. For example, do not use it for a pressing function is used, the diameter for the smallest detectable object machine that uses full-rotation clutch. Otherwise, the machine becomes larger. Be sure to use the diameter for the smallest may not stop before a person reaches the hazardous part, detectable object for the fixed blanking function or the floating resulting in serious injury. blanking function when calculating the safety distance. Failure to do so may prevent the machinery from stopping before a F3SJ-B F3SJ-A person reaches the hazardous part of the machinery, and result Do not use the auxiliary output or external indicator output for in serious injury. safety applications. Human body may not be detected when F3SJ fails, resulting in serious injury. F3SJ-B F3SJ-A The muting and override functions disable the safety functions of the device. Additional safety measures must be taken to ensure safety while these functions are working. 17 F3SJ-E/F3SJ-B/F3SJ-A F3SJ-B F3SJ-A F3SJ-E F3SJ-B F3SJ-A Install muting sensors so that they can distinguish between the Do not use the sensor system with mirrors in a regressive object that is being allowed to be pass through the detection reflective configuration. Doing so may hinder detection. It is zone and a person. If the muting function is activated by the possible to use mirrors to "bend" the detection zone to a 90- detection of a person, it may result in serious injury. degree angle. F3SJ-B F3SJ-A Muting lamps (external indicators) that indicate the state of the Reflector muting and override functions must be installed where they are clearly visible to workers from all the operating positions. F3SJ-A Muting times must be precisely set according to the application by qualified personnel who have received appropriate training. In particular, if the muting time limit is to be set to infinity, the Reflector person who makes the setting must bear responsibility. Position with detection F3SJ-B F3SJ-A zone bent at 90° Position with retro-reflection Use two independent input devices for the muting inputs. F3SJ-E F3SJ-B F3SJ-A F3SJ-B F3SJ-A When using series connections, perform inspection of all Install the F3SJ, Muting Sensors, or a protective wall so that connected F3SJs as instructed in the User's Manual. workers cannot enter hazardous areas while muting is in effect, and set muting times. For wiring F3SJ-B F3SJ-A WARNING Position the switch that is used to activate the override function in a location where the entire hazardous area can be seen, and F3SJ-E F3SJ-B F3SJ-A where the switch cannot be operated from inside the hazardous [For PNP output] Connect the load between the output and 0V line. area. Make sure that nobody is in the hazardous area before [For NPN output] activating the override function. Connect the load between the output and +24V line. If +24 V and 0 V are connected, it is dangerous because operation mode is F3SJ-E F3SJ-B F3SJ-A inversed to "ON when interrupted". Install the sensor system so that it is not affected by reflective surfaces. Failure to do so may hinder detection, resulting in F3SJ-E F3SJ-B F3SJ-A serious injury. [For PNP output] Do not short-circuit an output line to +24 V line. Otherwise, the F3SJ-E F3SJ-B F3SJ-A output is always ON. Also, 0 V of the power supply must be When using more than 1 set of F3SJ, install them so that mutual grounded so that output should not turn ON due to grounding of interference does not occur, such as by configuring series the output line. connections or using physical barriers between adjacent sets. [For NPN output] F3SJ-E F3SJ-B F3SJ-A Do not short-circuit an output line to 0 V line. Otherwise, the output is always ON. Also, +24 V of the power supply must be Make sure that the F3SJ is securely mounted and its cables and connectors are properly secured. grounded so that output should not turn ON due to grounding of the output line. F3SJ-E F3SJ-B F3SJ-A Make sure that no foreign material, such as water, oil or dust, F3SJ-E F3SJ-B F3SJ-A Configure the system by using the optimal number of safety enters the inside of the F3SJ while the cap is removed. outputs that satisfy the requirements of the necessary safety category. F3SJ-E F3SJ-B F3SJ-A Do not connect each line of F3SJ to a DC power supply higher than 24 V+20%. Also, do not connect to an AC power supply. Failure to do so may result in electric shock. 18 F3SJ-E/F3SJ-B/F3SJ-A F3SJ-E F3SJ-B F3SJ-A Installation Conditions For F3SJ to comply with IEC 61496-1 and UL 508, the DC power Detection Zone and Approach F3SJ-E F3SJ-B F3SJ-A supply unit must satisfy all of the following conditions: WARNINGMust be within rated power voltage (24 VDC±20%). Must have tolerance against the total rated current of devices if it Install a protective structure so that the hazardous part of a is connected to multiple devices. machine can only be reached by passing through the sensor's Must comply with EMC directives (industrial environment) detection zone. Install the sensors so that part of the person is Double or enhanced insulation must be applied between the always present in the detection zone when working in a primary and secondary circuits machine's hazardous zones. Automatic recovery of overcurrent protection characteristics If a person is able to step into the hazardous zone of a machine (reversed L sagging) and remain behind the F3SJ's detection zone, configure the Output holding time must be 20 ms or longer system with an interlock function that prevents the machine Must satisfy output characteristic requirements for class 2 circuit or from being restarted. Failure to do so may result in serious limited voltage current circuit defined by UL 508 injury. Must comply with EMC, laws, and regulations of a country or a region where F3SJ is used. (Ex: In EU, the power supply must Install the interlock reset switch in a location that provides a clear comply to the EMC Low Voltage Directive) view of the entire hazardous zone and where it cannot be activated from within the hazardous zone. F3SJ-E F3SJ-B F3SJ-A Double or enhanced insulation from hazardous voltage must be The F3SJ cannot protect a person from a projectile exiting the applied to all input and output lines. Failure to do so may result hazardous zone. Install protective cover(s) or fence(s). in electric shock. F3SJ-E F3SJ-B F3SJ-A Right positions Note: Keep the cable length within the rated length. Failure to do The hazardous zone of a machine can be reached only by so is dangerous as it may prevent safety functions from passing through the sensor's detection zone. operating normally. F3SJ-E F3SJ-B F3SJ-A Make sure to perform wiring while the power supply is OFF. Others F3SJ-E F3SJ-B F3SJ-A WARNING To use the F3SJ in PSDI mode (Reinitiation of cyclic operation by the protective equipment), you must configure an appropriate While working, a person is inside the sensor's detection zone. circuit between the F3SJ and the machine. For details about PSDI, refer to OSHA1910.217, IEC 61496-1, and other relevant standards and regulations. Do not try to disassemble, repair, or modify this product. Doing so may cause the safety functions to stop working properly. Do not use the F3SJ in environments where flammable or explosive gases are present. Doing so may result in explosion. Perform daily and 6-month inspections for the F3SJ. Otherwise, Incorrect installation the system may fail to work properly, resulting in serious injury. It is possible to reach the hazardous zone of a machine without passing through the sensor's detection zone. Do not use radio equipment such as cellular phones, walkie- talkies, or transceivers near the F3SJ. Note: For customers using the F3SJ-B@@@@P25-01TS: The functions available are external test, lockout reset, auxiliary output and series connection. A person is between the sensor's detection zone and the hazardous zone of a machine. 19 F3SJ-E/F3SJ-B/F3SJ-A Safety Distance F3SJ-E F3SJ-B F3SJ-A If the result exceeds 500 mm, use the following formula where K = 1,600 mm/s. The safety distance is the distance that must be set between the F3SJ S = 1,600 mm/s x (Tm + Ts) + 8 x (d - 14 mm) . . . Formula (3) and a machine's hazardous part to stop the hazardous part before a person or object reaches it. The safety distance varies according to If the result of this Eq. (3) is less than 500 mm, the standards of each country and the individual specifications of S = 500 mm each machine. In addition, the calculation of the safety distance differs if the direction of approach is not vertical to the detection zone System that has a detection capability larger than 40 mm of the F3SJ. Always refer to relevant standards. Use K = 1,600 mm/s and C = 8 x (d - 850 mm) in equation (1) for the calculation. Safety distance (S) S = 1,600 mm/s x (Tm + Ts) + 850 x (d - 14 mm) ... Formula (4) S = Safety distance (mm) Tm = Machine's response time (s) Ts = Response time of the F3SJ from ON to OFF (s) Hazard [Calculation example] When Tm = 0.05 s, Ts = 0.01 s: S = 1,600 mm/s x (0.05 s + 0.01 s) + 850 mm = 946 mm How to calculate the safety distance specified by American standard ANSI B11.19 (Ref.) WARNING If a person approaches the detection zone of the F3SJ Make sure to secure the safety distance (S) between the F3SJ perpendicularly, calculate the safety distance as shown below. and the hazardous part. Failure to do so may prevent the S = K x (Ts + Tc + Tr + Tbm) + Dpf machinery from stopping before a person reaches the S: Safety distance hazardous part of the machinery, and result in serious injury. K: Approach speed to the detection zone (the value recommended by OSHA standard is 1,600 mm/s) Note: The response time of a machine is the time period from when the machine receives a stop signal to when the machine's Approach speed K is not specified in the ANSI B.11.19 standard. hazardous part stops. Measure the response time on the actual To determine the value of K to apply, consider all factors, including system. Also, periodically check that the response time of the the operator's physical ability. machine has not changed. Ts = Machine's stop time (s) Ts = Response time of the F3SJ from ON to OFF (s) How to calculate the safety distance specified by Tc = Machine control circuit's maximum response time required International Standard ISO 13855 (European Standard EN ISO 13855) (Reference) to activate its brake (s) If a person approaches the detection zone of the F3SJ Tbm = Additional time (s) perpendicularly If a machine has a brake monitor, "Tbm = Brake monitor setting S = K x T + C . . . Formula (1) time - (Ts + Tc)". If it has no brake monitor, we recommend using S: Safety distance 20% or more of (Ts + Tc) as additional time. K: Approach speed to the detection zoneDpf = Additional distance T: Total response time of the machine and F3SJ According to ANSI's formula, Dpf is calculated as shown below: C: Additional distance calculated by the detection capability of Dpf = 3.4 x (d - 7.0): Where d is the detection capability of the F3SJ (unit: mm) the F3SJ [Calculation example] System that has detection capability of 40 mm max. When K = 1,600 mm/s, Ts + Tc = 0.06 s, brake monitor setting time Use K = 2,000 mm/s and C = 8 x (d - 14 mm) in equation (1) for the = 0.1 s, Tr = 0.01 s, and d = 14 mm: calculation. Tbm = 0.1 - 0.06 = 0.04 s S = 2,000 mm/s x (Tm + Ts) + 8 x (d - 14 mm) Dpf = 3.4 x (14 - 7.0) = 23.8 mm S = Safety distance (mm) S = 1,600 mm/s x (0.06 s + 0.01 s + 0.04 s) + 23.8 mm = 199.8 mm Tm = Machine's response time (s) Ts = Response time of the F3SJ from ON to OFF (s) d = Size of F3SJ's detection capability (mm) [Calculation example] When Tm = 0.05 s, Ts = 0.01 s, and d = 14 mm: S = 2,000 mm/s x (0.05 s + 0.01 s) + 8 x (14 mm - 14 mm) = 120 mm . . . Eq. (2) If the result is less than 100 mm, use S = 100 mm. 20 F3SJ-E/F3SJ-B/F3SJ-A Distance from Reflective Surface F3SJ-E F3SJ-B F3SJ-A Mutual Interference Prevention F3SJ-E F3SJ-B F3SJ-A WARNING WARNING Install the sensor system so that it is not affected by reflection Do not use the sensor system with mirrors in a regressive from a reflective surface. Failure to do so may hinder detection, reflective configuration. Doing so may hinder detection. It is resulting in serious injury. possible to use mirrors to "bend" the detection zone to a 90- degree angle. Install the sensor system at distance D or further from highly reflective surfaces such as metallic walls, floors, ceilings, or When using more than 1 set of F3SJ, install them so that mutual workpieces, as shown below. interference does not occur, such as by configuring series connections or using physical barriers between adjacent sets. Reflective ceiling Mutual interference from other F3SJ is prevented in up to 3 sets without series connection. D For series connection F3SJ-B F3SJ-A Emitter Receiver Series connection can prevent mutual interference when multiple sensors are used. Up to 3 sets with 192 beam for F3SJ-B series, or up to 4 sets with 400 beams for F3SJ-A series can be series- Detection zone connected. Emission of series-connected F3SJ is time-divided, ensuring safety without occurring mutual interference. L Receiver 1 Emitter 1 D Reflective floor Receiver 2 Emitter 2 Reflective surface D Receiver 3 Emitter 3 Emitter Receiver 5° 5° L Distance between emitter and Allowable installation receiver distance D (operating range L) For 0.2 to 3 m 0.13 m For 3 m or more L/2 x tan5° = L x 0.044 (m) 21 F3SJ-E/F3SJ-B/F3SJ-A No series connections F3SJ-B F3SJ-A Mutual interference is prevented in up to three sets, using interference light detection and cycle shift algorithm. If 4 or more sets of F3SJs are installed and are not connected to each other, arrange them so that mutual interference does not occur. If two sets are installed near each other, reflection from the surface of Aligned horizontally Aligned vertically the F3SJ may cause mutual interference. When mutual interference Emitter 1 Receiver 1 Emitter 2 Receiver 2 Emitter 1 Receiver 1 occurs, the safety outputs are turned OFF momentarily or the F3SJ enters lockout state. Combining countermeasures 1 to 3 shown below is effective. 1. Install a physical barrier Emitter 1 Receiver 1 Emitter 2 Receiver 2 Emitter 2 Receiver 2 Aligned fore and aft Emitter 1 Receiver 1 Emitter 2 Receiver 2 2. Alternate the direction of emission (alternation) F3SJ-A Aligned horizontally Aligned vertically If two sets are installed near each other, reflection from the surface of Receiver 1 Emitter 1 Emitter 2 Receiver 2 Emitter 1 Receiver 1 the F3SJ may cause mutual interference. Use of F3SJ-A can improve the condition by shortening operating range with the setting tool. < Before the change > Emitter Receiver Receiver 2 Emitter 2 Interference light Aligned fore and aft Receiver 1 Emitter 1 Emitter Receiver < After the change > Emitter 2 Receiver 2 Emitter Receiver Interference light 3. Keep sufficient distance between the F3SJs so that mutual interference does not occur Emitter Receiver Emitter Receiver Emitter Receiver 5° D D Emitter Receiver Emitter Receiver 5° L Distance between emitter and Allowable installation receiver distance D (operating range L) For 0.2 to 3 m 0.26 m For 3 m or more L x tan5° = L x 0.088 (m) Installation shown below may cause mutual interference. When mutual interference occurs, the safety outputs are turned OFF momentarily or the F3SJ enters lockout state. 22 F3SJ-E/F3SJ-B/F3SJ-A Related Manuals Man. No. Model Manual name SCHG-718 F3SJ-A@@@@P@@ F3SJ-A@@@@P@@ (Ver.2) Safety Light Curtain User's Manual SCHG-720 F3SJ-A@@@@P@@-TS F3SJ-A@@@@P@@-TS Safety Light Curtain User's Manual SCHG-722 F3SJ-A@@@@P20-01TS F3SJ-A@@@@P20-01TS Safety Light Curtain User's Manual SCHG-719 F3SJ-A@@@@N@@ F3SJ-A@@@@N@@(Ver.2) Safety Light Curtain User's Manual SCHG-726 F3SJ-A@@@@N@@-01T F3SJ-A@@@@N@@-01T(Ver.2) Safety Light Curtain User's Manual SCHG-716 F3SJ-AM@P@@@ F3SJ-AM@P@@@(Ver.2) Multi-beam Safety Sensor User's Manual SCHG-734 F3SJ-B@@@@P25-01TS F3SJ-B@@@@P25-01TS Safety Light Curtain User's Manual SCHG-733 F3SJ-E@@@@N25/B@@@@N25 F3SJ-E@@@@N25/B@@@@N25 Safety Light Curtain User's Manual SCHG-732 F3SJ-E@@@@P25/B@@@@P25 F3SJ-E@@@@P25/B@@@@P25 Safety Light Curtain User's Manual SCHG-712 F39-MC21 F39-MC21 F39-MC21 Setting Console Instruction Sheet SCHG-736 F3SJ-B@@@@P25-02TS F3SJ-B@@@@P25-02TS Safety Light Curtain User's Manual 23 Terms and Conditions of Sale 1. Offer; Acceptance. These terms and conditions (these "Terms") are deemed ITY OR FITNESS FOR A PARTICULAR PURPOSE OF THE PRODUCTS. part of all quotes, agreements, purchase orders, acknowledgments, price lists, BUYER ACKNOWLEDGES THAT IT ALONE HAS DETERMINED THAT THE catalogs, manuals, brochures and other documents, whether electronic or in PRODUCTS WILL SUITABLY MEET THE REQUIREMENTS OF THEIR writing, relating to the sale of products or services (collectively, the "Products") INTENDED USE. Omron further disclaims all warranties and responsibility of by Omron Electronics LLC and its subsidiary companies (“Omron”). Omron any type for claims or expenses based on infringement by the Products or oth- objects to any terms or conditions proposed in Buyer’s purchase order or other erwise of any intellectual property right. (c) Buyer Remedy. Omron’s sole obli- documents which are inconsistent with, or in addition to, these Terms. gation hereunder shall be, at Omron’s election, to (i) replace (in the form 2. Prices; Payment Terms. All prices stated are current, subject to change with- originally shipped with Buyer responsible for labor charges for removal or out notice by Omron. Omron reserves the right to increase or decrease prices replacement thereof) the non-complying Product, (ii) repair the non-complying on any unshipped portions of outstanding orders. Payments for Products are Product, or (iii) repay or credit Buyer an amount equal to the purchase price of due net 30 days unless otherwise stated in the invoice. the non-complying Product; provided that in no event shall Omron be responsi- 3. Discounts. Cash discounts, if any, will apply only on the net amount of invoices ble for warranty, repair, indemnity or any other claims or expenses regarding sent to Buyer after deducting transportation charges, taxes and duties, and will the Products unless Omron’s analysis confirms that the Products were prop- be allowed only if (i) the invoice is paid according to Omron’s payment terms erly handled, stored, installed and maintained and not subject to contamina- and (ii) Buyer has no past due amounts. tion, abuse, misuse or inappropriate modification. Return of any Products by 4. Interest. Omron, at its option, may charge Buyer 1-1/2% interest per month or Buyer must be approved in writing by Omron before shipment. Omron Compa- the maximum legal rate, whichever is less, on any balance not paid within the nies shall not be liable for the suitability or unsuitability or the results from the stated terms. use of Products in combination with any electrical or electronic components, 5. Orders. Omron will accept no order less than $200 net billing. circuits, system assemblies or any other materials or substances or environ- 6. Governmental Approvals. Buyer shall be responsible for, and shall bear all ments. Any advice, recommendations or information given orally or in writing, costs involved in, obtaining any government approvals required for the impor- are not to be construed as an amendment or addition to the above warranty. tation or sale of the Products. See http://www.omron247.com or contact your Omron representative for pub- 7. Taxes. All taxes, duties and other governmental charges (other than general lished information. real property and income taxes), including any interest or penalties thereon, 14. Limitation on Liability; Etc. OMRON COMPANIES SHALL NOT BE LIABLE imposed directly or indirectly on Omron or required to be collected directly or FOR SPECIAL, INDIRECT, INCIDENTAL, OR CONSEQUENTIAL DAMAGES, indirectly by Omron for the manufacture, production, sale, delivery, importa- LOSS OF PROFITS OR PRODUCTION OR COMMERCIAL LOSS IN ANY tion, consumption or use of the Products sold hereunder (including customs WAY CONNECTED WITH THE PRODUCTS, WHETHER SUCH CLAIM IS duties and sales, excise, use, turnover and license taxes) shall be charged to BASED IN CONTRACT, WARRANTY, NEGLIGENCE OR STRICT LIABILITY. and remitted by Buyer to Omron. Further, in no event shall liability of Omron Companies exceed the individual 8. Financial. If the financial position of Buyer at any time becomes unsatisfactory price of the Product on which liability is asserted. to Omron, Omron reserves the right to stop shipments or require satisfactory 15. Indemnities. Buyer shall indemnify and hold harmless Omron Companies and security or payment in advance. If Buyer fails to make payment or otherwise their employees from and against all liabilities, losses, claims, costs and comply with these Terms or any related agreement, Omron may (without liabil- expenses (including attorney's fees and expenses) related to any claim, inves- ity and in addition to other remedies) cancel any unshipped portion of Prod- tigation, litigation or proceeding (whether or not Omron is a party) which arises ucts sold hereunder and stop any Products in transit until Buyer pays all or is alleged to arise from Buyer's acts or omissions under these Terms or in amounts, including amounts payable hereunder, whether or not then due, any way with respect to the Products. Without limiting the foregoing, Buyer (at which are owing to it by Buyer. Buyer shall in any event remain liable for all its own expense) shall indemnify and hold harmless Omron and defend or set- unpaid accounts. tle any action brought against such Companies to the extent based on a claim 9. Cancellation; Etc. Orders are not subject to rescheduling or cancellation that any Product made to Buyer specifications infringed intellectual property unless Buyer indemnifies Omron against all related costs or expenses. rights of another party. . Omron shall not be liable for any delay or failure in delivery Any intellectual property in the Products is the exclu- 10. Force Majeure 16. Property; Confidentiality. resulting from causes beyond its control, including earthquakes, fires, floods, sive property of Omron Companies and Buyer shall not attempt to duplicate it strikes or other labor disputes, shortage of labor or materials, accidents to in any way without the written permission of Omron. Notwithstanding any machinery, acts of sabotage, riots, delay in or lack of transportation or the charges to Buyer for engineering or tooling, all engineering and tooling shall requirements of any government authority. remain the exclusive property of Omron. All information and materials supplied 11. Shipping; Delivery. Unless otherwise expressly agreed in writing by Omron: by Omron to Buyer relating to the Products are confidential and proprietary, a. Shipments shall be by a carrier selected by Omron; Omron will not drop ship and Buyer shall limit distribution thereof to its trusted employees and strictly except in “break down” situations. prevent disclosure to any third party. b. Such carrier shall act as the agent of Buyer and delivery to such carrier shall 17. Export Controls. Buyer shall comply with all applicable laws, regulations and constitute delivery to Buyer; licenses regarding (i) export of products or information; (iii) sale of products to c. All sales and shipments of Products shall be FOB shipping point (unless oth- “forbidden” or other proscribed persons; and (ii) disclosure to non-citizens of erwise stated in writing by Omron), at which point title and risk of loss shall regulated technology or information. pass from Omron to Buyer; provided that Omron shall retain a security inter- 18. Miscellaneous. (a) Waiver. No failure or delay by Omron in exercising any right est in the Products until the full purchase price is paid; and no course of dealing between Buyer and Omron shall operate as a waiver d. Delivery and shipping dates are estimates only; and of rights by Omron. (b) Assignment. Buyer may not assign its rights hereunder e.Omron will package Products as it deems proper for protection against nor- without Omron's written consent. (c) Law. These Terms are governed by the mal handling and extra charges apply to special conditions. law of the jurisdiction of the home office of the Omron company from which 12. Claims. Any claim by Buyer against Omron for shortage or damage to the Buyer is purchasing the Products (without regard to conflict of law princi- Products occurring before delivery to the carrier must be presented in writing ples). (d) Amendment. These Terms constitute the entire agreement between to Omron within 30 days of receipt of shipment and include the original trans- Buyer and Omron relating to the Products, and no provision may be changed . If any provi- portation bill signed by the carrier noting that the carrier received the Products or waived unless in writing signed by the parties. (e) Severability from Omron in the condition claimed. sion hereof is rendered ineffective or invalid, such provision shall not invalidate 13. Warranties. (a) Exclusive Warranty. Omron’s exclusive warranty is that the any other provision. (f) Setoff. Buyer shall have no right to set off any amounts Products will be free from defects in materials and workmanship for a period of against the amount owing in respect of this invoice. (g) Definitions. As used twelve months from the date of sale by Omron (or such other period expressed herein, “including” means “including without limitation”; and “Omron Compa- in writing by Omron). Omron disclaims all other warranties, express or implied. nies” (or similar words) mean Omron Corporation and any direct or indirect (b) Limitations. OMRON MAKES NO WARRANTY OR REPRESENTATION, subsidiary or affiliate thereof. EXPRESS OR IMPLIED, ABOUT NON-INFRINGEMENT, MERCHANTABIL- Certain Precautions on Specifications and Use 1. Suitability of Use. Omron Companies shall not be responsible for conformity ADDRESS THE RISKS, AND THAT THE OMRON’S PRODUCT IS PROP- with any standards, codes or regulations which apply to the combination of the ERLY RATED AND INSTALLED FOR THE INTENDED USE WITHIN THE Product in the Buyer’s application or use of the Product. At Buyer’s request, OVERALL EQUIPMENT OR SYSTEM. Omron will provide applicable third party certification documents identifying 2. Programmable Products. Omron Companies shall not be responsible for the ratings and limitations of use which apply to the Product. This information by user’s programming of a programmable Product, or any consequence thereof. itself is not sufficient for a complete determination of the suitability of the Prod- 3. Performance Data. Data presented in Omron Company websites, catalogs uct in combination with the end product, machine, system, or other application and other materials is provided as a guide for the user in determining suitabil- or use. Buyer shall be solely responsible for determining appropriateness of ity and does not constitute a warranty. It may represent the result of Omron’s the particular Product with respect to Buyer’s application, product or system. test conditions, and the user must correlate it to actual application require- Buyer shall take application responsibility in all cases but the following is a ments. Actual performance is subject to the Omron’s Warranty and Limitations non-exhaustive list of applications for which particular attention must be given: of Liability. (i) Outdoor use, uses involving potential chemical contamination or electrical 4. Change in Specifications. Product specifications and accessories may be interference, or conditions or uses not described in this document. changed at any time based on improvements and other reasons. It is our prac- (ii) Use in consumer products or any use in significant quantities. tice to change part numbers when published ratings or features are changed, (iii) Energy control systems, combustion systems, railroad systems, aviation or when significant construction changes are made. However, some specifica- systems, medical equipment, amusement machines, vehicles, safety equip- tions of the Product may be changed without any notice. When in doubt, spe- ment, and installations subject to separate industry or government regulations. cial part numbers may be assigned to fix or establish key specifications for (iv) Systems, machines and equipment that could present a risk to life or prop- your application. Please consult with your Omron’s representative at any time erty. Please know and observe all prohibitions of use applicable to this Prod- to confirm actual specifications of purchased Product. uct. 5. Errors and Omissions. Information presented by Omron Companies has been NEVER USE THE PRODUCT FOR AN APPLICATION INVOLVING SERIOUS checked and is believed to be accurate; however, no responsibility is assumed RISK TO LIFE OR PROPERTY OR IN LARGE QUANTITIES WITHOUT for clerical, typographical or proofreading errors or omissions. ENSURING THAT THE SYSTEM AS A WHOLE HAS BEEN DESIGNED TO OMRON AUTOMATION AND SAFETY • THE AMERICAS HEADQUARTERS • Chicago, IL USA • 847.843.7900 • 800.556.6766 • www.omron247.com OMRON CANADA, INC. • HEAD OFFICE OMRON ARGENTINA • SALES OFFICE Toronto, ON, Canada • 416.286.6465 • 866.986.6766 • www.omron247.com Cono Sur • 54.11.4783.5300 OMRON ELECTRONICS DE MEXICO • HEAD OFFICE OMRON CHILE • SALES OFFICE México DF • 52.55.59.01.43.00 • 01-800-226-6766 • mela@omron.com Santiago • 56.9.9917.3920 OMRON ELECTRONICS DE MEXICO • SALES OFFICE OTHER OMRON LATIN AMERICA SALES Apodaca, N.L. • 52.81.11.56.99.20 • 01-800-226-6766 • mela@omron.com 54.11.4783.5300 OMRON ELETRÔNICA DO BRASIL LTDA • HEAD OFFICE São Paulo, SP, Brasil • 55.11.2101.6300 • www.omron.com.br OMRON EUROPE B.V. • Wegalaan 67-69, NL-2132 JD, Hoofddorp, The Netherlands. • +31 (0) 23 568 13 00 • www.industrial.omron.eu Authorized Distributor: Automation Control Systems • Machine Automation Controllers (MAC) • Programmable Controllers (PLC) • Operator interfaces (HMI) • Distributed I/O • Software Drives & Motion Controls • Servo & AC Drives • Motion Controllers & Encoders Temperature & Process Controllers • Single and Multi-loop Controllers Sensors & Vision • Proximity Sensors • Photoelectric Sensors • Fiber-Optic Sensors • Amplified Photomicrosensors • Measurement Sensors • Ultrasonic Sensors • Vision Sensors Industrial Components • RFID/Code Readers • Relays • Pushbuttons & Indicators • Limit and Basic Switches • Timers • Counters • Metering Devices • Power Supplies Safety • Laser Scanners • Safety Mats • Edges and Bumpers • Programmable Safety Controllers • Light Curtains • Safety Relays • Safety Interlock Switches F25I-E-01 12/14 Note: Specifications are subject to change. © 2014 Omron Electronics LLC Printed in U.S.A. Printed on recycled paper.
Frequently asked questions
How does Electronics Finder differ from its competitors?

Is there a warranty for the F3SJ-E0625P25?

Which carrier will Electronics Finder use to ship my parts?

Can I buy parts from Electronics Finder if I am outside the USA?

Which payment methods does Electronics Finder accept?

Why buy from GID?
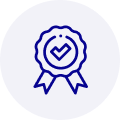
Quality
We are industry veterans who take pride in our work
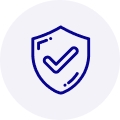
Protection
Avoid the dangers of risky trading in the gray market
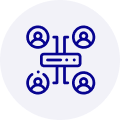
Access
Our network of suppliers is ready and at your disposal
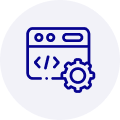
Savings
Maintain legacy systems to prevent costly downtime
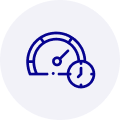
Speed
Time is of the essence, and we are respectful of yours
What they say about us
FANTASTIC RESOURCE
One of our top priorities is maintaining our business with precision, and we are constantly looking for affiliates that can help us achieve our goal. With the aid of GID Industrial, our obsolete product management has never been more efficient. They have been a great resource to our company, and have quickly become a go-to supplier on our list!
Bucher Emhart Glass
EXCELLENT SERVICE
With our strict fundamentals and high expectations, we were surprised when we came across GID Industrial and their competitive pricing. When we approached them with our issue, they were incredibly confident in being able to provide us with a seamless solution at the best price for us. GID Industrial quickly understood our needs and provided us with excellent service, as well as fully tested product to ensure what we received would be the right fit for our company.
Fuji
HARD TO FIND A BETTER PROVIDER
Our company provides services to aid in the manufacture of technological products, such as semiconductors and flat panel displays, and often searching for distributors of obsolete product we require can waste time and money. Finding GID Industrial proved to be a great asset to our company, with cost effective solutions and superior knowledge on all of their materials, it’d be hard to find a better provider of obsolete or hard to find products.
Applied Materials
CONSISTENTLY DELIVERS QUALITY SOLUTIONS
Over the years, the equipment used in our company becomes discontinued, but they’re still of great use to us and our customers. Once these products are no longer available through the manufacturer, finding a reliable, quick supplier is a necessity, and luckily for us, GID Industrial has provided the most trustworthy, quality solutions to our obsolete component needs.
Nidec Vamco
TERRIFIC RESOURCE
This company has been a terrific help to us (I work for Trican Well Service) in sourcing the Micron Ram Memory we needed for our Siemens computers. Great service! And great pricing! I know when the product is shipping and when it will arrive, all the way through the ordering process.
Trican Well Service
GO TO SOURCE
When I can't find an obsolete part, I first call GID and they'll come up with my parts every time. Great customer service and follow up as well. Scott emails me from time to time to touch base and see if we're having trouble finding something.....which is often with our 25 yr old equipment.
ConAgra Foods